Strategic Approach
SUSTAINABLE DEVELOPMENT MILESTONES
- The Integrated Annual Report was based on the GRI non-financial reporting standards for the first time.
- The Company developed Corporate and Social Responsibility Sustainability Programme 2017-2019.
- Kazatomprom developed and published Sustainable Development Policy.
- The Company reinforced the corporate sustainability management function by establishing a dedicated unit, the Sustainable Development Department.
- The Integrated Annual Report includes information on sustainability management approaches and the Company's contribution to achieving the UN global sustainable development goals (UN SDGs).
- The Company identified priority UN SDGs and key targets for each of the UN SDGs.
- The ESG information in the 2020 Integrated Annual Report was independently assured in line with global best practices for the first time.
- More GRI indicators disclosed.
- Kazatomprom started work on climate risk management.
- The Company identified sustainable development risks.
- The 2021 Integrated Annual Report included key indicators of achievement of the UN Conference on Trade and Development (UNCTAD) Sustainable Development Goals.
- The Company successfully passed the first supervisory audit and confirmed its certificate from the TÜV International Certification (Germany) in accordance with the requirements of two international standards, ISO 45001 and ISO 14001.
- All enterprises of the Group have the ISO 50001 energy management system in place. Energy audits were regularly conducted as part of the Group's energy management systems.
- The Company identified and assessed climate risks.
- The Company developed the Decarbonisation and Carbon Neutrality of NAC Kazatomprom JSC until 2060.
- The Company developed Kazatomprom Human Rights Policy.
- Kazatomprom joined UN Global Compact
- The Company extended the list of GRI disclosures.
- Kazatomprom made disclosures as recommended by the Task Force on Climate-related Financial Disclosures (TCFD).
- Kazatomprom received its first independent ESG rating from leading international rating agency S&P Global Ratings.
- The Company received the first international climate CDP (Carbon Disclosure Project) rating at the level "B" ("governance").
- Kazatomprom received a CSA (Corporate Sustainability Assessment) rating of 41/100 from leading international rating agency S&P Global Ratings.
- The Company's Board of Directors approved the Sustainable Development Programme of NAC Kazatomprom JSC for 2023-2030.
- The Company’s Board of Directors approved the Water Resources Management Strategy of NAC Kazatomprom JSC for 2023-2030.
- The Company implements the Roadmap for improving ESG practices in NAC Kazatomprom JSC for 2023-2024.
- Kazatomprom developed the Radioactive Waste Management Programme for 2023-2030.
- The Company disclosed information in accordance with SASB standards.
- Kazatomprom included climate risks in the Company's risk register.
- The Company held an annual town hall for the Group's employees dedicated to sustainable development of the uranium mining industry in Kazakhstan.
- Kazatomprom participated in the UN Global Compact Programme SDG Ambition.
- Update CSA (Corporate Sustainability Assessment)/receive an independent ESG rating.
- Update the international climate CDP rating (Carbon Disclosure Project).
- Implement the Sustainable Development Programme of NAC Kazatomprom JSC for 2023-2030.
- Implement the Road Map to improve ESG practices at Kazatomprom in 2023-2024.
- Develop, get approval and implement the Comprehensive Action Plan on the Water Resources Management Strategy for 2023-2030.
- Prepare for information disclosure in accordance with IFRS S2.
- Hold events for employees of the Group to raise awareness and promote adherence to ESG principles.
OUR APPROACH
Kazatomprom strives to comply with the principles of sustainable development across its operations and promotes responsible business and social responsibility practices among its partners, suppliers, and other stakeholders. The principles of sustainable development lie at the core of the Company's operations. Compliance with these principles is vital not only for long-term business development but also for instilling Kazatomprom's core corporate values.
When determining priority sustainability areas, Kazatomprom follows the principles of the UN Global Compact and the UN Sustainable Development Goals 2030 (UN SDGs), as well as other international standards and initiatives in this area.
Principles of sustainable development of NAC Kazatomprom JSC
Kazatomprom’s priority areas of sustainable development
Areas | UN SDGs |
---|---|
Economic sustainability |
|
Human capital and culture development |
|
Health and safety |
|
Environmental responsibility |
|
R&D, innovations, and technological development |
|
Effective corporate governance and risk culture |
|
High ethical standards and anti-corruption measures |
|
Responsible procurement |
|
Responsible business practices – engagement with stakeholders and local communities and reporting |
|
The Company integrates sustainability issues at all management levels. At the top of the hierarchy, the Board of Directors pays special attention to this topic, considering it as strategic priority. The Board of Directors approves and monitors the implementation of the Company's Development Strategy. The Strategy integrates Kazatomprom's sustainable development principles and goals, as well as other programme and planning documents containing goals, values and processes related to the Company's sustainable development. The Board of Directors is provided with reports on sustainable development areas and processes on a regular basis (annual, quarterly). When considering them, if necessary, the Board of Directors members discuss these issues with stakeholders (Company employees, external stakeholders, etc.). The Board of Directors review such reports at regular and extraordinary meetings. Committees within the Board of prepare recommendations to the Board of Directors on the introduction and implementation of sustainable development principles and strategic objectives in this area. At the management level, the Company's Management Board directly supervises the implementation of strategic plans, programmes and initiatives, monitors the achievement of established goals and the effectiveness of sustainable development activities. We distribute tasks in specific areas of sustainable development among the relevant Company’s divisions at the centralised level and in subsidiaries and affiliates at the local level. This ensures holistic and effective management in this important area.
The Company reviews the list of material topics to be disclosed in the Company's non-financial statements on the annual basis. The Board of Directors approves it as part of the Company's Integrated Annual Report.
The Company has adopted a number of internal documents governing sustainability aspects and business processes on good governance and integrity, health and safety, environmental protection, personnel management, community involvement, and supply chain management.
Promoting sustainability standards and initiatives
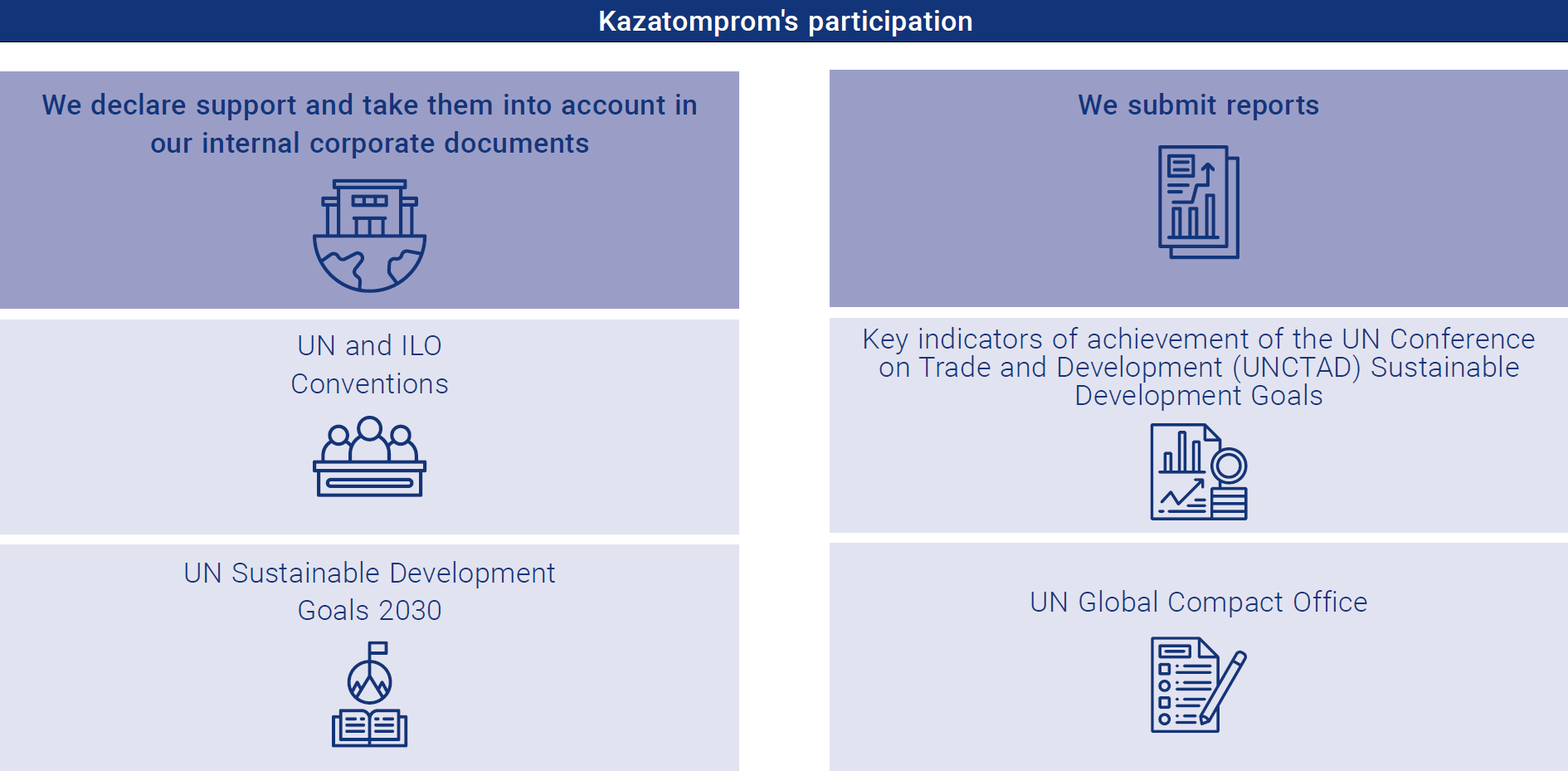
In November 2023, the Board of Directors of NAC Kazatomprom JSC approved the Company's Sustainable Development Programme for 2023-2030.
The Programme aims to implement the Company's Development Strategy according to the sustainable development principles to ensure growth in shareholder value and value-added in the long term for the benefit of all stakeholder groups through active management of economic, social and environmental impacts.
Programme objectives in accordance with the UN SDGs:
Environmental protection
Sustainable consumption and lean production
Biodiversity conservation
Support and promotion of global initiatives in the field of ecology and biodiversity
Achieving zero fatal injuries
Safety Culture improvement
Coverage of contractors and suppliers with the Company's industrial safety system
Attracting and retaining qualified personnel
Increasing social stability and employee engagement
Development of regions of presence
Health care and welfare of employees
Striving for gender equality
Ensuring respect for human rights
Zero tolerance for corruption
Improving the corporate governance system
Development of risk culture and compliance
Implementation of a responsible procurement system along the Company's supply chain
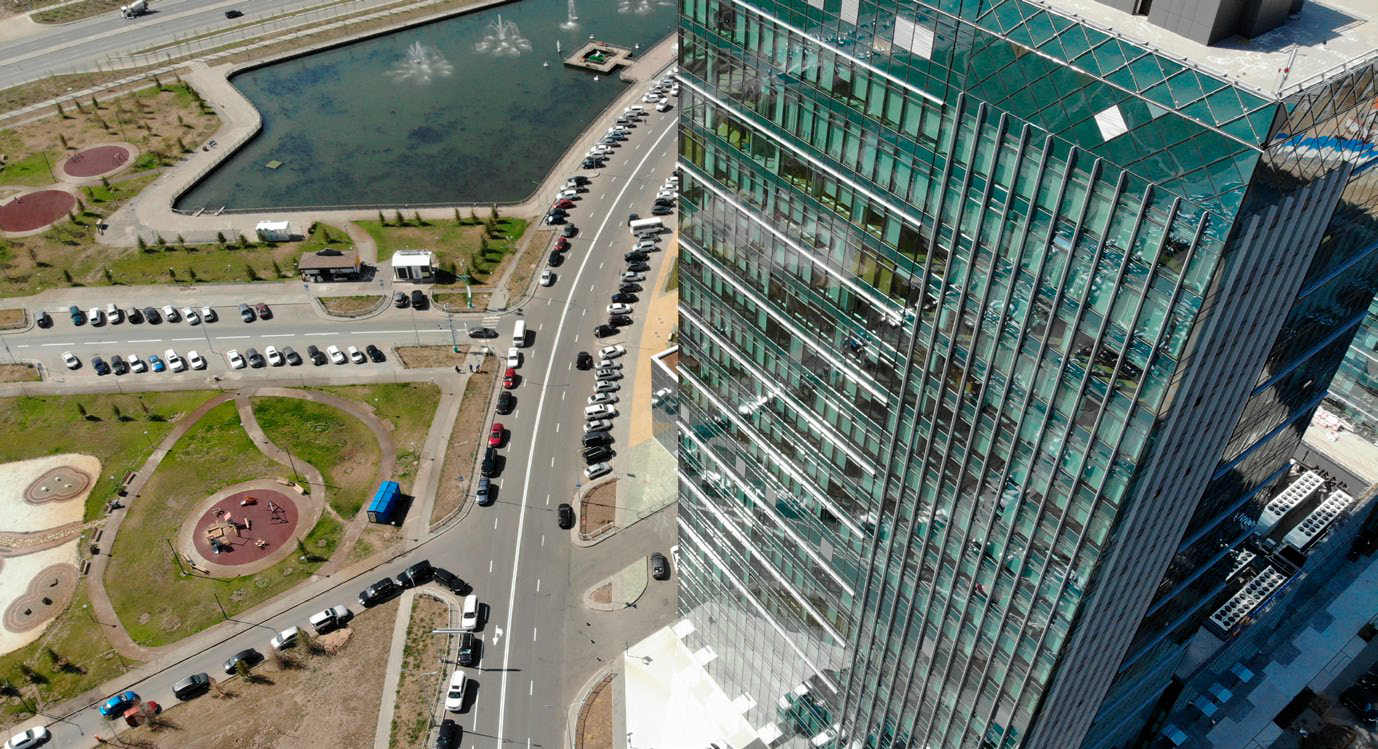
Expected key results of the Programme implementation by 2030:
- Increase in the Company's ESG rating/assessment by 10% from 2022 level.
- Reduction of the Company's greenhouse gas emissions under Scopes 1 and 2 by 10% from 2021 level.
- Increase in green electricity share (RES+AES) in the Company's energy mix to 10%.
- Increase in the economic efficiency of recycling by 40% from 2021 level.
- Increase in water reuse share up to 10%.
- Reduction in specific water consumption (m3/tonne
of production) by 2022 level:
- in uranium mining – by 15%;
- in uranium production (UMP JSC) – by 100%;
- in tantalum production (UMP JSC) – by 50%;
- in beryllium production (UMP JSC) – by 100%;
- in sulphuric acid production – by 5%.
- Elimination of liquid radioactive waste generation during natural uranium chemical concentrate processing per production unit.
- Elimination of fatal injuries at production facilities.
- Reduction of LTIFR indicator to 0.1.
- Reduction of staff turnover to 12%.
- Increase in the social stability level up to 77%.
- Increase in the share of women in the Holding's management bodies to 30%.
- Maintaining in-country value in the procurement of the Holding’s goods, works and services at the level of at least 50% for goods and 91% for works and services.
- 100% coverage of the Holding's employees trained in human rights protection on annual basis.
- 15-fold increase in the number of the Holding's supplier’s voluntary trained on ethics, compliance and ESG principles compared to 2022.
COMMITMENT TO THE UN GLOBAL COMPACT PRINCIPLES
In 2022, Kazatomprom joined the UN Global Compact initiative (UNGC) and continues to work towards this cause. The Global Compact's ten principles in the areas of human rights, employment, environment, and anticorruption are included in the substantive topics that the Company has identified as the most significant and relevant. Cooperation with the UNGC builds trust with the investment community, allows us to measure and demonstrate our progress in implementing the Ten Principles in a consistent and coherent manner, and provides an opportunity to benchmark our progress against that of other global companies.
Every year, UNGC participants publish a Progress Report, which is available on the official UNGC website. In June 2023, Kazatomprom released its first Progress Report. In addition, Kazatomprom employees have access to the UNGC's academic platform, where various workshops and conferences are held monthly, covering the most significant topics of the global ESG agenda.
№ | Principles | Section of the Report |
---|---|---|
1. | Businesses should support and respect the protection of internationally proclaimed human rights | HR management |
2. | Businesses should make sure that they are not complicit in human rights abuses | HR management |
3. | Businesses should uphold the freedom of association and the effective recognition of the right to collective bargaining | HR management |
4. | Businesses should uphold the elimination of all forms of forced and compulsory labour | HR management |
5. | Businesses should uphold the effective abolition of child labour | HR management |
6. | Businesses should uphold the elimination of discrimination in respect of employment and occupation | HR management |
7. | Businesses should support a precautionary approach to environmental challenges | Environmental sustainability |
8. | Businesses should undertake initiatives to promote greater environmental responsibility | Environmental sustainability |
9. | Businesses should encourage the development and diffusion of environmentally friendly technologies | Environmental sustainability |
10. | Businesses should work against all forms of corruption, including extortion and bribery | Corporate Ethics and Compliance |
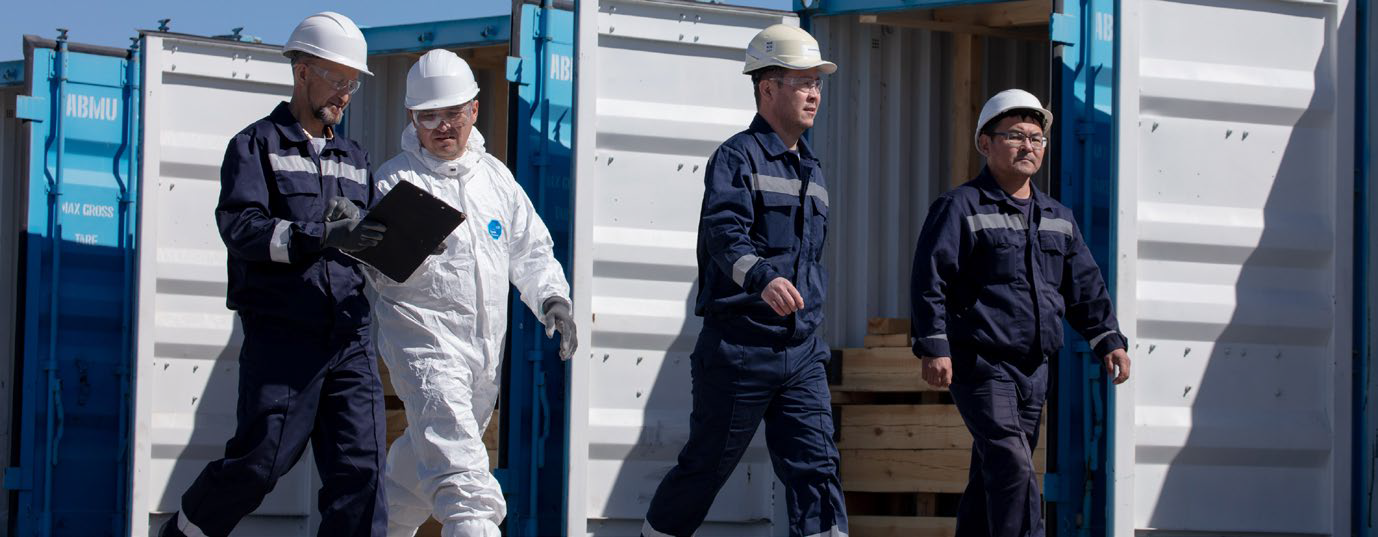
STAKEHOLDER ENGAGEMENT
Kazatomprom sees its mission as creating value for stakeholders in alignment with their interests and needs. To deliver on this mission, the Company is building a system of effective interaction with stakeholders, using various engagement methods and communication channels, and paying special attention to improving two-way communication systems and receiving feedback.
Key underlying documents regulating the Company’s stakeholder engagement are Kazatomprom Disclosure Policy and Stakeholder Map.
To identify and select stakeholders for further engagement, Kazatomprom relies on the assessment of the impact on its current operations and strategic development, as well as the established practice of the Company's engagement with external stakeholders and their dependence on its performance.
Stakeholder communication channels
- Analyst days.
- Performance conference calls.
- Surveys and questionnaires.
- Newsletters and mailouts.
- General and individual meetings.
- Direct contact by email and telephone.
- Sectoral events.
- Presentations.
- Corporate reporting.
- Official website.
- Publications in media.
- Social media.
- Grievance mechanisms.
The Company updates its stakeholder map annually. In 2023, a management survey confirmed the relevance of the map.
Kazatomprom stakeholder ranking map 2023
Stakeholder engagement mechanisms
Stakeholder’s interest in the Company | Stakeholder engagement mechanisms |
Shareholders | |
---|---|
Economic profit/consolidated net profit/economic performance Free funds for development and dividends Net asset value (NAV) Corporate governance rating Market share/Market presence Reduction of environmental emissions |
Decisions of the General Meeting of Shareholders of the Company, the Board of Directors and Management Board of the Fund, the Board of Directors of the Company Joint working groups, meetings, negotiations Discussion of the implementation status of sustainable development processes with the Fund Regular reporting to shareholders, including the Fund, in the agreed format Special session on sustainable development with the relevant Board of Directors Correspondence on the operations of the Group Surveys, questionnaires, testing Internal corporate communication channels Annual report and website of the Company |
Customers | |
Market share/Market presence Products and service labelling Marketing communications Reduction of environmental emissions |
Customer feedback Meetings, negotiations, questionnaires Signing of agreements, memoranda, and strategic cooperation agreements The Hotline Annual report and website of the Company |
Investment analysts | |
Analysis of various aspects of the Company's operations The Company's entering into analytical ratings |
Conferences, forums, annual meetings, analyst days, production site visit with investors Meetings, negotiations, questionnaires Annual report and website of the Company Quarterly operating results Quarterly financial statements and press releases |
Senior managers and staff | |
Employment, relations between employees and management, non-discrimination/diversity and equal opportunities/level of employee satisfaction with work and the work of Company-controlled services Training and education Improvements in the production safety culture |
Fair and transparent conditions for staff remuneration, professional growth of employees, safe working conditions Staff development Production safety briefings and implementation of programmes to improve working conditions Implementation of measures for social support of workers and members of their families Staff training, upskilling and development Regular meetings with management, negotiations Notification of employees on the Company's operations, professional growth opportunities through corporate magazines, social media Surveys, questionnaires, testing The Hotline, internal corporate communication channels, website of the Company |
Suppliers of goods, works, and services | |
Equal access to tenders Benefits from the implementation of category-based procurement strategies Support for domestic manufacturers |
Transparent procurement system with public access Regular analytical meetings, negotiations, business correspondence Signing of agreements, memoranda, strategic cooperation agreements, licensing Information/reporting on the implementation of production, investment and social plans and obligations forwarded to the Company Reporting on the Company's financial and economic performance Consideration of letters (requests) sent to the Company Surveys, questionnaires, testing The Hotline Annual report and website of the Company |
Business communities (Associations, National Chamber of Entrepreneurs, Union of Legal Entities) | |
Participation of the Company in improvements in and compliance with industry standards Participation of the Company in improvements to the business environment Support for the Company at the state authorities through mechanisms of interaction of the business environment with the state authorities, assistance with the promotion of the legislative initiatives of the Company |
Development of proposals on amendments and supplements to the laws of Kazakhstan Signing of agreements, memoranda, and strategic cooperation agreements Joint working groups, meetings, negotiations, questionnaires Annual report and website of the Company |
Partners | |
Market share/Market presence Unit production cost of U3O8 produced by the Company and all uranium mining subsidiaries |
Memorandums of association Decisions of the Company management bodies/participants of subsidiaries and affiliates, joint consultative and advisory bodies Joint working groups, joint inspections Meetings, negotiations, business correspondence, questionnaires Reports on current operations Correspondence on the operations of the Group of subsidiaries and affiliates Annual report and website of the Company |
Government authorities | |
Compliance, stability and business sustainability Creation and maintenance of jobs Representation of the country's economic interests in the international arena (economic, political and image benefits for the country through the prism of development of the uranium industry in Kazakhstan) Improvement in the energy and resource efficiency in production Reduction of environmental emissions |
Verification of the compliance by the Company’s subsidiaries and affiliates with licensing and contractual obligations Audit of compliance with the laws of Kazakhstan, development of proposals on amendments to the laws of the Republic of Kazakhstan Coordination of the subsoil use contracts and state registration of the right of subsoil use Information/reporting on the implementation of production, investment and social plans and obligations in line with requests Negotiations, business correspondence, control, production, operational and other meetings, questionnaires Reports on the performance by the Company’s subsidiaries and affiliates of licensing and contractual obligations, submission of quarterly reports to the Ministry of Energy of the Republic of Kazakhstan, reporting on the Company's financial and economic performance The Hotline Annual report and website of the Company |
International organisations | |
Participation of the Company in international agreements and initiatives |
Conferences, forums, annual meetings Signing of agreements, memoranda, and strategic cooperation agreements Joint working groups, meetings, negotiations, questionnaires Annual report and website of the Company |
Lenders | |
Economic profit/Consolidated net profit/Economic performance Free funds for development and dividends Net asset value (NAV) Investment and procurement practices/Benefits from the implementation of category-based procurement strategies |
Regular analytical meetings, negotiations, business correspondence, questionnaires Media coverage of the Company's operations The Hotline Annual report and website of the Company |
Local executive authorities | |
Compliance with requirements, creation and retention of workplaces, sponsorship and philanthropy Occupational health and safety of the employees of the Company Improvement in the energy and resource efficiency in production, reduction of environmental emissions |
Memoranda of cooperation between the local executive authorities and the Company to support and develop the social sector in the regions General agreements between the local executive authorities and the Company on financing the social sector in the regions The Hotline, social media Annual report and website of the Company |
CSOs and local communities | |
Improvements in the production safety culture Improvement in the energy and resource efficiency in production Reduction of environmental emissions Compliance with legislative requirements, sponsorship and philanthropy Training and education |
Public hearings Developing proposals to amend and supplement the laws of Kazakhstan Media coverage of the Company's operations Surveys, questionnaires, testing Information on the current operations of the Company, its subsidiaries and affiliates Handling letters (complaints, requests) sent to the Company The Hotline, social media Annual report and website of the Company |
Trade union | |
Creation and maintenance of jobs Improvements in the production safety culture |
Public hearings Signing of agreements, memoranda, and strategic cooperation agreements Regulation of employment relations with the employees of the Company through the collective bargaining agreement Remuneration of employees in accordance with the labour laws of Kazakhstan, training and education, safe working conditions Information on the current operations of the Company's subsidiaries and affiliates Receiving letters (complaints, requests) sent to the Company The Hotline, social media, internal corporate communication channels Annual report and website of the Company |
Subsidiaries and affiliates | |
Employment and level of remuneration, relations between employees and management, nondiscrimination, diversity and equal opportunities Improvements in the production safety culture, training and education Market share/Market presence, products and service labelling |
Decisions of the Company as a participant/shareholder of the subsidiaries and affiliates Reporting in accordance with the Non-Disclosure Agreement between Samruk-Kazyna and Kazatomprom Decisions of the management bodies of the Company, decisions of participant of subsidiaries and affiliates Audit of compliance with the laws of the Republic of Kazakhstan and the internal regulations of the Group Verification of the compliance by the Company’s subsidiaries and affiliates with licensing and contractual obligations Developing proposals to amend and supplement the laws of Kazakhstan Provision of information at the request of the government authorities on different lines of business of the Company Signing of agreements, memoranda, and strategic cooperation agreements Orders and instructions, hearings of management reports (subsidiaries and affiliates) Information/reporting on the implementation of production, investment and social plans and obligations forwarded to the Company Operational and other meetings, public hearings Production safety briefings, training and education The Hotline, social media, internal corporate communications channels, Annual report and the website of the Company |
Specialised organisations (including Samruk-Kazyna Trust Social Project Development Fund) | |
Implementation of projects and programmes aimed at addressing socially significant issues Function of a single operator of philanthropic efforts of the Samruk-Kazyna group |
Incoming and outgoing correspondence Business correspondence Meetings, negotiations, etc. Reports on current operations Media coverage of the Company's operations The Hotline Company’s website |
Stock exchanges | |
Compliance Timely submission of financial statements and other information |
Meetings and negotiations Company’s website Report Websites of exchange regulators |
CONSULTATIONS BETWEEN STAKEHOLDERS AND THE COMPANY
Kazatomprom has adopted specific procedures for conducting consultations on economic, environmental and social issues between key stakeholder groups and the highest governing body. Economic, environmental and social issues are regularly considered by the specialised Committees of the Board of Directors and the management bodies of subsidiaries and affiliates.
Relying on the preliminary work performed by the BoD committees, namely preliminary consideration of the most important matters reserved to the Board of Directors and development of recommendations for decision-making on these matters, the Board of Directors is able to quickly adapt to the changing circumstances and observe particularly important principles of corporate governance.
PROCESSES TO REMEDIATE NEGATIVE IMPACTS
As a public company, Kazatomprom strictly complies with listing rules and disclosure requirements. The Company's corporate governance system rests on the principles of efficiency, prompt response, and transparency, ensuring good governance and control in all areas: human rights protection, shareholder protection, HR policy, supplier relations, law and ethics, occupational health and safety, environmental protection, corporate conflicts and conflicts of interest, as well as issues and processes related to remediation of potential and/or emerging adverse impacts.
We fully recognise that any incident involving our business and/or a breach of the law could lead to negative consequences, such as financial losses, undermined the trust of investors and stakeholders, lower share prices, damage to the reputation, fines, etc.
Kazatomprom has built, and continues to develop, a system of engagement with all stakeholders, using a variety of communication methods and channels, which allows focussing on improvements in two-way communication systems.
To ensure effective cooperation in identifying and/ or addressing adverse impacts, the Company has established clear and accessible grievance mechanisms to allow all stakeholders to raise concerns about potential and/or actual adverse impacts and to seek response and remedy. All our employees and stakeholders can communicate their requests, questions, suggestions or complaints through the communication channels in place. Moreover, Kazatomprom's internal documents oblige all employees who become aware of any circumstances and/or actions related to the occurrence of negative impacts to report them to the Company's hotline, via internal corporate communication channels, social media accounts or website. Kazatomprom strictly prohibits any retaliatory measures against whistleblowers, guaranteeing confidentiality and anonymity.
The materiality of all issues raised is established against the criteria approved and appropriate to every topic raised. Depending on the actual/potential adverse impact and/or the complaint received, Kazatomprom will take appropriate corrective action.
In particular, we seek to identify all possible risks in advance and reduce our exposure to operational, environmental and financial damage to the lowest possible level to eliminate our negative impact. The Company follows this approach in all relevant business processes, including strategy, business planning, business operations and capital value creation processes, and has already effectively identified and remediated adverse impacts, as well as ensures effective control of risk mitigation. Kazatomprom takes adequate and timely measures to prevent and/or eliminate adverse impacts through rigorous processes to investigate hazardous conditions, potential accidents/ incidents and awareness of environmental conditions, as well as a responsible approach.
We assess the effectiveness of our communication channels through corporate culture audits, in particular through staff engagement and interaction within the Company, the promptness of crisis resolution, production efficiency and the achievement of our strategic development goals.
CREATING ECONOMIC VALUE
Kazatomprom openly and transparently informs shareholders, employees, partners and other stakeholders about its efforts taken to create economic value. This disclosure helps the Company's stakeholders see how the Group creates and distributes economic value over the reporting period.
Direct economic value generated and distributed, KZT billion

65 Incomes are calculated in line with the GRI Standards methodology and include the revenues and all incomes of the Company.
66 Operating expenses include the following expenditures: cost of sales (excluding salaries and taxes), selling expenses (excluding salaries and taxes), general and administrative expenses (excluding salaries and taxes).
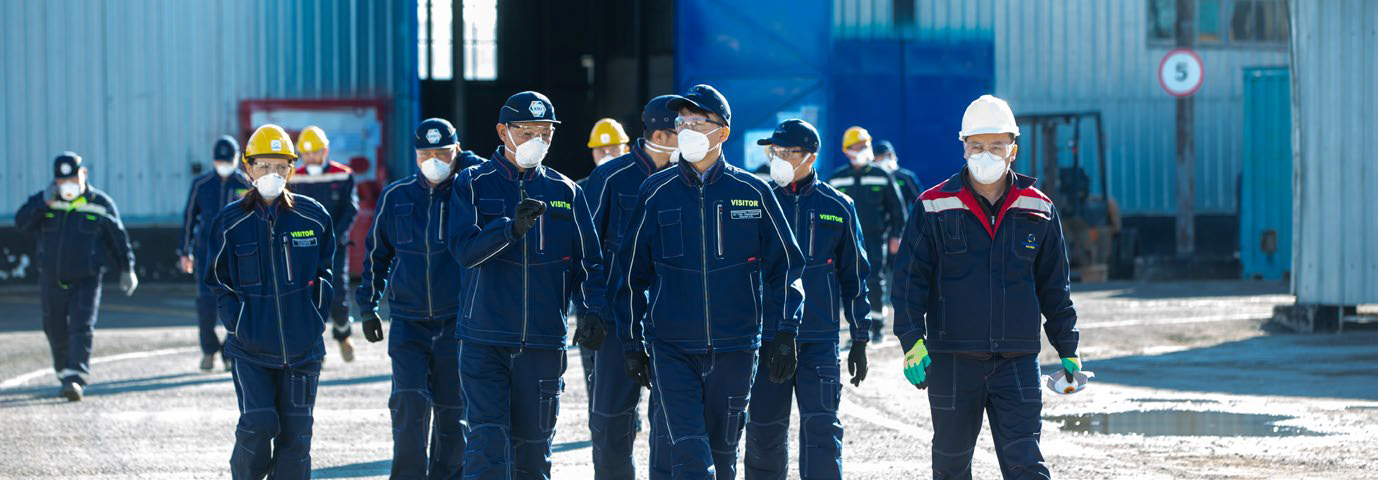
DETERMINING MATERIAL TOPICS
The Company’s Department for Strategic and Sustainable Development has embarked on preparing an Integrated Annual Report (IAR) of Kazatomprom for 2023 to comply with the disclosure and transparency rules of the listing agency of the United Kingdom DTR 4.1.3 (UKLA’s Disclosure and Transparency Rules), the requirements of the Kazakhstan Stock Exchange (KASE) and Astana International Stock Exchange (AIX) for the publication of annual reports as well as with Kazatomprom’s Information Disclosure Rules and the corporate governance standards recommended by the Company’s Corporate Governance Code. At the same time, the 2023 IAR will be prepared in line with the GRI, SASB, and TCFD non-financial reporting standards.
The Company’s Department for Strategic and Sustainable Development carried out a number of activities to determine the material topics for the Company and their disclosure in the 2023 IAR.
It conducted a stakeholder survey to determine material topics to be disclosed in the 2023 IAR. These topics demonstrate the Company’s significant impacts on the economy, environment, and people, including impacts on their human rights. Overall, the Company received responses from the following stakeholder groups:
- its subsidiaries and affiliates;
- partners;
- international organisations;
- business communities;
- suppliers of goods, works and services.
The list of topics for evaluation included the topics of the GRI Topic Standards and Kazatomprom’s indicators. The stakeholders were asked to rate each topic on the organisation’s impact on the economy, environment, and people, including impacts on their human rights, on a 5-point scale, with 1 being “very low” and 5 being “very high”. The preliminary list included topics that scored 4 and 5 points out of 5 possible.
Also, the Company’s Department for Strategic and Sustainable Development analysed the material topics for the leading companies in the nuclear and mining industries, as well as the material ESG-related issues for independent international rating agencies.
Thus, they developed a list of 16 material topics to be disclosed in the 2023 IAR. The Management Board approved the list.
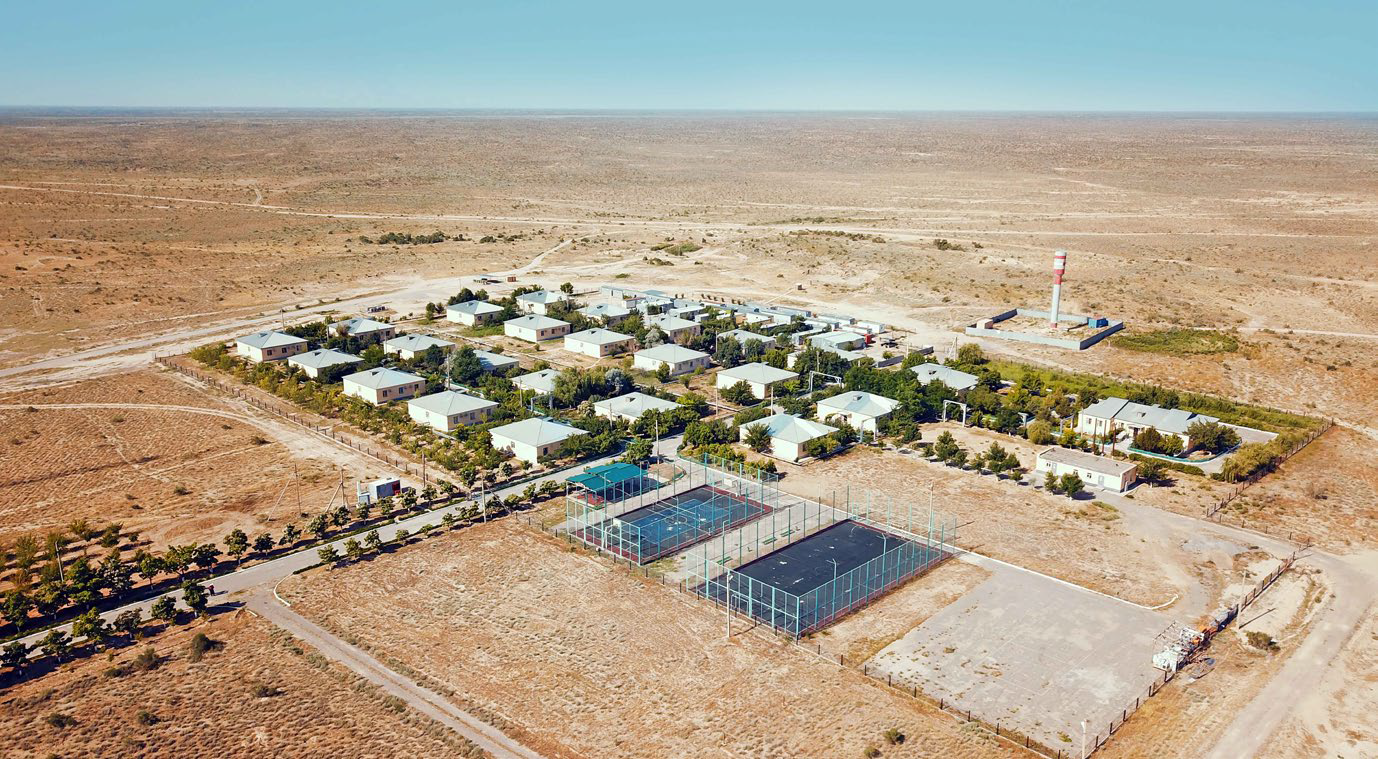
Changes in material topics
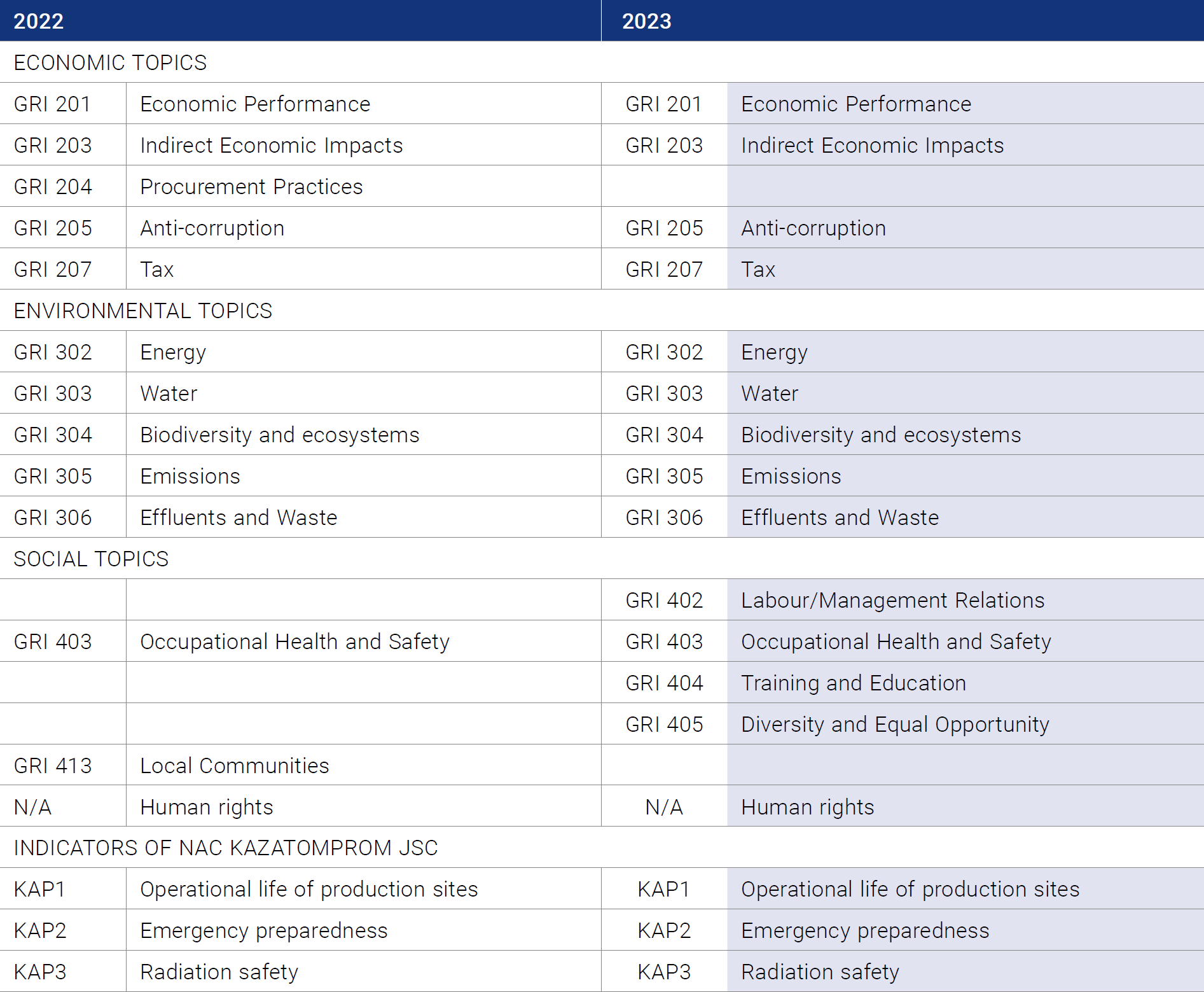
The list of material topics for 2023 was used to prepare the 2023 IAR for detailed disclosure of the economic, environmental and social impacts of the Company in line with the requirements of the GRI, SASB and TCFD standards.
As required by GRI 3-3, the Company conducted an additional analysis of potential positive and negative impacts of Kazatomprom on the economy, environment or people, including impacts on the human rights.
Climate Change and Energy Efficiency
OUR APPROACH
To reduce the impact of technologies on climate and move towards a low-carbon economy, Kazatomprom supports the efforts of countries that have adopted the Paris Agreement, striving to reduce greenhouse gas emissions. The Company implements measures to reduce its carbon footprint and develops plans to achieve carbon neutrality and climate resilience strategies. Kazatomprom views decarbonisation as one of multiple important tools to fight against climate change. As part of its Decarbonisation Strategy, which was developed in 2022, Kazatomprom implemented projects to reduce greenhouse gas emissions and protect water resources and biodiversity. Karatau LLP put into operation four solar collector systems to supply hot water to a hotel, household facilities, a hostel, and a sports complex, facilities of the Physico- Chemical Laboratory and the Household and Utility Complex. The conversion of hot water boilers from diesel fuel to liquefied gas in the boiler units of Karatau LLP's shift camp was completed.
In the Strategy for Decarbonisation and Carbon Neutrality, we have identified three main development scenarios:
- A pessimistic scenario of inertial business development without any steps towards decarbonisation.
- A realistic scenario with the gradual achievement of carbon neutrality, given the moderate pace of decarbonisation of the country's economy.
- An optimistic scenario seeking to achieve carbon neutrality quickly.
The realistic and optimistic scenarios prioritised by the Company include a list of measures, including increasing energy efficiency, applying offset mechanisms, increasing the use of renewable energy sources, modernising the car fleet or switching to electric transport, and reducing carbon intensity.
GREENHOUSE GAS EMISSIONS
The Company regularly monitors greenhouse gas emissions by quantifying direct and indirect emissions in accordance with international standards and guidelines such as the GHG protocol and ISO 14064.
The Group carries out consolidation of greenhouse gases on a 100% basis regardless of the Company's equity participation in joint ventures.
Direct greenhouse gas emissions, 2021-2023 (Scope 1), ‘000 tonnes of CO2-eq.
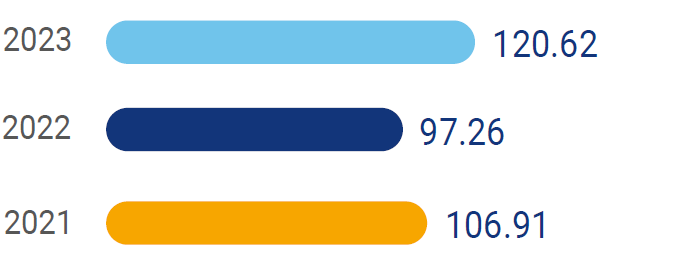
The 24% increase in greenhouse gas emissions of Scope 1 emissions by the Group compared to 2022 is attributed to the expansion of drilling and mine preparation activities, increased freight transportation, and the development of new mining areas.
The Company has no emissions from combustion or decomposition of biomass.
Indirect GHG emissions, 2021-2023 (Scope 2), tonnes of CO2-eq.
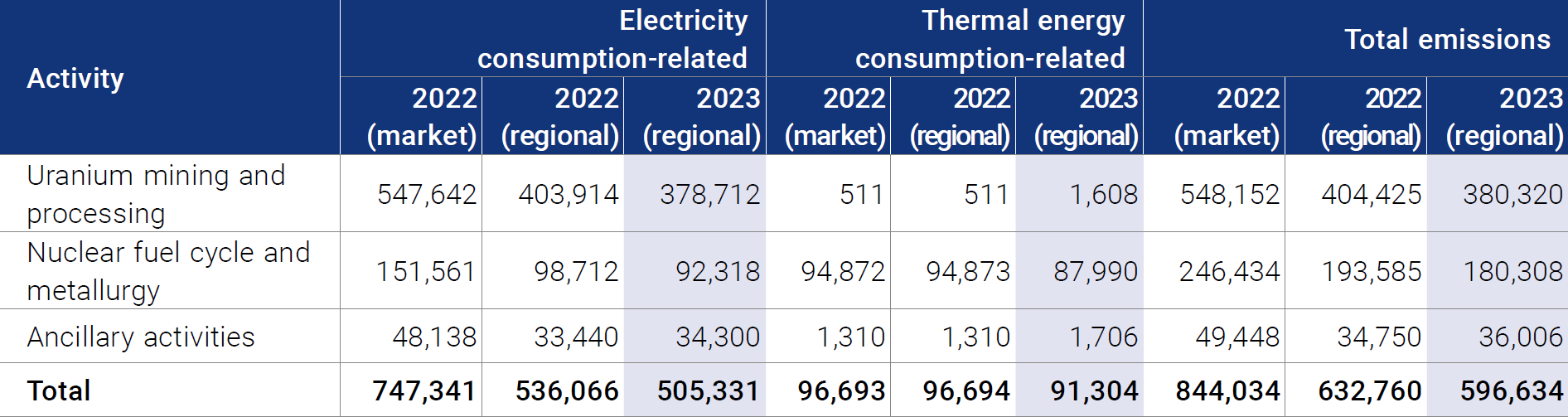
Compared to the benchmark in 2022, the decrease in indirect emissions (Scope 2) in 2023 by 5.70% (632,760 tonnes CO2-eq. in 2022) is associated with an increase in the purchase of additional green electricity. In late 2022, Kazatomprom's subsidiaries and affiliates purchased electricity through spot trading on the platform of Kazakhstan Operator of Electricity and Capacity Market JSC (KOREM JSC). In 2023, the total volume of electricity purchased from Moynak HPP JSC on the KOREM JSC platform amounted to 142 million kWh.
Also, due to the amendment of the Law of the Republic of Kazakhstan On Electricity, the method for calculating GHG emissions under Scope 2 has changed from market-based to regional according to the GHG protocol. In this regard, the above table reflects actual data for 2023, obtained by the regional method. The calculation of greenhouse gas emissions using the market method for 2023 is 793,299 tonnes of CO2-eq.
In accordance with the amended Law of the Republic of Kazakhstan On Electricity of 01 July 2023, the Financial Settlement Centre of Renewable Energy Sources LLP of the Ministry of Energy of the Republic of Kazakhstan is a single buyer of electricity in the Republic of Kazakhstan. In accordance with subparagraph 3, paragraph 5, Article 19-1 of the Law of the Republic of Kazakhstan On Electricity, subjects of the wholesale electricity market shall purchase electricity only from a single buyer of electricity. Contracts for the purchase of electricity from Moynak HPP JSC in the second half of 2023 had to be terminated accordingly. In the first half of 2023, the actual volume of green electricity purchased including direct contracts and spot trading totalled 49,615,000 kWh, which resulted in the reduction of the Company's Scope 2 indirect GHG emissions for 2023.
Annual greenhouse gas emissions at each subsidiary and affiliate do not exceed the threshold of 20,000 tonnes of CO2 equivalent as adopted at the national level for reporting emissions and participating in the Kazakhstan Emissions Trading System.
In the reporting period, Kazatomprom held several campaigns to help reduce the Company's climate change impact. In particular, we continued planting trees on the territory of the fields and in the adjacent settlements. We also held a Car-Free Day when employees and stakeholders ditched private cars for a day and used public transport, reducing CO2 emissions from road transport.
Kazatomprom employees actively participated in the Earth Hour campaign when they disconnected all devices from electricity for an hour. The aim was not only to save electricity and reduce greenhouse gas emissions associated with its consumption, but also to draw public attention to the climate change issues.
Other indirect greenhouse gas emissions (Scope 3), tonnes of CO2-eq.

The decrease in greenhouse gas emissions under Scope 3 for 2023 compared to 2022 is due to a decrease in purchased goods, in particular, sulphuric acid at JV Zarechnoye JSC, Baiken-U LLP, ME Ortalyk LLP, Kazatomprom-SaUran LLP, UMP JSC, ammonium nitrate at Karatau LLP, Kazatomprom-SaUran LLP, and ammonia water at UMP JSC.
Earlier, until 2021, the Company did not calculate greenhouse gases for Scopes 2 and 3, as the applicable Kazakhstan Law provides only for calculations for Scope 1 based on assessments of independent and licensed companies. In this regard, the Company did not recalculate greenhouse gas emissions.
In 2023, the intensity of greenhouse gas emissions was 34.5 tonnes per tonne of produced uranium. The metric selected by the Company (denominator) for calculating the coefficient was the volume of uranium production by Kazatomprom (20,996 tonnes) in 2023. Direct emissions (Scope 1) and indirect energy-related greenhouse gas emissions (Scope 2) were considered in the intensity ratio.
Intensity of greenhouse gas emissions
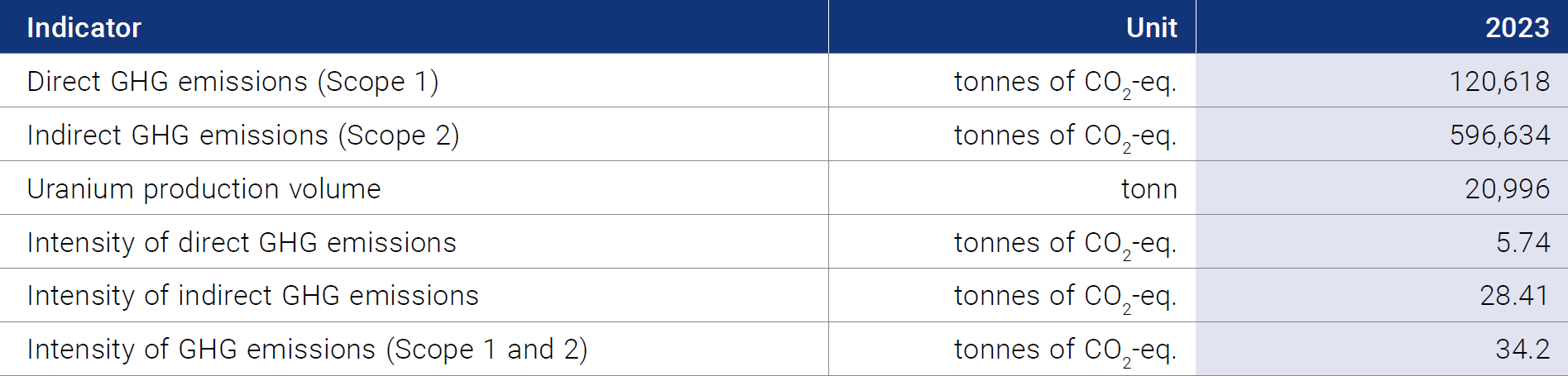
ENERGY EFFICIENCY AND ENERGY SAVING
Kazatomprom aims to minimise its impact on the environment and emphasises reducing its carbon footprint. The Company implements measures to reduce and optimise energy use. All subsidiaries and affiliates of the Group have an energy management system that manages energy efficiency issues and complies with the requirements of ISO 50001:18001.
The Company is also in a phased transition to an upgraded energy management system that complies with ISO 50001:2019, which helps on an ongoing basis reduce energy consumption, minimise emissions of harmful substances and receive financial benefits.
Kazatomprom improves energy efficiency and reduces the energy intensity of production by introducing energy-efficient equipment, rational using natural resources and modernising production processes. In the field of energy consumption and energy efficiency improvement, the Company established a KPI that does not allow exceeding the annual planned specific electricity consumption rates for uranium production.
An energy audit is conducted at the Group's enterprises once every five years to assess the possibility and potential for energy saving. Its results form the basis when developing an Action Plan for energy saving and energy efficiency improvement. The plan is formed annually as part of the Implementation Plan of the Kazatomprom Development Strategy until 2028.
In 2023, the Company implemented a range of measures to improve energy efficiency. The actual economic effect was KZT 1,292 million, or up by 4% of the target. Our energy saving and energy efficiency measures helped save 218 GJ in 2023.
As part of decarbonisation and carbon neutrality projects, Karatau LLP completed conversion of hot water boilers from diesel fuel to liquefied gas in the boiler units of a shift camp. Works are completed, flow meters are installed. Savings in 2023 amount to KZT 43,715.
Energy consumption, ‘000 GJ67
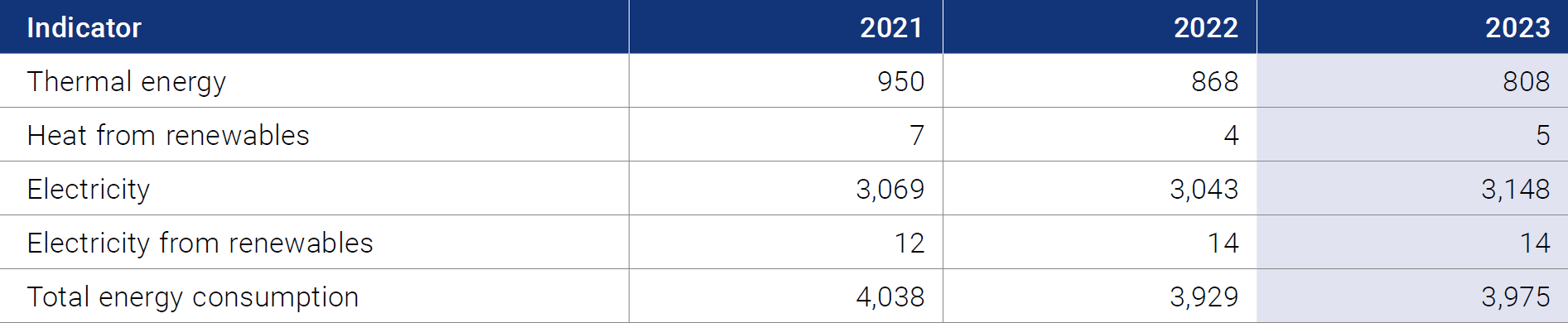
67 The 2021-2023 figures have been adjusted. Indicators for heat and electricity consumption from RES have been added to the table.
Sokol-M(O)-5 Water Desalination Plant launched at UMP JSC reduced thermal energy consumption in steam in 2023 as compared to 2022. This allowed obtaining distilled water without using thermal energy in steam for further use in the technological process. Total consumption of fuel and energy resources for production, extraction and processing of raw materials reached 5,556,000 GJ.
Earlier, the Company produced distilled water from saturated steam by cooling tubular heat exchangers (distillers) with recycled water.
Use of primary energy sources, ‘000 GJ

The increase in coal consumption is linked to the inclusion of the ore enrichment plant for fluorspar concentrate production in the city of Kurchatov within UMP JSC. Coal is utilized there for generating heat and steam for production purposes and heating facilities.
Excess gas consumption in 2023 compared to 2022 is due to the gradual replacement of diesel with natural gas.
The annual electricity output generated by the Group's solar photovoltaic plants is 3,020 MWh. The generated electricity is used for own needs, allowing annual savings of KZT 72 million. Excess electricity is supplied to local power grids for use by households and businesses in the regions where the Group operates.
Energy intensity
In 2023, the consumption of fuel and energy resources (FER) at the Group's enterprises increased by 2.7% compared to 2022. This is due to the commissioning of blocks No.6 and No.7 of the Budenovskoye deposit and low uranium content in pregnant solutions, which required the commissioning of additional capacities. In 2023, the specific energy intensity was 265 GJ/t and includes energy consumption from all fuel and energy resources.
Energy intensity68

68 The 2020-2021 figures have been adjusted. Heat consumption for production, extraction and processing of raw materials has been added to the data on fuel and energy consumption.
Alternative energy
Kazatomprom aims to improve its energy efficiency and reduce its carbon footprint by moving from traditional energy sources to more sustainable and environmentally friendly methods. This approach helps reduce greenhouse gas emissions and save fuel and energy resources:
- photovoltaic stations (PV);
- solar collectors (or solar water heaters).
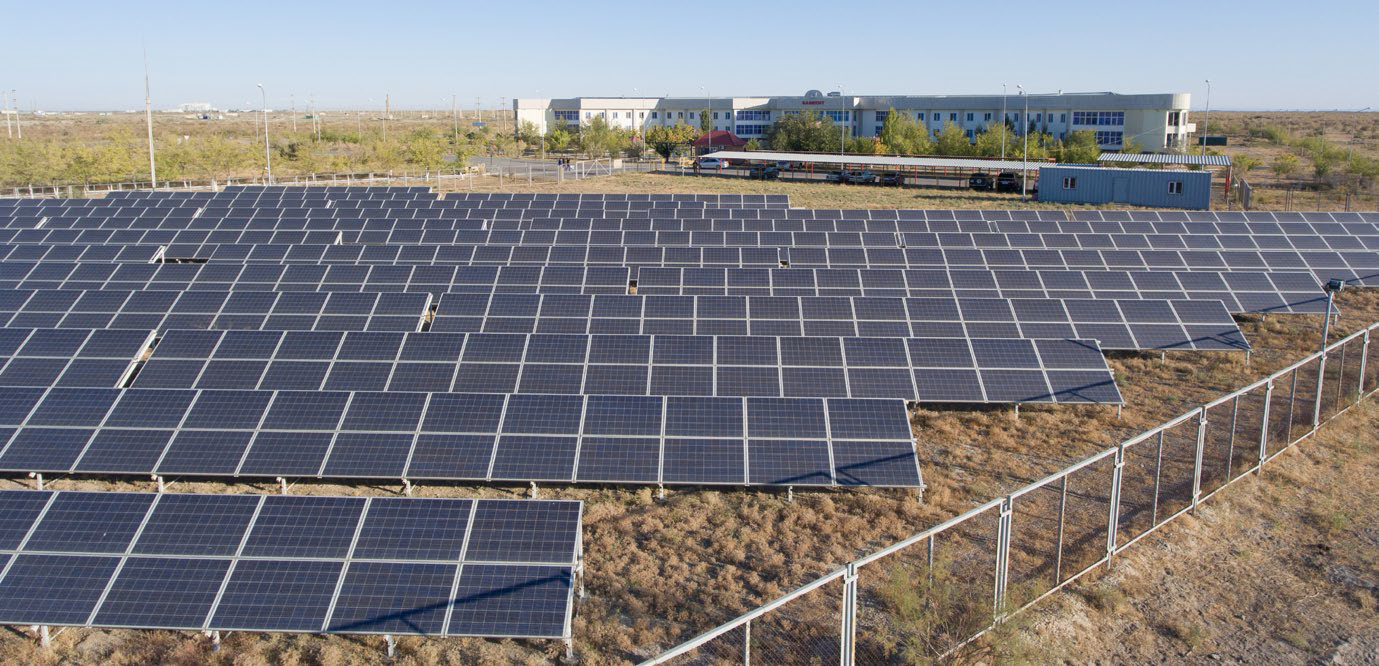
Electricity generation by PV stations, ‘000 MWh
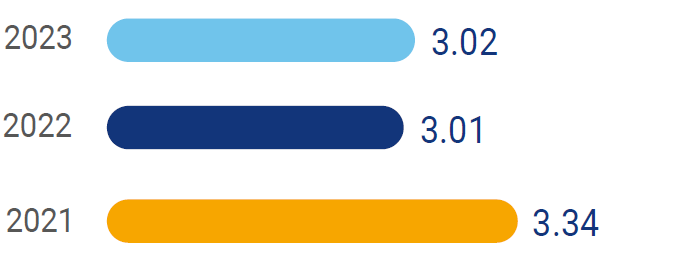
Effect from the use of alternative energy sources in 2023, ‘000 KZT

The Company is constantly looking for new ways to use alternative energy sources at its enterprises. In 2022- 2023, Karatau LLP developed design documentation and received a positive opinion from a non-departmental expert review for the installation of four solar collector systems. The Company will use these systems to supply hot water to a hotel, household facilities, a hostel, and a sports complex. The facility was put into operation in Q1 2023.
Recycling
KZT 6.85 billion was the actual economic effect from the Company’s recycling project in 2023.
Plans for 2024 and a medium term
In 2024, we plan actions to reduce the carbon footprint of products in line with the developed Strategy for Decarbonisation and Carbon Neutrality of NAC Kazatomprom JSC until 2060. To achieve this goal, we will focus our efforts on the development of renewable energy sources and the reduction of greenhouse gas emissions across Kazatomprom. Work will continue on energy saving and energy efficiency of our operations. Focus areas include:
- Installation of solar collectors.
- Rational distribution and use of electricity, lighting, heating, hot water supply, and ventilation systems.
- Upgrade of electrical equipment, replacement with energy-efficient equipment.
- Efforts to ensure the proper technical condition and rational operation of power equipment and power plants.
In 2024, JV SMCC LLP plans to develop design documentation for the technical re-equipment of existing boiler houses and their conversion to liquefied imported gas. The first stage includes Central Boiler House and Mini Boiler House No.1 of a shift camp. Construction and installation works are scheduled for 2025. The second stage includes Mini Boiler House No.2 of a new shift camp and Mini Boiler House of VIP-settlement. Construction and installation works are scheduled for 2026.
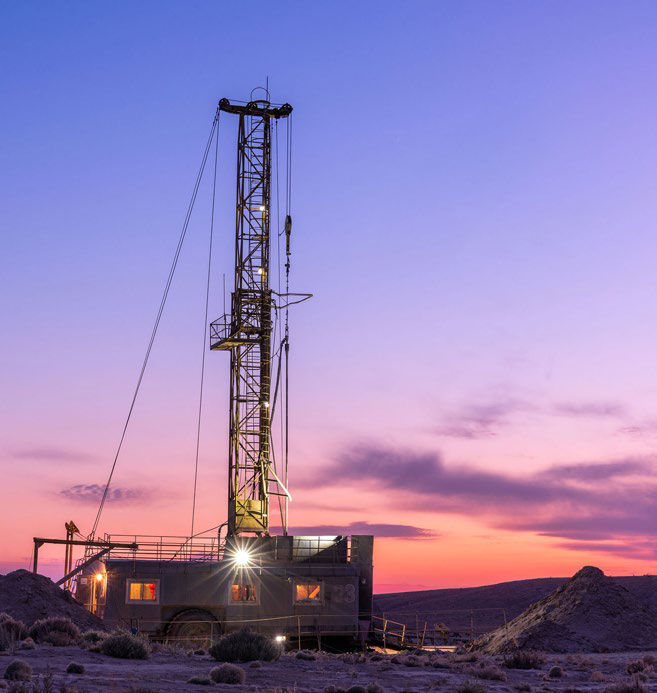
Environmental Sustainability
OUR APPROACH
Kazatomprom recognises the negative impact of natural uranium extraction on the environment and aims to minimise it. The Company conducts regular environmental monitoring, ensures rational use of natural resources and implements innovative technologies.
The Company implements its environmental policy through the environmental and energy management system implemented at all Group’s production facilities and complies with ISO 14001 and ISO 50001 standards. Strict controls help prevent pollution of water, soil and air, as well as conserve biodiversity and reduce noise levels. This system allows the Company to set goals, measure results and comply with regulatory requirements.
The main principles and approaches to environmental protection management are set out in the Policy of NAC Kazatomprom JSC in the field of health and safety, environmental protection, and radiation and nuclear safety.
The Company's Production Safety (HSE) Committee operates under the Board of Directors and coordinates the relevant activities. The Corporate HSE Department of the parent company provides overall guidance on environmental protection activities, analyses the effectiveness of environmental safety and emergency response activities, and prepares reports for the Company's management. Within the structure of the subsidiaries and affiliates, specialized divisions have been created whose task is to ensure the implementation of environmental policy, compliance with legal requirements and corporate standards in the field of environmental protection.
We apply the precautionary principle, especially in the areas of health, safety and environmental impact. The implementation of this principle is carried out in the process of risk management within the framework of the Group's integrated HSE management system.
Kazatomprom aims to reduce environmental impacts throughout the life cycle of a deposit: from environmental impact assessment (EIA) during design to closure and remediation upon completion of deposit utilisation.
The Company emphasises environmental education and open exchange of information with stakeholders, including public hearings and written appeals.
Kazatomprom requires that its suppliers of goods, works and services, as well as contractors, comply with the corporate standard The System of HSE Standards. These requirements are advisory in nature for counterparties.
In 2023, within the framework of the implementation of the ESAP Roadmap:
- we conducted studies of the environmental impact of mine production facilities on the environment and local communities;
- we conducted integrated environmental and social studies for sustainable development according to GRI standards;
- we conducted studies on optimisation of production and consumption waste management processes at enterprises in accordance with the Environmental Code of the Republic of Kazakhstan and GRI standards (Zero Waste);
- we updated the plans for elimination of subsoil use consequences of uranium mining;
- we developed an integrated technology to reduce the volume of solid low-level radioactive waste (SLRW) generated by eliminating the consequences of subsoil use at in-situ uranium leaching mines at Kazatomprom-SaUran LLP.
Environmental protection milestones for 2023
The Group implements the following environmental projects:
- implementation of the Programme of Bird Protection;
- projects for atmospheric air protection;
- Corporate Zero Waste Culture Development Programme;
- Integrated Environmental and Social Research Programme, ESRP;
- low-carbon and decarbonisation strategy.
Also, in 2023:
- we developed Water Resources Management Strategy and Standard;
- Kazatomprom confirmed the independent ESG rating from the leading international rating agency S&P Global;
- Kazatomprom received its first CDP (Carbon Disclosure Project) rating, with a "B" rating for climate change;
- Kazatomprom regularly participates in working group meetings on changes to environmental legislation;
- the Company's employees took part in the IAEA environmental conference with reports in Vienna;
- almost all subsidiaries and affiliates held international environmental events, environmental lessons in schools, clean-up days, territory cleanup with further rubbish removal and other events with wide media coverage;
- As part of World Environment Day, an online event was held, organized by the Corporate Safety Department of the Company, on the topic: "The World is More Beautiful When It's Clean!"
- JV Katko LLP was awarded a bronze place of the Paryz Prize by the President of the Republic of Kazakhstan for its contribution to the environment.
MONITORING AND CONTROL
The primary objective of the Group’s environmental monitoring is to control the negative impact of production on the environment and health of local communities. In accordance with the environmental laws of the Republic of Kazakhstan, the Group’s subsidiaries and affiliates carried out industrial environmental control (IEC) on a quarterly basis in the reporting period, engaging accredited contracting organisations (laboratories) following the Schedule.
In 2023, in accordance with the new norms of the Environmental Code of the Republic of Kazakhstan69 and the Corporate Zero Waste Culture Development Programme, the Company updated Kazatomprom's corporate standard ST NAC 17.2 "Environmental Protection Standards. Rules of production and consumption waste management at NAC Kazatomprom JSC enterprises70". The Company developed the Regulation on Waste Management of the UMP JSC Tailings Storage Facility No.1204 of 30 September 2023.
69 Environmental Code of the Republic of Kazakhstan No.400-VI ZRK of 02 January 2021.
70 Company’s Administrative Order No.6 of 10 January 2024.
SKZ-U LLP completed construction and assembly works on installation of an automated monitoring system at pollution emitters. UMP JSC ran a pilot (test) output.
As required by the environmental laws of the Republic of Kazakhstan, an Environmental Impact Assessment (EIA) and public hearings are to be held prior to the commencement of any planned activity. At the hearings, representatives of enterprises, acting as customers, present their projects and explain to stakeholders the environmental and social aspects of the planned project. Results of EIA are fully disclosed for review and comments to all stakeholders, and any resident of an area where the Company operates can share their opinion on the issues regarding the impact of the planned activity on the environment and health of the local population.
All projects for the construction and reconstruction of production facilities implemented in the Company's subsidiaries and affiliates have passed public hearings and the EIA stage and received a positive state environmental expert opinion.
INVESTMENT IN ENVIRONMENTAL PROTECTION
The environmental and energy management system implemented at all Group’s production facilities complies with ISO 14001 and ISO 50001 standards.
In 2023, as part of its commitment to improve its approaches to occupational safety management, Kazatomprom's headquarters successfully passed a recertification audit and confirmed its certificate from the TÜV International Certification. The independent audit certified that, when organising licensed export and import deliveries of specific products, the Company's integrated management system complies with the requirements of international standards ISO 14001:2015 Environmental Management System and ISO 45001:2018 Health and Occupational Safety Management System.
In 2023, Kazatomprom’s total cost of environmental protection measures amounted to KZT 1,306.5 million. In 2023, the Company paid KZT 267.0 million in emission taxes.
Investment in environmental measures, 2023, KZT million

COMPLIANCE WITH ENVIRONMENTAL LEGISLATION
The Company utilises robust environmental monitoring and radiation safety systems (ISO 14001 compliant) at its uranium mines and production sites. There were no environmental accidents in 2023. Violations of environmental legislation were detected. The Holding Company paid fines in the amount of KZT 22.213 million (UMP JSC, Semizbay-U LLP, RU-6 LLP, JV Katko LLP, Baiken-U LLP, JV Khorasan-U). The authorised state body for violation of environmental norms and requirements imposed administrative fines for soil pollution due to spillage of process solutions and minor littering of the territory. There were no exceedances of the established total limits set by the state authorities for waste generation, emissions and discharges. The Company identified and eliminated root causes of all violations and took prompt actions to prevent any future accidents.
ENVIRONMENTAL PROTECTION TRAINING
To obtain the necessary competencies and knowledge in studying and applying the Good International Industry Practice (GIIP) and ensuring the effectiveness of environmental management, the Company organises regular training sessions for the heads of subsidiaries and affiliates and specialists responsible for subsoil protection, environmental and social issues. In accordance with the Action Plan of the ESAP Roadmap within the reporting period, Kazakhstan Nuclear University LLP jointly with the IHT LLP branch held training seminars in the area of environmental safety and emergency response:
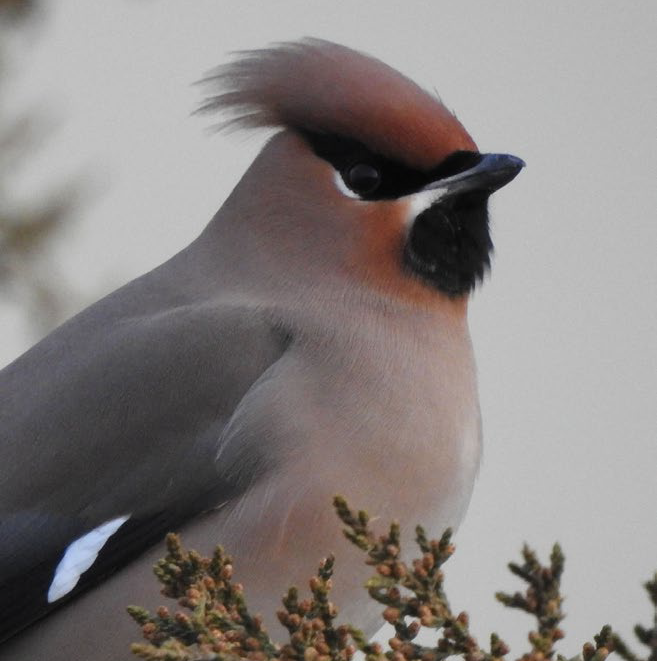
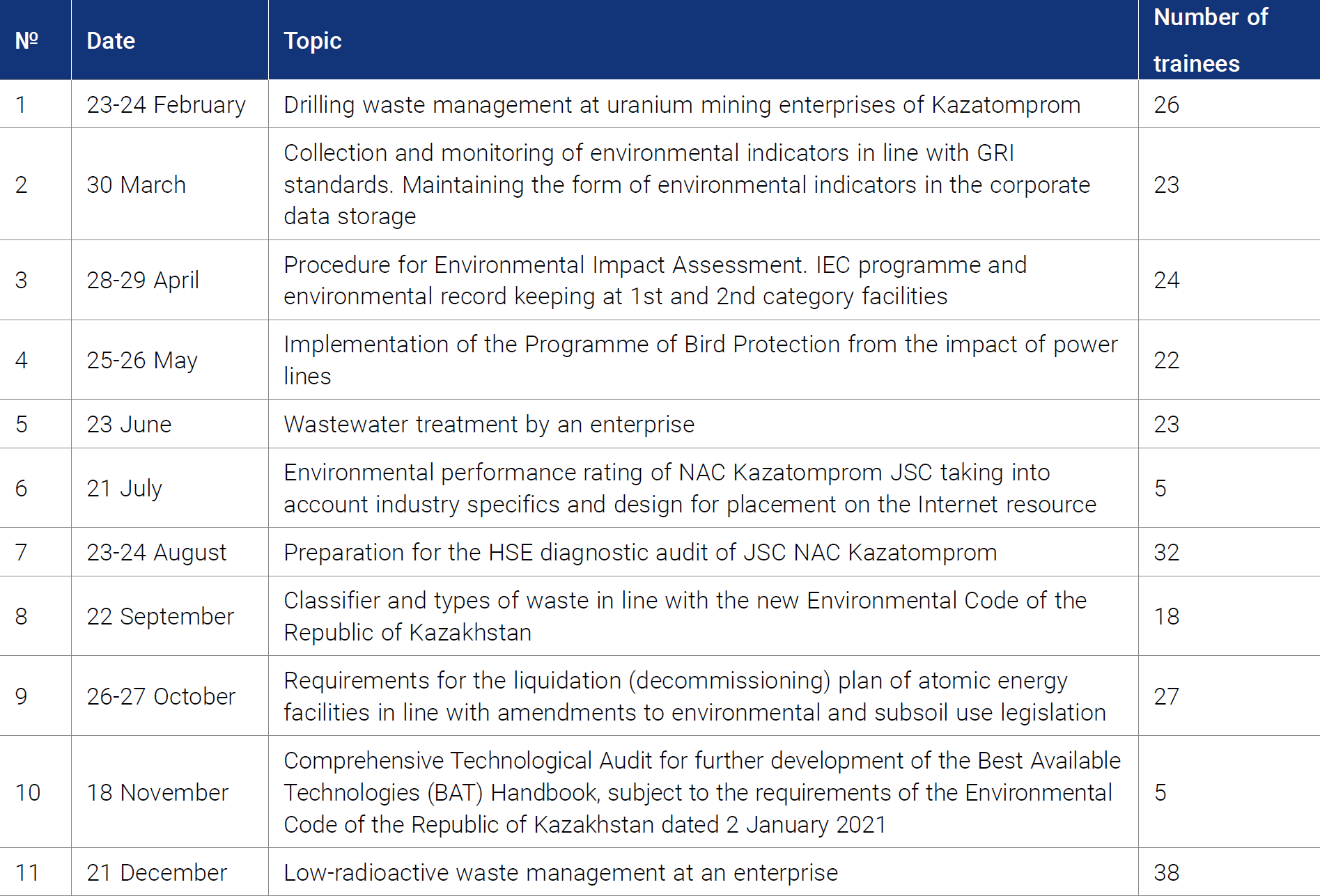
243 trainees from 20 subsidiaries and affiliates and the headquarters took part in the training.
The Company held 33 training seminars/webinars that brought together 968 trainees from the headquarters, subsidiaries, and affiliates of Kazatomprom over the entire period of implementation of the ESAP Plan (2018-2023).
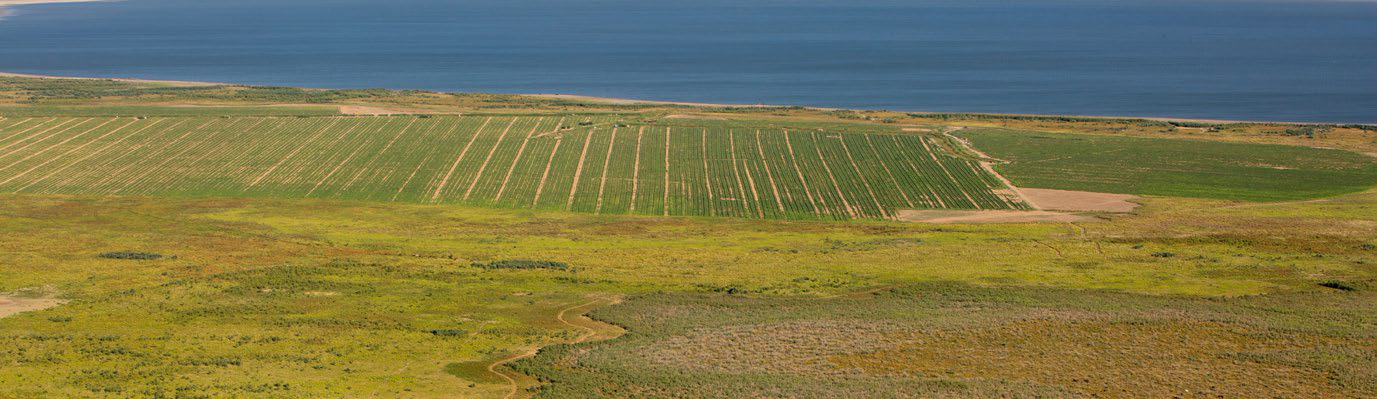
EMISSIONS
The specifics of the Group's production activities result in emissions into the atmosphere, due to which minimisation of pollutant emissions is an important aspect of Kazatomprom's environmental activities.
We seek to reduce the negative impact by introducing technological improvements in our own production facilities. At the same time, the Company sells its products to countries that use nuclear energy. By doing this, the Company contributes to low carbon industry development in these countries and helps reduce emissions.
Breakdown and source of air emissions, '000 tonnes
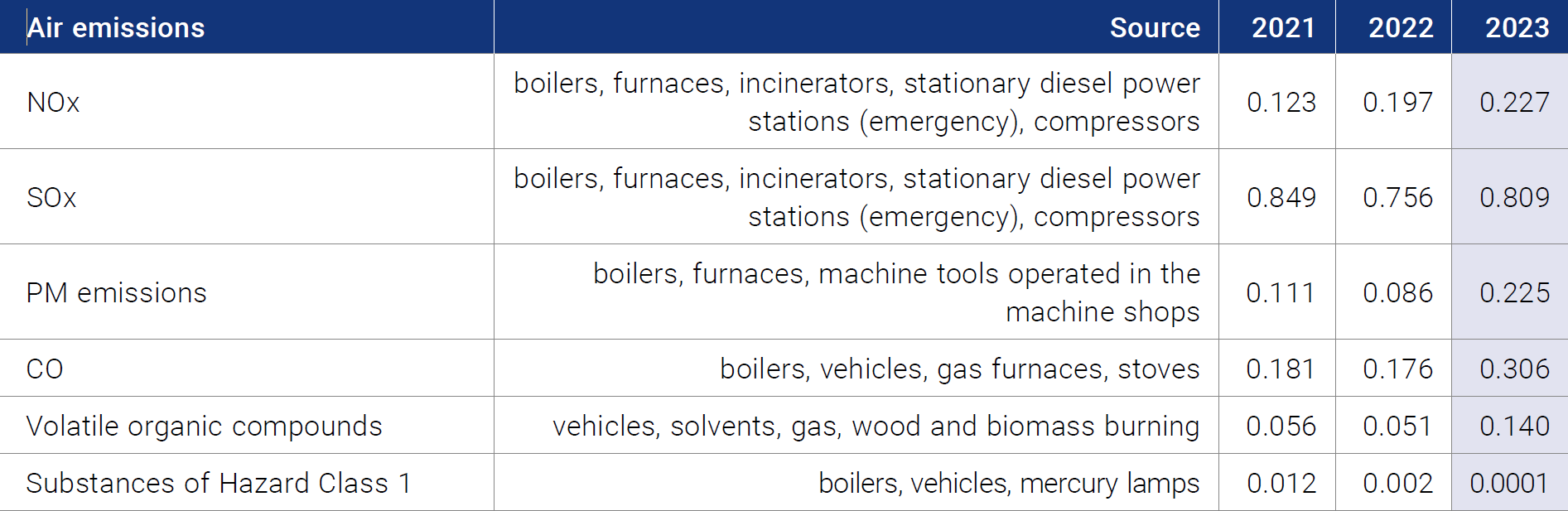
The increase in specific emissions and Scope 1 GHG emissions is due to increased drilling operations, increased freight traffic, and the exploration of new sites.
No emissions of mercury. In the Group, there are emissions of lead and its compounds only at Ulba Metallurgical Plant JSC, JV Katko LLP, Karatau LLP, RU-6 LLP and Semizbay-U LLP – 0.00055 tonnes.
The Group implements a number of measures aimed at reducing air emissions and monitoring the air quality:
- air quality monitoring;
- using modern gas treatment systems, energyefficient technologies and photovoltaic stations, which reduce emissions;
- using dust and gas catching collectors for dust cleaning and purification of process gases, coming from VGTP calcination furnaces. A hydrofilter and a pulsed ceramic filter (PCF-45) successfully operate in the refining shops of Baiken-U LLP and reconstructed Kazatomprom-SaUran LLP, eliminating the emission of radiation dust and minimising emissions to the environment by 20%.
The Company does not produce, export, or import ozone-depleting substances.
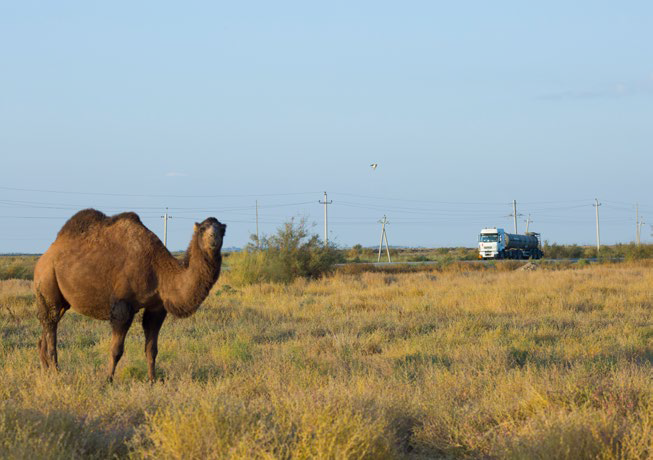
WATER RESOURCES
Water is an essential component of the technological process both at the main production facilities of Kazatomprom and in the operation of osmosis units (demineralised water is a raw material for generating electricity supplied to the external network for the needs of local communities). Besides, in some regions of operation, the Company provides water supply to the local population and industry.
We support the UN Agenda for Sustainable Development 2030, including SDG 6, Ensure the availability and sustainable management of water and sanitation for all, and also operate in accordance with the Water Code of the Republic Kazakhstan (Article 66) and water resources protection permit documents. The Company divides the water supply of enterprises into industrial and potable.
In 2023, the Company developed Water Resources Management Strategy and Standard to ensure efficient and sustainable use of water resources. The Company set the goals and objectives of the Water Resources Management Strategy in accordance with the public policy and approaches to effective water resources management, its strategic plans, and the specifics of the production and technological processes of Kazatomprom's enterprises, taking into account the location of the enterprises with regard to water resources availability.
UMP JSC develops design documentation for the installation of recycled water supply systems. This initiative will reduce the consumption of cold water from municipal sources used for cooling furnaces and rolling mills. Instead, recycled water cooled by chillers and dry coolers will be used. This will reduce wastewater volumes.
The Company's water intake does not have a significant impact on water sources. The Group does not withdraw water from sources that are recognised as vulnerable, protected by the state and of particular value to local communities or biodiversity. In an effort to reduce water consumption, we are making maximum efforts to reduce water abstraction and increase recycling. We also regularly monitor and assess the risks of water supply in all regions of our presence.
Kazatomprom emphasises cooperation with local communities in water resources management. Ensuring access to clean and safe drinking water is a fundamental human right. The Company provides feedback channels through which people can express their questions and concerns about the impact of the Group's enterprises on local water bodies. People are confident that the relevant environmental services will receive and address their concerns. Kazatomprom also cooperates with local authorities and public organisations to ensure a sustainable water supply in a long term.
WATER CONSUMPTION AND WATER WITHDRAWAL
The Company carries out water intake, including for drinking water supply, in accordance with the requirements and norms of technological regulations for ISR method. The withdrawal does not have a significant impact on water sources. Enterprises providing water supply (centralised and noncentralised) keep monitoring water withdrawal, and conduct regular monitoring of the state of water withdrawal facilities, internal water supply systems, and water metering units. The Water Code of the Republic of Kazakhstan, technical regulations, and rules for the selection, installation and operation of water meters in water supply and sanitation systems establish the requirements for water meters.
Groundwater is taken from the water withdrawal sites against a permit for special use of water issued by the Basin Inspectorates for Regulation of the Use and Protection of Water Resources under the Committee for Water Resources of the Ministry of Ecology, Geology and Natural Resources of the Republic of Kazakhstan. On 11 September, 2023, a standalone Ministry of Water Resources and Irrigation of the Republic of Kazakhstan was established.
In 2023, total water withdrawn dropped by 1.2% year on year, from 9,188,900 m3 to 9,081,400 m3.
Total water withdrawal, '000 m3
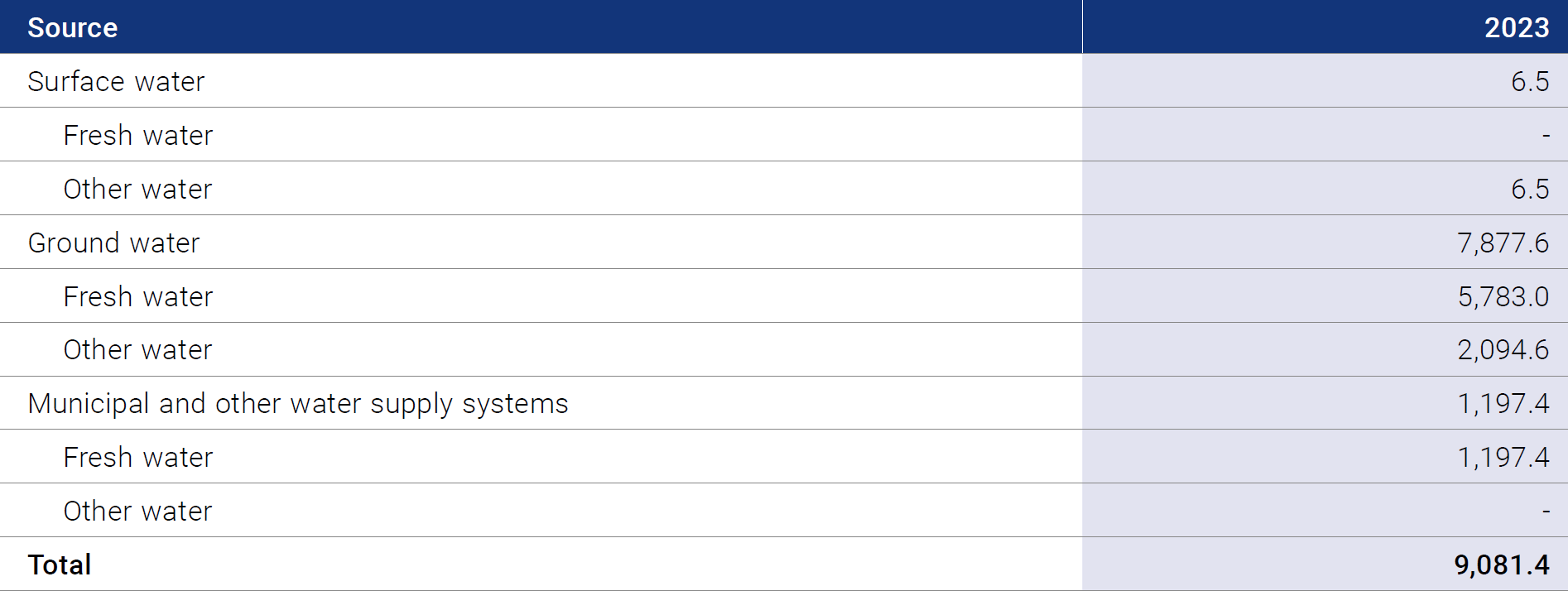
Groundwater accounts for 87% of the total amount of water withdrawn. 0.07% of water is withdrawn from surface sources. Ground water withdrawal dropped by 8%, from 8,573,500 m3 to 7,877,600 m3 due to an increase in the share of recycled water.
According to the Aqueduct Water Risk Atlas of the Institute of Water Resources, only the production sites of JV Zarechnoye JSC are located in a waterscarce region. The volume of fresh water intake from groundwater at the enterprise amounted to 141.8 thousand m3.
The total water consumption volume amounted to 5,193.5 thousand m3, with 68.9 thousand m3 attributed to JV Zarechnoye LLC.
WASTEWATER DISCHARGES
The Group's entities produce industrial, storm and domestic wastewater as a result of operations. After treatment through storm sewer outlet, water is discharged to surface water bodies from storm waste water from the territory of the industrial site and water not used in the technological process. Mine wastewater is discharged into storage ponds. The national laws prohibit the discharge of untreated wastewater into water bodies or on the terrain up to the permissible discharge standards. Since 2017, the General Requirements for Environmental Safety in Kazatomprom's Subsidiaries and Affiliates standard has been in force at Kazatomprom.
The monitoring programme includes studies of wastewater quality at all industrial sites connected to the centralised sewerage.
The main objectives of industrial monitoring of pollutant discharge sources at enterprises in accordance with the state standard ST RK 1545 are:
- assessment of the qualitative and quantitative composition of discharged wastewater directly at the point of discharge into storage tanks, filtration fields and natural depressions in the terrain;
- сompliance with the maximum permissible discharge limits at individual links of the technological scheme of wastewater treatment, improving the efficiency of existing treatment facilities.
In accordance with the approved List of pollutants (Order of the Minister of Ecology, Geology and Natural Resources of the Republic of Kazakhstan No.212 dated 25 June 2021), emissions of pollutants at production facilities are subject to environmental regulation.
Substances that pollute water:
- organic compounds of halogens and substances that can form these compounds in the aquatic environment;
- organic compounds of phosphorus;
- organic compounds of tin;
- metals and their compounds;
- hydrocarbons and their compounds;
- cyanides;
- arsenic and its compounds;
- pesticides, for which maximum permissible concentrations and approximate permissible levels of substances in water have been established;
- suspended substances and suspensions;
- substances that contribute to eutrophication (nitrates and phosphates);
- substances that have an unfavourable impact on the oxygen balance;
- other pollutants and their compounds, for which maximum permissible concentrations and approximate permissible levels of substances in water in water bodies of cultural and domestic, household, drinking and fishery water use are established.
In addition, according to the Rules for Maintaining the Pollutant Release and Transfer Register approved by the Order of the Minister of Ecology, Geology and Natural Resources of the Republic of Kazakhstan No.346 dated 31 August 2021, the Company monitors pollutants in wastewater information on which is subject to submission to the Pollutant Release and Transfer Register. This registry includes chemical compounds, polymers, biological sequences of nucleotides or amino acids, mixtures and alloys listed in the Chemical Abstracts Service, a division of the American Chemical Society.
All discharges are treated and meet regulatory requirements of the quality of discharged water according to the Methodology for Emission Rates adopted by the Ministry of Ecology, Geology and Natural Resources of the Republic of Kazakhstan. Monitoring of the condition of water bodies, including the determination of the chemical composition of surface, underground and waste water, is carried out regularly by the Company's accredited laboratories.
Total wastewater discharge by categories, ’000 m3

Total wastewater discharge by categories, ’000 m3

The wastewater discharges increased by 14% from 3,415,600 m3 in 2022 to 3,887,900 m3 in 2023. This is explained by the fact that in 2022, the Company indicated only the volume of wastewater discharges to stormwater sewage for UMP JSC. In 2023, the total volume of wastewater discharges also included discharges into the municipal sewer and the tailings management facility.
According to the Aqueduct Water Risk Atlas by the Water Resources Institute, the water-stressed region only encompasses the production facilities of Zarechnoye Joint Venture LLC. The volume of freshwater discharge at the enterprise amounted to 72.9 thousand m3.
GROUND WATER
Uranium mining based on the ISR method poses a risk of groundwater contamination. To minimise environmental risk at all Kazatomprom mines in accordance with sanitary standards, the deposits are surrounded by a sanitary protection zone with a radius of 500 m from ore deposits. Moreover, the Group’s enterprises constantly monitor the state of groundwater as part of the production environmental control in accordance with the established legal requirements and the requirements of the corporate standard “Methodological Guidelines for the Monitoring of the Impact on Ground and Underground Water in ISR Mining of Uranium”.
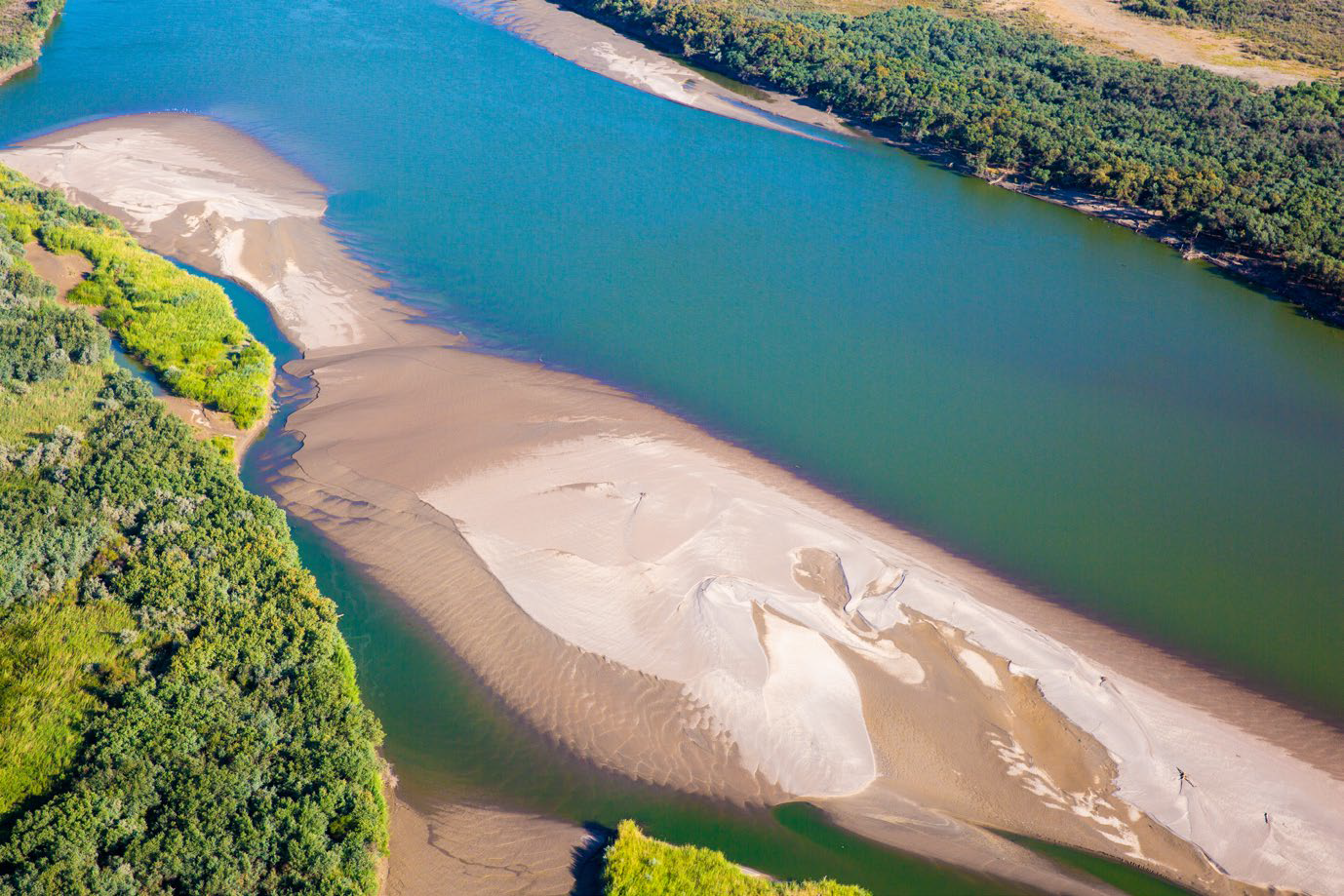
WASTE MANAGEMENT
Kazatomprom’s production operations generate industrial and municipal waste. Safe waste management, recycling and disposal is one of Kazatomprom's priorities. If it is impossible to process waste, we ensure detoxication and environmentally safe disposal of waste or transfer waste to specialised organisations.
Key waste generated by the Company:
- Solid and liquid radioactive waste.
- Overburden rocks generated during the mining of fluorite copper-molybdenum ores.
- Drilling mud from wells construction at the ISR mining sites.
- Fluoric gypsum from the production of hydrofluoric acid.
- Ash and slag waste from the production of thermal energy.
- Household waste.
- Waste oil products.
- Car tyres.
- Spent batteries.
When handling waste, the Group is guided by the internal standards and national legislation, which obliges the enterprises to ensure separate collection of all generated waste, depending on their type and composition, for subsequent disposal, processing and disposal. The Company carries out mandatory control over the prevention of waste generation, and also performs a number of activities in accordance with approved waste management programmes and plans.
Waste reduction efforts:
- Reuse of polyethylene pipes for piping.
- Recycling.
- Reuse of used car tyres and oils.
- Waste generation monitoring by sampling and analysis to identify the best measures to reduce and neutralise waste.
- Separate collection of municipal solid waste: plastic, paper and glass in the offices and production site camps. The sorted municipal solid waste is delivered to the nearest paper and plastic collection points (specialised organisations) at no charge for further recycling.
- All wastes generated is temporarily stored only at designated and equipped sites: temporary production waste storage sites, temporary municipal solid waste storage sites, drill cuttings storage sites, and temporary solid low radioactive waste storage sites.
To manage waste, we also work with organisations specialising in waste collection, recovery or disposal operations.
In particular, Kazatomprom makes contracts for the following services:
- Acceptance and disposal of low-level radioactive waste.
- Acceptance and disposal of municipal solid waste.
- Industrial waste recycling.
- Removal and disposal of radioactively contaminated metal and low density polyethylene materials.
Despite an increase in drilling activities in some subsidiaries and affiliates, the overall Company's efforts have resulted in the reduction of waste volumes by means of waste prevention, reduction, recycling and reuse. In 2023, in accordance with the new norms of the Environmental Code of the Republic of Kazakhstan and the Corporate Zero Waste Culture Development Programme, the Company updated Kazatomprom's corporate standard ST NAC 17.2 "Environmental Protection Standards. Rules of production and consumption waste management at NAC Kazatomprom JSC enterprises". As a result of Group's activities in 2023, total waste volume was 401,000 tonnes, dropped by 12% compared to 2022.
Total weight of waste and tailings by type, ‘000 tonnes
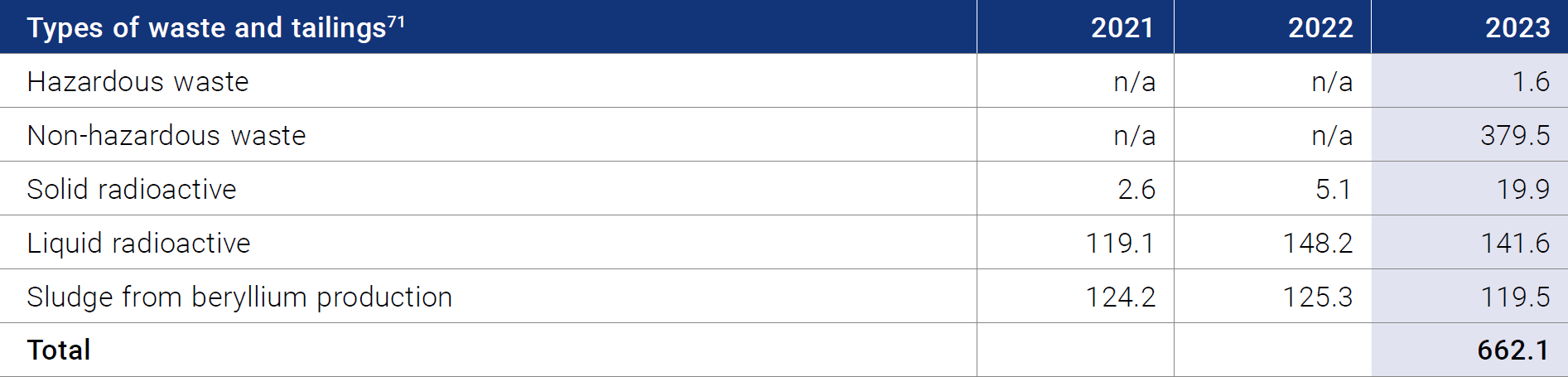
71 In view of the new waste classifier and changes to waste calculation methodology, the Company did not recalculate waste volumes for 2021 and 2022.
The Company classifies liquid radioactive waste and hydrometallurgical processing sludges of beryllium ore, not contaminated with radionuclides, as tailings.
In accordance with the new waste classification set in the Environmental Code of the Republic of Kazakhstan, there is hazardous and non-hazardous waste. The majority of waste generated by the Company is drilling mud. This type of waste is classified as nonhazardous in accordance with a recent sanitary and epidemiological assessment.
We have developed passports with basic information for hazardous waste, indicating description, hazardous properties, composition, toxicity and precautions for waste handling. Hazardous waste is transported in line with the applicable laws only by licensed organisations.
In 2023, the Company did not transport hazardous waste across borders.
RADIOACTIVE WASTE MANAGEMENT
In their operations, the Group’s enterprises generate solid and liquid radioactive waste, which are disposed of in specially designated areas for disposal.
In total, the Group generated 19,865.61 tonnes of radioactive waste (SRW) in 2023. The main type of SRW is radioactively contaminated soil due to the use of ISR mining method and Kazatomprom-SaUran LLP's operations in 2023 to mitigate the consequences of subsoil use at the Uvanas deposit.
Contribution of various SRW types from the Group to total SRW in 2023, %
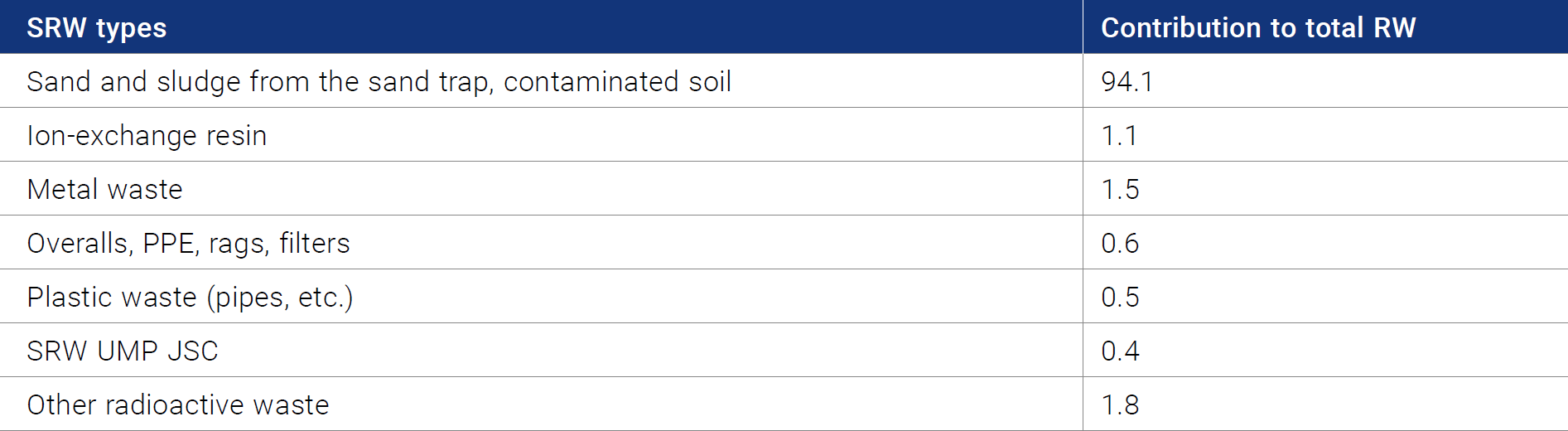
Only UMP JSC generates liquid radioactive waste (LRW), as in accordance with process regulations, other mining entities of the Group dispatch spent pregnant solutions to sand traps for reuse in the technological process. In 2023, UMP JSC generated 141,603.54 tonnes of LRW and 119,456 tonnes of sludge from beryllium production. The total of generated LRW and sludge from beryllium production is placed at the UMP JSC Tailings Storage Facility.

The Group's enterprises manage radioactive waste in accordance with the laws of the Republic of Kazakhstan and the best international practice.
In alignment with its commitment to the UN Global Compact and ESG principles, NAC Kazatomprom JSC adopted a comprehensive Radioactive Waste Management Programme for 2023-2030. This program establishes a unified Group policy and a midterm approach for responsible radioactive waste management.
The Programme's core objective is safe and efficient radioactive waste management, minimising its environmental impact and protecting health.
To achieve this objective, the Company held analysis of radioactive waste management and set four major tasks:
- Reduce radioactive waste generation.
- Improve radioactive waste management system and introduce new approaches.
- Conduct a comprehensive review of internal radioactive waste management documents and develop actionable proposals for strengthening the regulatory legal framework.
- Build stakeholders' trust and reputation.
To achieve its objectives and strengthen the internal regulatory framework, NAC Kazatomprom JSC implemented the following activities in 2023:
- Updated the Standard "Methodological Guidelines for Radioactive Waste Management", which establishes general organisational and technical requirements for managing radioactive waste generated by production facilities.
- Developed the Standard "System of Standards for Environmental Protection. Model Quality Assurance Programme for Radioactive Waste Management. Requirements for structure and content". The Standard defines the structure and content of quality assurance programmes for radioactive waste management across the Group.
- Developed the Rules for Inspections of Radioactive Waste Management System at Enterprises of NAC Kazatomprom JSC. The Rules define the procedure for organising and conducting inspections of Group's facilities that generate radioactive waste.
- The Group's enterprises that generate radioactive waste have developed and approved Quality Assurance Programmes for radioactive waste management. The Programmes establish a set of organisational and technical measures for quality assurance impacting nuclear, radiation, environmental and physical safety, and determine the radioactive waste management system at the enterprises.
In 2023, in an effort to update the regulatory legal framework for radioactive waste management, NAC Kazatomprom JSC representatives participated in the working group of the Committee on Ecology and Nature Management of the Mäjilis of Parliament. They were involved in the development of the draft law On Radioactive Waste Management.
TAILING STORAGE FACILITY MANAGEMENT
NAC Kazatomprom JSC takes a responsible approach to tailing facilities management and focuses on ensuring their physical and technological safety. The Company operates one tailing storage facility at UMP JSC in Ust-Kamenogorsk. The tailing storage contains five surface impoundments to place fluid tailings.
Tailing management site (tailing storage facility) is a structural subdivision of the UMP JSC maintenance centre.
Management and maintenance of the tailing storage facility stable operation takes place in accordance with the following documents:
- Technological regulation for the Operation of Tailing Management Site of UMP JSC.
- Technological regulation on Waste Management at UMP JSC Tailing Management Site.
- Other internal regulatory documents of NAC Kazatomprom JSC and UMP JSC.
The Technological regulation for the Operation of Tailing Management Site of UMP JSC applies to the technological process of receiving and disposal of industrial waste and establishes requirements for the process flow, and maintenance of technological parameters within the set limits, which ensure safety and accident-free process operation, as well as requirements for the processes of receiving, disposal, accounting and transportation of liquid and solid industrial waste; receiving, disposal and accounting of liquid and solid radioactive waste of UMP JSC subdivisions received at the Tailing Management Site of UMP JSC.
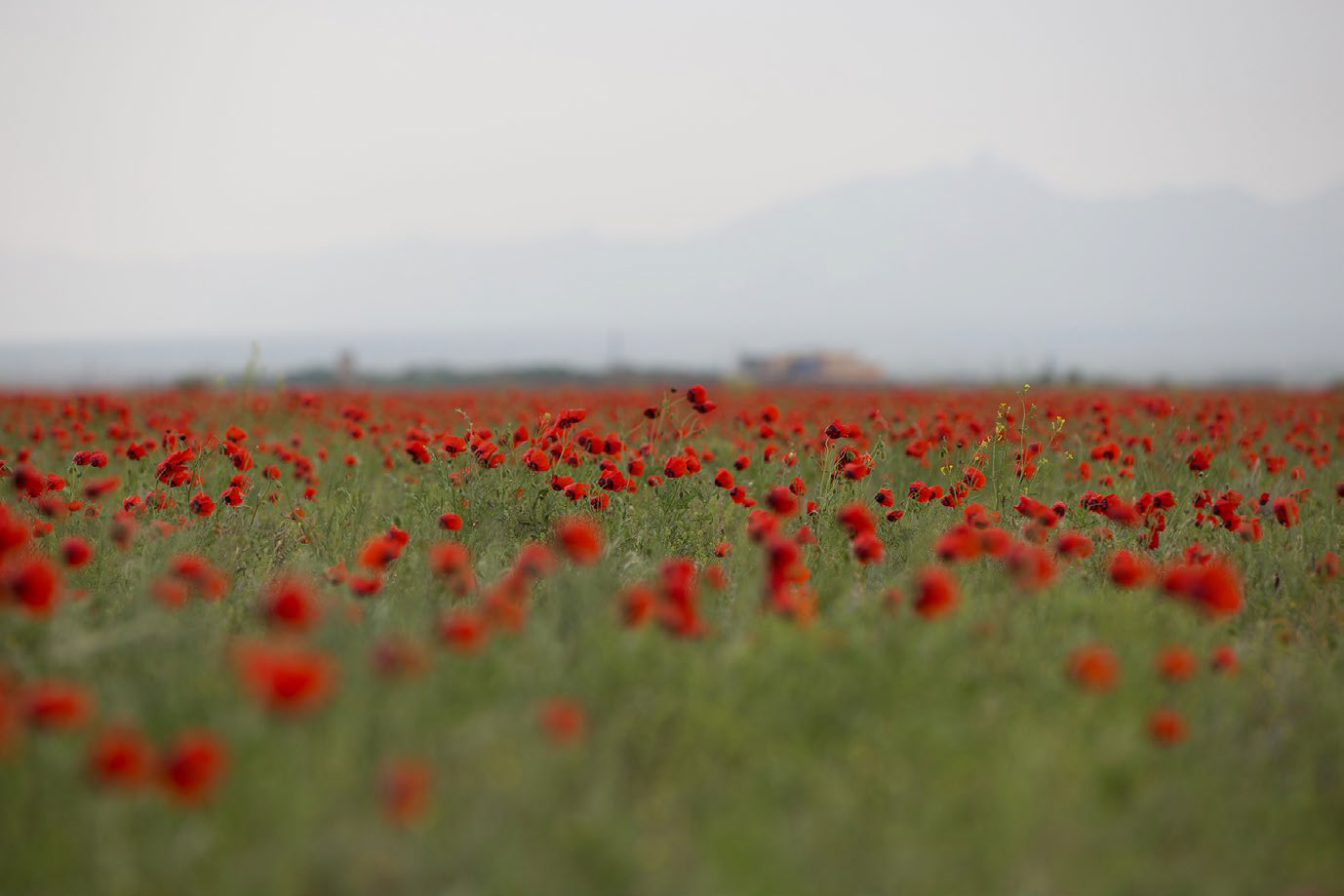
The Technological regulation on Waste Management at UMP JSC Tailing Management Site, approved by the Chairman of the Management Board of UMP JSC on 30 September 2023, to manage the site of the operating Tailing Management Facility of UMP JSC for 2023- 2042 was developed in accordance with the Code of the Republic of Kazakhstan On Subsoil and Subsoil Use, the Environmental Code of the Republic of Kazakhstan. It sets the terms of subsoil use for storage and disposal of hazardous substances (industrial waste) at the site of the operating Tailing Management Facility of UMP JSC.
In accordance with the Environmental Code of the Republic of Kazakhstan, the Company carried out an environmental impact assessment at the tailing management site of UMP JSC and conducts ongoing monitoring of the condition of hydraulic constructions and environmental monitoring in the adjacent areas.
UMP JSC is governed by the following documents in the field of emergency response and emergency preparedness:
- Emergency response plan for hydraulic structures of the Tailing Management Site of UMP JSC (approved by the Director for Technical Preparation on 14 November 2023).
- Emergency response plan for pumping (slurry pumping) stations of the Tailing Management Site of UMP JSC (approved by the Director for Technical Preparation on 13 November 2023).
Emergency response plans for the tailing management site were prepared in accordance with the requirements of the Instruction on development of emergency response plans and conducting drills and emergency drills at hazardous production facilities and the Law of the Republic of Kazakhstan On Civil Protection No.188-V dd. 11 April 2014.
UMP JSC has all material and financial resources to respond to emergencies at its tailing storage facility and remediate the damage quickly.
BIODIVERSITY
Despite that Kazatomprom’s operations do not have a direct material impact on biodiversity, we understand and accept the importance of preserving biological diversity in the region of our presence, making every effort to study the state of flora and fauna in the territory of uranium deposits.
The Company joins forces with public organisations for biodiversity conservation and protection. For example, Kazatomprom's subsidiary, IHT LLP, has a consortium agreement with the Institute of Zoology to conduct comprehensive research on the protection of birds from the dangers of power lines as part of Kazatomprom's programme.
We make efforts to prevent threats to biodiversity by investing significant resources in risk analysis at all stages of our operations. Environmental risks arising from our operations primarily relate to the disturbance of soil and vegetation and the displacement of animals outside their usual habitat. Striving to reduce environmental risks, the Company approved a standard for assessing and monitoring biodiversity during the industrial mining of uranium deposits and during the post-reclamation period.
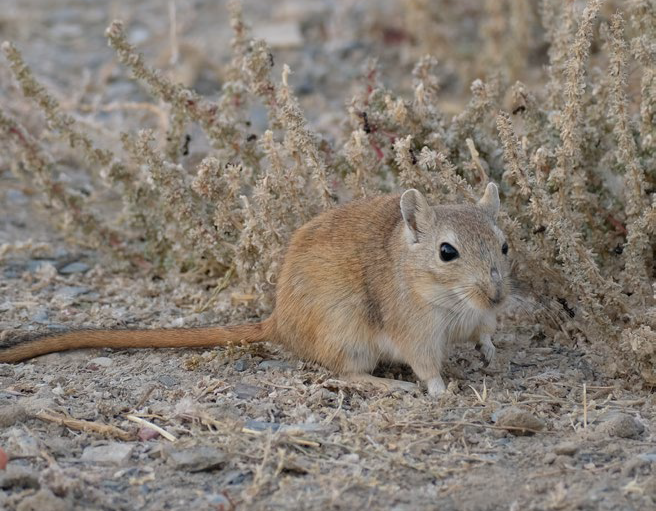
The total area of land owned, leased and managed by the Group is 105,477.99 hectares.
Information about the Group's sites/deposits borderingspecially protected natural areas (reserves/ wildlife area):
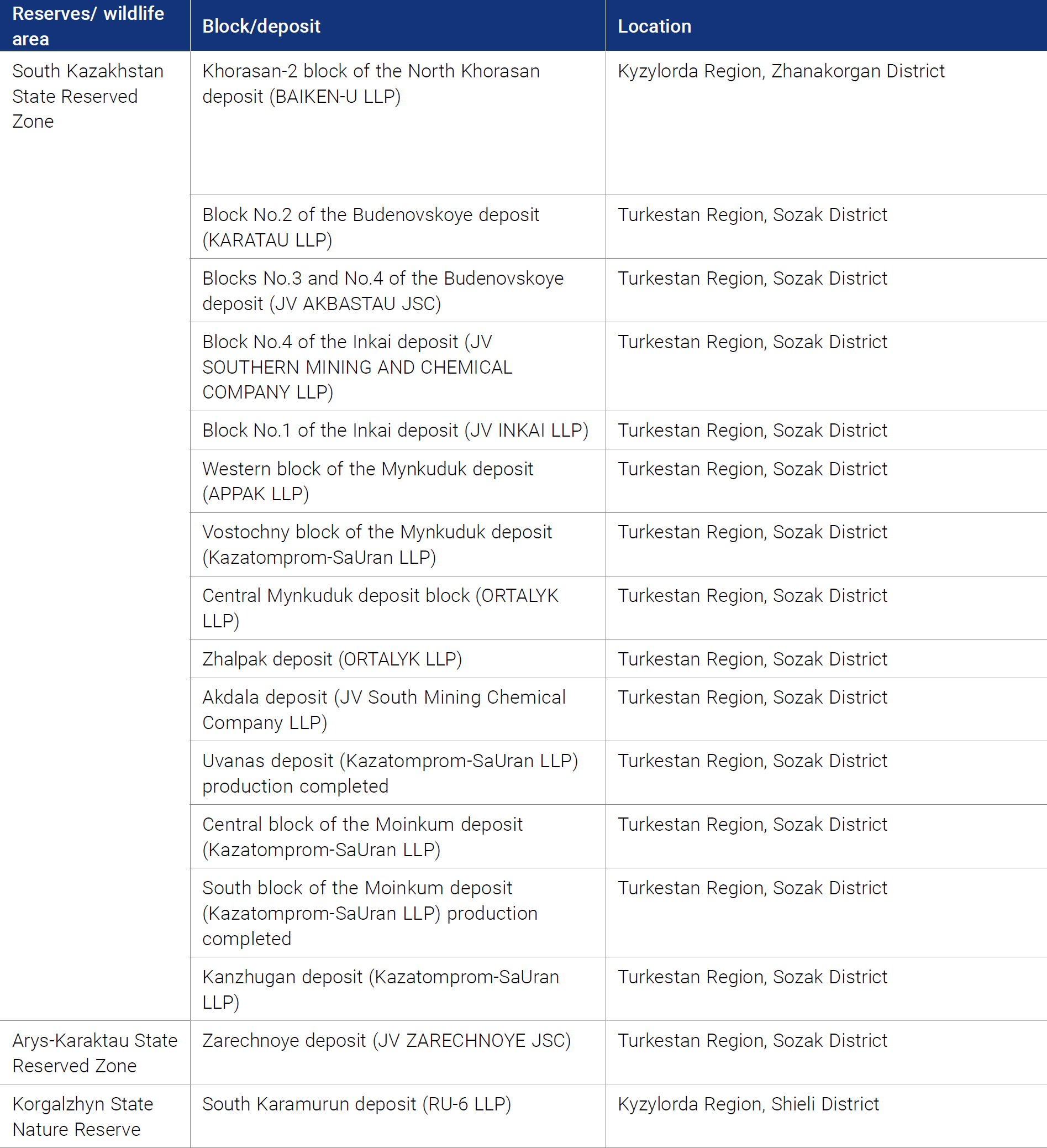
Kazatomprom operates on industrial land and in settlements in line with the applicable laws. In 2023, all subsidiaries and affiliates within the scope of the project for the implementation of the ESAP Roadmap were covered by biodiversity assessment studies carried out in the territories of production sites.
As part of the implementation of the ESAP Roadmap, Kazatomprom continued the implementation of the Programme of Bird Protection from the impact of power lines in the reporting period. We also carried out comprehensive environmental studies, including biodiversity assessments in the territories adjacent to 12 uranium mines in Southern Kazakhstan: Khorasan-1, Khorasan-2, Central Moinkum, South Moinkum, Kanzhugan, Kulandy, Karatau, Western Mynkuduk, Eastern Mynkuduk, Uvanas, Inkai and South Inkai.
Studies were carried out on the territory of mine land allotments and within 10 km to identify possible manmade and cumulative impacts on environmental objects and the local population. In 2023, the total area of the studied territories was 9,000 square metres.
The biodiversity assessment took place in accordance with ST NAC 17.6-2022. "Methodological Guidelines for Biodiversity Assessment at Uranium Fields, Production Facilities and Adjacent Territories" at South Inkai, Eastern Mynkuduk, Uvanas, Kanzhugan, South Moinkum, and Central Moinkum mines.
In the studies, we analysed the production operations from the environmental perspective, the available background data on the condition of air, surface and groundwater. We also studied soil types, the structure of underground aquifers, and the species composition of flora and fauna. We collected new data on the ecological state of the soil cover, water resources, and atmospheric precipitation. For the first time, we carried out studies of microbiocenosis and phytotoxicity of soils. We identified potential channels of impact on environmental objects and compiled a primary list of environmental risks.
The results of the study concluded that there were no impacts of the production activities on the indicators of the state of the environment beyond the sanitary protection zone.
In 2024, the Company will continue the environmental condition and biodiversity assessment of Kazatomprom's uranium deposits.
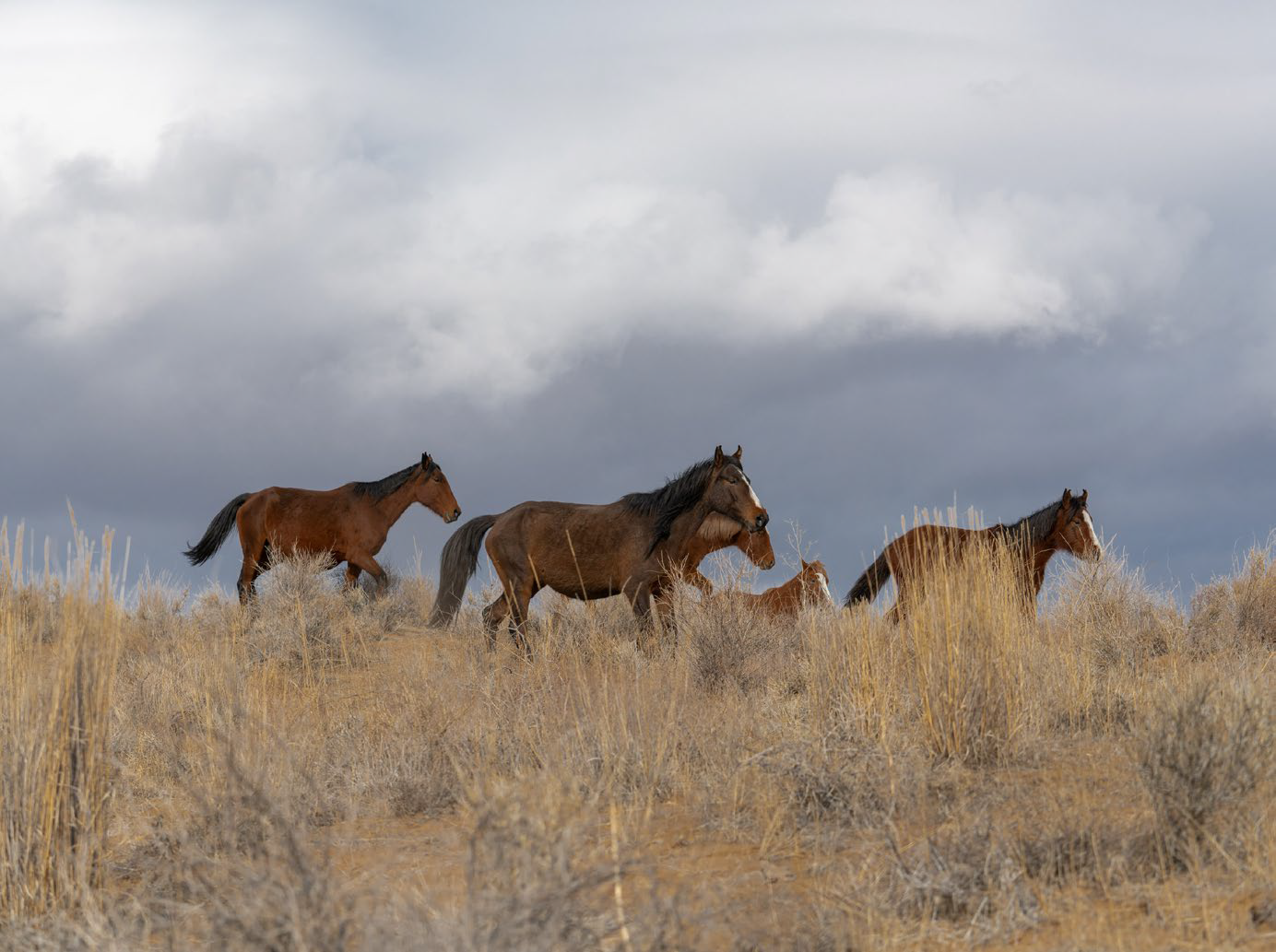
REMEDIATION OF SUBSOIL OPERATIONS AND LAND RECLAMATION
The Company ensures responsible remediation of subsoil operations and effective reclamation efforts in line with the Subsoil and Subsoil Use Code of the Republic of Kazakhstan, other legal and internal regulations:
- Standard Methodological guidelines for calculating the estimated cost of subsoil operations remediation (ARO assessment) in the subsidiaries and affiliates of NAC Kazatomprom JSC.
- Standard Arrangements for Remediation of Subsoil Operations and Land Reclamation. Methodological guidelines.
- Instruction Criteria for remediation of production activities at uranium mining sites.
NAC Kazatomprom JSC fulfills its Asset Retirement Obligations (ARO) at uranium mining enterprises.
This includes calculating annual cost estimates for remediation and maintaining a permanent commission to oversee the effective remediation of subsoil use and reclamation of disturbed lands.
Demonstrating its commitment to environmental responsibility, NAC Kazatomprom JSC launched a progressive liquidation programme in 2023. This proactive approach involves dismantling spent technological units at uranium mining sites before the subsoil use contracts expire. This initiative will deliver several key benefits: reduced environmental impact, lowered future financial obligations associated with decommissioning, and positive impact on local communities where the Company operates.
As part of progressive liquidation programme implementation, in 2023, NAC Kazatomprom JSC developed and implemented the Standard Procedure for progressive liquidation of spent operational process units at in-situ recovery mining facilities.
In 2023, Kazatomprom-SaUran LLP started work at the Uvanas deposit to remediate subsoil use operations and restore disturbed lands in accordance with the Deposit Liquidation Project, which passed state expertise in the authorised state bodies and received environmental approval. The activities include:
- Elimination of the uranium mining geotechnological site facilities (process wells, process solution pipelines, acid pipelines and other infrastructure).
- Dismantling of buildings and structures of the industrial site and administrative buildings.
- Reclamation works (clean-up of contaminated areas, surface planning, restoration of vegetation cover).
- Post-reclamation soil and groundwater monitoring.
Kazatomprom works on an ongoing basis to restore lands disturbed by mining operations. While developing the deposits, the Company carries out reclamation works to restore the landscape and vegetation and return the land into economic use.
There are no protected or restored habitats within the above 26 deposits/sites of Kazatomprom. The Company conducts annual consultations on environmental issues with stakeholders, including representatives of the local community.
International standards, methodological guidelines and relevant qualifiers, as well as the Environmental Code of Kazakhstan and ST 17.6-2022 Standard "Methodological Guidelines for Biodiversity Assessment at Uranium Deposits, Production Facilities and Adjacent Territories" guide the biodiversity assessment.
Our operations do not pose a threat to animals and plants listed in the Red List of the International Union for Conservation of Nature and Natural Resources (IUCN) and the Red List of the Republic of Kazakhstan and threatened with extinction.
The in-situ recovery does not change the landscape, which contributes to the conservation of endemic flora and fauna. The death of animals and desertification of territories are excluded. Once uranium mining is completed and the consequences of subsoil use are eliminated, the animals return to their natural habitat.
At present, the conservation status of animal and plant species included in the Red List is: 6 endangered, 3 extinct, 14 vulnerable (close to vulnerable), 1 nearthreatened, and 25 least concern species.
PLANS FOR 2024 AND A MEDIUM TERM
In 2024, Kazatomprom plans to implement a number of environmental protection measures:
- continue training employees of subsidiaries and affiliates responsible for environmental protection, in particular: production and consumption waste management, biodiversity assessment at uranium mining deposits, environmental monitoring at enterprises;
- continue research programme to explore the impact of Kazatomprom’s operations on the environment and the local population (Environmental and Social Research Programme, ESRP) and the Zero Waste Programme of Kazatomprom, seeking to develop measures to reduce and minimise production and consumption waste generated at the enterprises of the uranium mining industry;
- continue implementing the Programme of Bird Protection from the Impact of Power Lines;
- continue efforts to create a database of the environmental monitoring system and the environment of uranium mining enterprises of the Group;
- participate in the implementation of the Decarbonisation and Carbon Neutrality of NAC Kazatomprom JSC until 2060;
- conduct implementation of Water Resources Management Strategy in subsidiaries and affiliates;
- organise and roll out the RHYTHM corporate programme at Kazatomprom to mark the World Environment Day;
- conduct an external diagnostic audit in subsidiaries and affiliates based on the results of ESAP Roadmap implementation;
- participate in working groups on amendments to the environmental laws of the Republic of Kazakhstan that have an impact on Kazatomprom's operations; collect and analyse proposals on the amendments and supplements to the environmental laws in Kazakhstan that have an impact on the Company's operations;
- hold environmental campaigns (Earth Hour, World Clean Day), community work days, environmental events, open days, master classes and other environmental communications with stakeholders;
- conduct further Radioactive Waste Management Programme of NAC Kazatomprom JSC for 2023- 2030;
- conduct further works at the Uvanas deposit to remediate subsoil use operations.
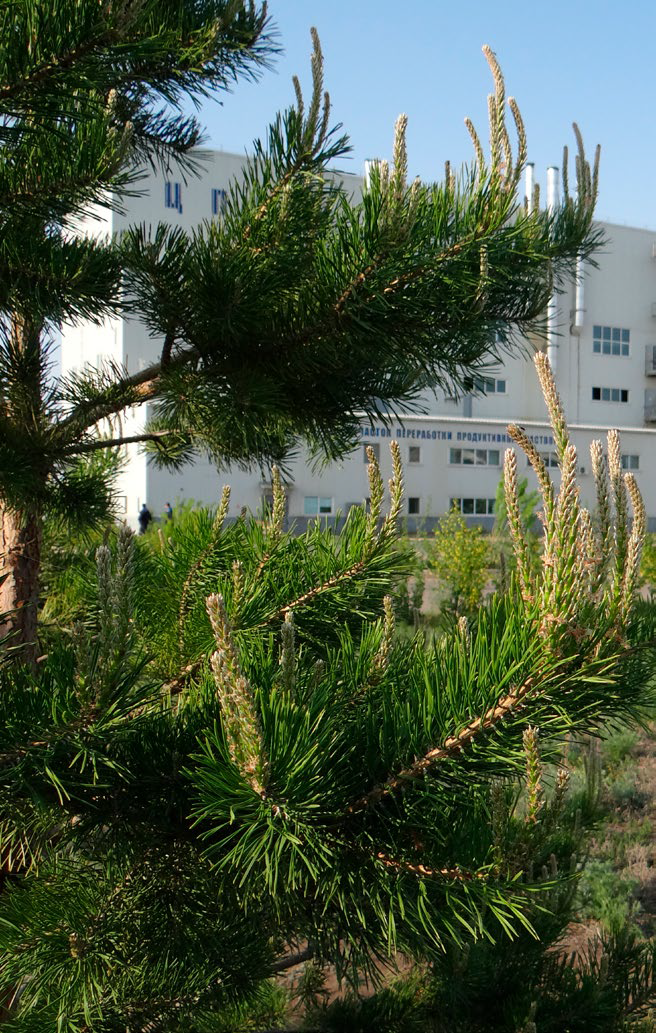
Deposit lifecycle management
The Group operates 26 deposits/sites. The deposit is developed by the ISL method in succession by dividing it into technological blocks. It takes an average of three to four years to develop one technological block at the deposit.
Uranium mining by the ISL method involves a set of operations:
- mining preparation works (construction of technological holes, installation of trunk and intrablock piping, acidification of the mining mass);
- uranium leaching directly in the subsurface and production of productive solutions (active leaching, leaching and additional leaching).
Advantages of natural uranium mining by the ISL method compared to conventional uranium mining:
- lower cost of mine development;
- shorter construction time;
- lower cost of production;
- reduced environmental impact;
- reduced risk to health and safety.
Uranium mining by the ISR method in Kazakhstan
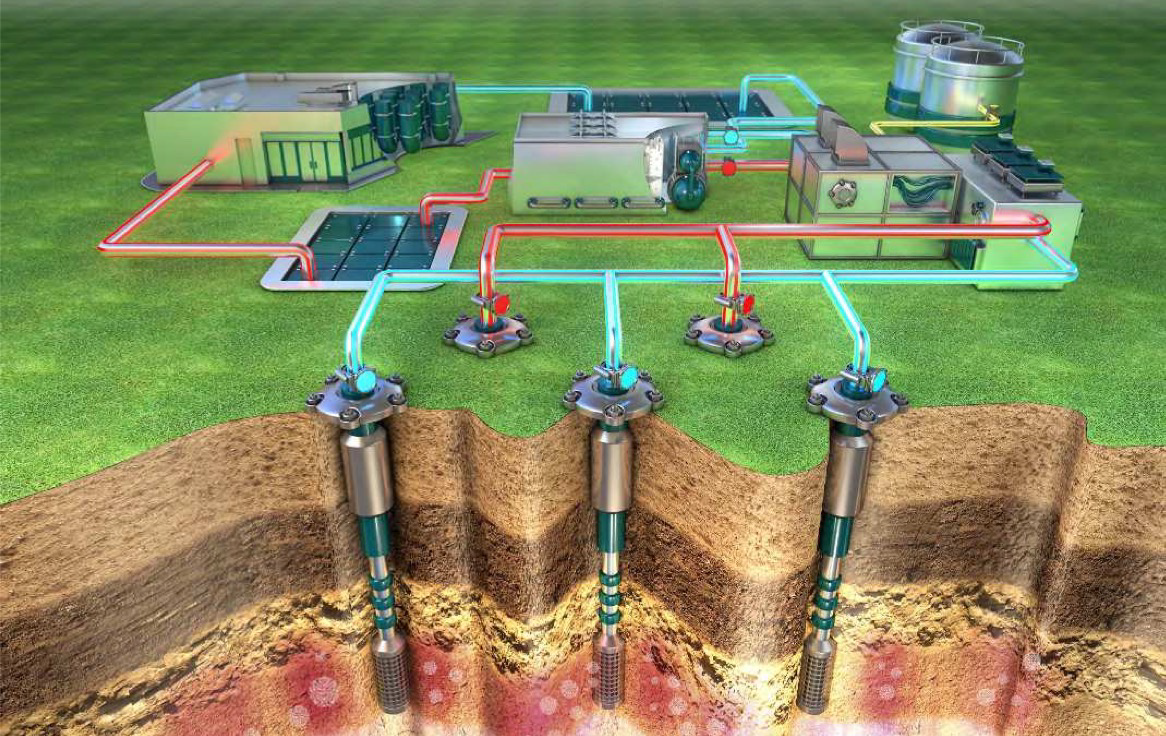
Health and Safety
OUR APPROACH
Kazatomprom prioritises the health and safety of employees and contractors over production and financial performance. The Company's commitment is reflected in our occupational health and safety (H&S) policy, which emphasises responsibility for safety, a zero-tolerance approach to injuries among employees and contractors, and rigorous risk management practices across all production sites.
The main regulatory documents that define the principles and rules of occupational health and safety and fire safety of the Company:
- Occupational Safety and Health Convention (C 155) (International Labour Organization, 1981), Occupational Safety and Health Recommendation (R164) (International Labour Organization, 1981), ISO 45001 Occupational Safety and Health Management System.
- Labour Code of the Republic of Kazakhstan.
- Law of the Republic of Kazakhstan On Civil Protection.
- Law of the Republic of Kazakhstan On the Use of Atomic Energy
- Rules for Ensuring Industrial Safety in Geological Exploration, Mining and Processing of Uranium.
- Policy of NAC Kazatomprom JSC in the field of health and safety, environmental protection, radiation and nuclear safety.
- Occupational Health and Safety Code.
- Standard "Unified industrial safety management system".
- Standard "General requirements for the occupational health and safety management system. Guidelines".
- Standard "Requirements for contractors in the field of industrial safety".
- Standard "Organisation of fire safety at Kazatomprom's enterprises".
The Company's H&S principles and rules are binding on all employees and contractors of the Group.
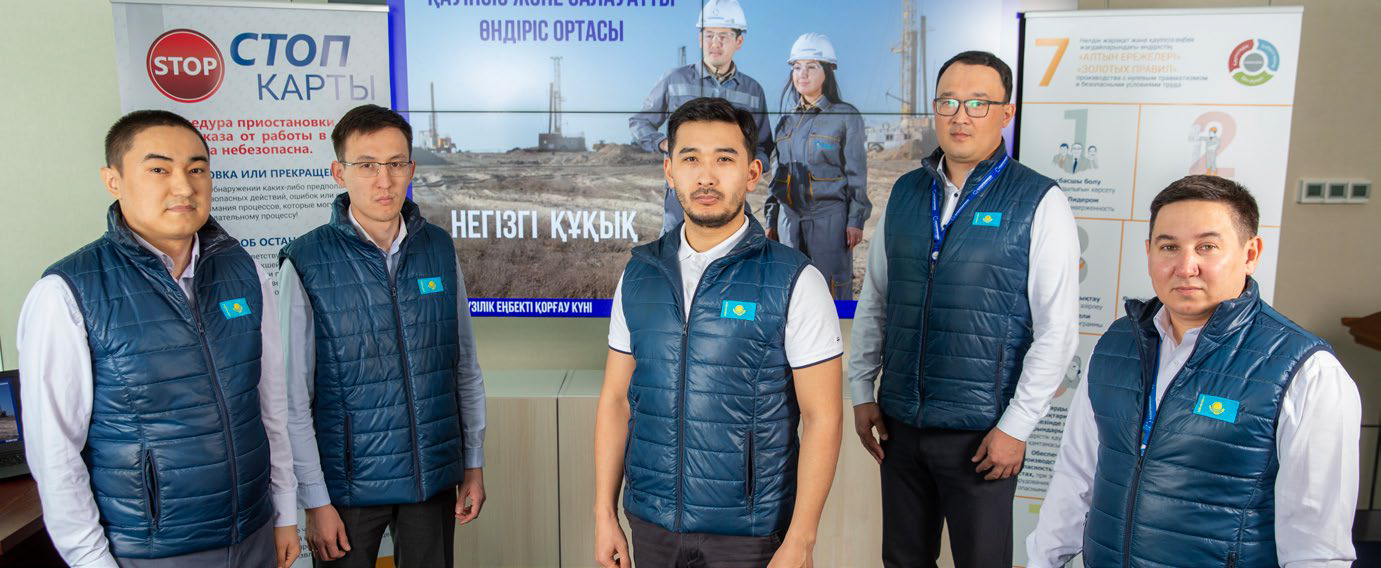
Kazatomprom’s HSE management system
The Management Board Chairman conducts regular meetings of the CEOs and executives of subsidiaries and affiliates to discuss the health and safety culture in the Company.
The Company's enterprises implement regular H&S measures. The Board of Directors and the Risk Management Committee of Kazatomprom Management Board regularly review the results of all H&S measures.
The H&S report is submitted to the Chairman and the Board of Directors for analysis.
The H&S function accountable to the Chairman of the Management Board coordinates efforts to improve the H&S system in the Company, its subsidiaries and affiliates. The H&S Department is responsible for the prevention of violations of H&S standards and rules, fire safety, prompt response to incidents and criticalities, as well as the monitoring, analysis, and control of the H&S risks.
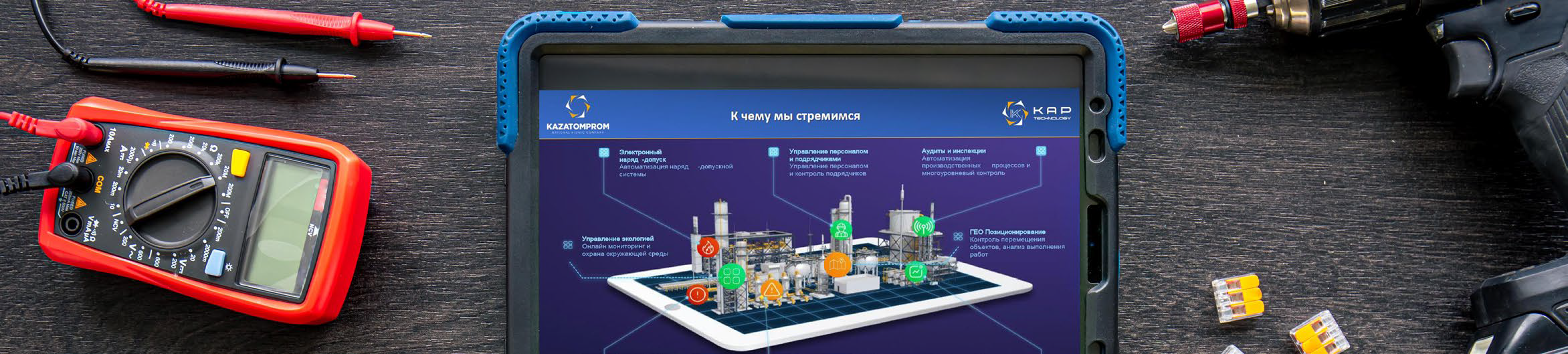
In accordance with Kazatomprom's policy, all occupational H&S functions at subsidiaries and affiliates are subordinate to their CEOs.
Kazatomprom regularly analyses the structure of qualifications and competencies of the H&S units at the Group's subsidiaries and affiliates to improve the H&S efficiency and remain in line with the requirements of national laws and the best world practices.
H&S RISK ASSESSMENT
Kazatomprom views risk management as a key component of its corporate governance system including H&S. The Company takes a holistic approach to preventing industrial injuries and occupational diseases, as well as to identifying, analysing, and minimising industrial risks.
All Kazatomprom's activities are conducted in accordance with the fundamental regulatory and legal H&S documents. The main ones are the Labour Code and the Law of the Republic of Kazakhstan On Civil Protection. The Company also adheres to a number of by-laws regulating H&S for various types of activities – mining and processing of uranium, operation of hazardous equipment, e.g. lifting mechanisms and pressure vessels.
The regulatory documents guide the procedures for investigating accidents and incidents at Kazatomprom's companies. The Company timely provides information regarding each lost time accidents in the workplace to the authorised government agencies. In the case of group accidents or accidents with a severe injury, the Company is obliged to conduct a special investigation with the involvement of a governmental H&S inspector as required by the laws of the Republic of Kazakhstan. The Company also conducts internal investigations of all accidents to reveal the causes using the "Why Five" and "Why Tree" methods. The Chairman of the Board and executives regularly review the results of internal investigations. An information bulletin is issued and disseminated to all structural units describing all incidents, traffic accidents, fires, and other emergencies, enabling workers to avoid such situations in the future.
The Company immediately prepares an information bulletin and promptly communicates it to all affiliates when any incident occurs. This information is communicated to employees via e-mail, unscheduled briefings and by posting information on information boards and in conspicuous places.
The Company also keeps an updated register of risks, with occupational injury risks included. To reduce occupational injuries, Kazatomprom develops and implements comprehensive measures to continuously improve the level of H&S, prevent occupational injuries, and achieve the established safety standards.
These actions include:
- Developing measures to prevent the recurrence of accidents.
- Conducting regular inspections of the Group's assets for compliance with H&S regulatory acts.
- Regular informing of subsidiaries and affiliates about the results of industrial injuries analysis and providing proposals for their prevention.
- Holding valid and up-to-date workplace certification, which means audits of working conditions and provision of suitable work-ware and protective equipment to employees of subsidiaries and affiliates.
- Keeping records of potentially unsafe conditions, acts, and near-miss incidents at Kazatomprom companies (Near Miss reporting).
- Introducing the process of terminating unsafe works by employees with STOP Cards.
- Using the tool "Behavioural H&S audit".
- Digitalising HSE management, in particular implementing the e-system for issuing and using work permits.
- Analysing and preventing risks.
Health and safety risks are identified at each production site. A register of identified risks is communicated to employees in that area and is posted in conspicuous places. The registers are regularly reviewed and updated. Identified risks from all production areas are put into an overall register of occupational health and safety risks.
The Company operates a system to identify and record Hazardous Conditions (HC), Hazardous Activities (HA) and Near Miss (NM). All HC, HA and NM are registered in the eCAP information system and accessible to all employees. The registration of HC, HA, and NM does not entail any negative consequences for the employee, on the contrary, it is taken into account in motivational incentives.
The Company also identifies and records hazards that have caused or may cause the risk of severe incidents. The Company identifies the risks of severe incidents resulting from accidents, tripping and falls, and chemical exposure as the most significant.
The Group conducts behavioural H&S audits for all its companies. The main goal is to analyse the behaviour of employees when performing production tasks and to prevent behaviour-related risks.
Constant analysis and monitoring of data show that safety violations, which are often linked to a human factor, is the common threat at any Group company. Kazatomprom provides strict control over compliance with industrial safety rules at workplaces, as well as controls the technical condition of equipment, and the availability of all necessary internal documents, including instructions, procedures, and standards.
Kazatomprom applies a risk-based approach to improve the H&S system. H&S Department developed a register of functional risks, which includes the major occupational H&S hazards and risks associated with the Department's activities. The register of functional risks is reviewed and updated annually. The Company also applies a risk-based approach to planning and conducting inspections/audits. This helps to identify the most dangerous production areas and focus on the major risks, improve quality, and reduce the waste of time resources.
In 2022, Kazatomprom adopted a standard defining the procedure for issuing and using work permits for hazardous operations, as well as a form of a Safe Work Analysis. The latter helps assess existing and potential risks and take measures to mitigate them before work commences. In 2023, the Company began to develop the e-system for issuing and using work permits.
HSE PERFORMANCE
The safety and well-being of employees are top priorities for Kazatomprom. The Company implements comprehensive measures and the world’s best practices to prevent accidents and incidents. Kazatomprom conducts regular training campaigns to raise the health and safety awareness of its personnel. All these actions are aimed at improving the safety culture throughout the Group and at preventing possible negative consequences.
Executives of subsidiaries and affiliates cascade personal H&S commitments to managers at all levels.
- Take leadership – demonstrate commitment
- Identify hazards – control risks
- Define targets – develop programmes
- Keep improving the safe and healthy system – be extremely well-organized
- Ensure safety and health at workplaces, in operation of machines and equipment and handling hazardous substances
- Improve qualifications – develop competence
- Invest in people – motivate by participation
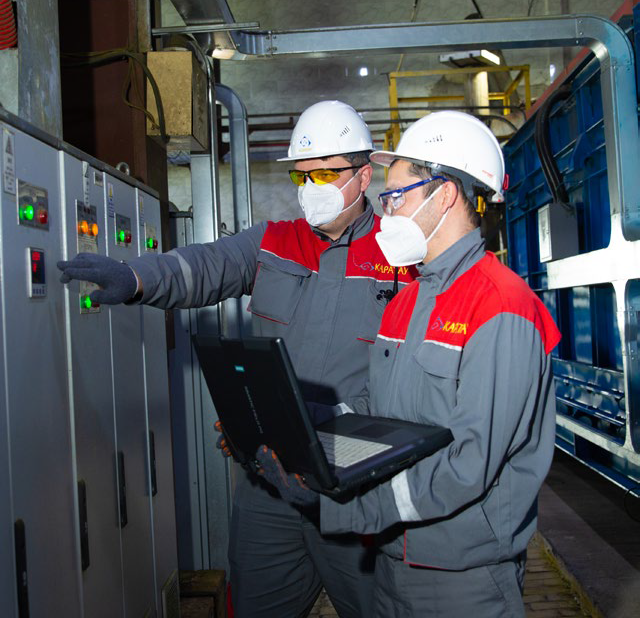
The Company established special safety information boards to explain personal responsibility and leadership to raise the H&S awareness of the Group's employees in the rotation camps of subsidiaries and affiliates.
The health and safety awareness activities require both a consistent approach and investment.
In 2023, the Company invested KZT 12.47 billion in health and safety. Fire safety investments amounted to KZT 1.3 billion.
The Company takes a responsible approach to health and safety matters, investing heavily in health and safety measures.
The Company has a system for the employee performance appraisal in place. It is based on a list of key performance indicators (KPIs). The health and safety of the Group's employees is one of the key performance indicators. “Improving safety culture” indicator is one of the major H&S KPIs, which includes such mandatory elements as “Lost Time Injury Frequency Rate (LTIFR),” “Number of behavioural safety audits conducted (BSA),” and “Number of non-work related fatalities (NWRF)”. This high-level KPI is cascaded to performance indicators for management, employees of the Company and subsidiaries and affiliates. The KPI system covers all employees of the Company from Kazatomprom Board Chairman to an ordinary employee.
To ensure the effective identification and implementation of measures aimed at improving the H&S management system in the Company, Kazatomprom holds an annual corporate meeting on the H&S performance and future plans. The results of the meeting are recorded in minutes along with specific tasks aimed at H&S improvement.
In line with the Unified Occupational Safety Management System, each subsidiary/affiliate has a production control system that helps prevent and eliminate deviations from projects, process regulations, standards, rules and instructions, established work procedures, as well as to prevent emergencies and injuries.
The first level of control is the responsibility of the immediate supervisor of works (foreman, shift supervisor, mechanic, etc.) and should be carried out at least once per shift. The second level of production control is carried out by the head of the subdivision. The third level of production control is carried out by the Production Safety Department of the subsidiary/ affiliate with the participation of the head of the subdivision and specialists in their respective areas. The fourth level of production control is carried out by a commission chaired by the CEO of the subsidiary/ affiliate The commission includes managers, line specialists and specialists from the H&S service/ departments. The fifth level of production control is carried out by a commission of Kazatomprom’s headquarters. The Commission is composed of the Company's top managers, specialists of the Company's areas of expertise and the head or specialists of the occupational safety service.
In 2023, subsidiaries and affiliates carried out scheduled and targeted inspections as part of production control for compliance with the legal acts and internal H&S requirements. In addition, the Company has a practice of peer checks where the subsidiaries and affiliates inspect each other in accordance with an approved schedule of peer checks. This practice improves communication and allows experience sharing between subsidiaries and affiliates.
Competent H&S authorities carry out inspections of the Company's subsidiaries and affiliates in line with the Labour Code and the Entrepreneurial Code of the Republic of Kazakhstan.
In 2023, all production sites and employees of the Company were covered by internal and external audits.
The H&S Management System Corporate Standard is based on the laws of the Republic of Kazakhstan, the Reference Model for H&S Management of Samruk-Kazyna Portfolio Companies, as well as advanced international standards and practices.
PERFORMANCE
The Company's Risk Register highlights occupational injuries as one of the key risks. The Group has developed and implemented a list of comprehensive measures to prevent the risk of occupational injury and minimise its consequences.
The analysis of the H&S situation shows that major causes of personal injuries at Kazatomprom’s subsidiaries and affiliates, as well as of their contractors, include traffic accidents, handling sulphuric acid, falls and tripping.
OCCUPATIONAL INJURIES AND ACCIDENTS
Despite a considerable decrease in the number of occupational accidents, Kazatomprom continues to make every effort to achieving its goal – to reduce the number of accidents to “zero” and ensure accidentfree production activities and safe working conditions for employees.
In 2023, four accidents happened at Group companies, resulting in five injuries, one of which was severe and four of which were non-serious.
LTIFR made 0.15 in 2023.
Accidents in 2023

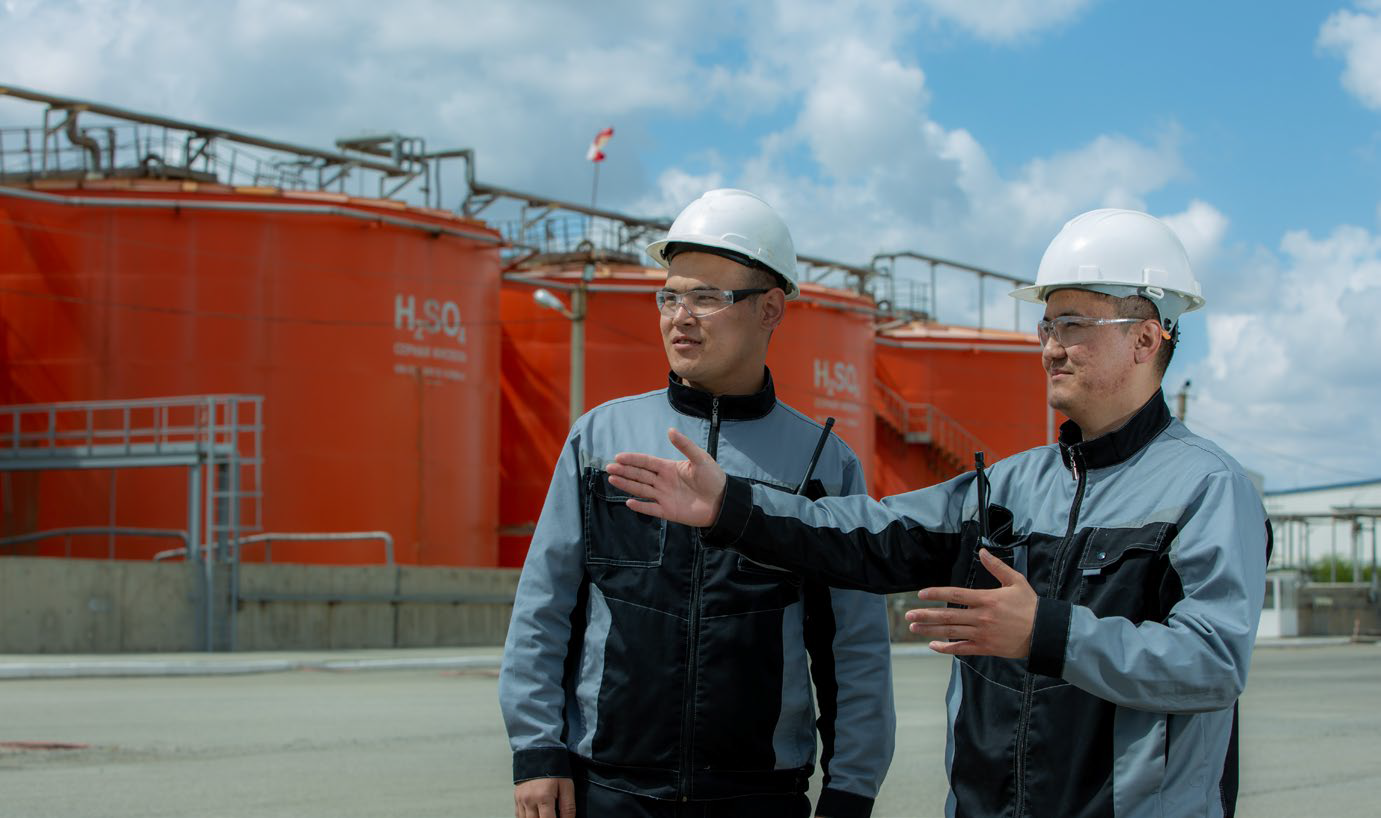
The Company carried out thorough investigations of all accidents in accordance with the established procedures, which included a detailed analysis of the circumstances to determine their root causes and develop prevention measures. The investigation process suggested the assessment of all aspects, from technical malfunctions of equipment to the physical and emotional state of employees.
We used the investigation findings to develop a set of measures that were implemented in all companies of the Group in a timely manner.
PREVENTING OCCUPATIONAL INJURIES
The Group constantly implements measures aimed at preventing occupational injuries, preventing and minimising risks and hazards.
These include:
- Conducting scheduled and unscheduled safety briefings.
- Organizing meetings of occupational H&S services to analyse the root causes of accidents and develop prevention measures.
- Raising employees’ awareness about hazards and risks in the workplace, materialised risks and hazardous conditions, and accident prevention and avoidance measures.
- Employee training and upskilling.
- Identifying near misses and taking corrective measures.
- Conducting behavioural H&S audits.
- Using STOP Cards by employees to stop unsafe work, or refusal by employees to do work if they believe the work cannot be done safely.
- Developing and updating internal regulations (standards and instructions) on occupational safety.
- Carrying out checks at five levels of production control.
- Using Lockout/Tagout.
- Training top management at a bespoke course, Leadership in Occupational Safety.
- Conducting regular employee surveys to assess satisfaction with the HSE system.
- Enhancing the motivation by holding an annual Chairman of the Board Award among employees of subsidiaries, affiliates, and jointly controlled organisations of NAC Kazatomprom JSC in the areas of occupational safety, environmental protection, industrial and radiation safety. The number of identified near-misses is among the criteria to select the best employees.
In 2020, the Company introduced a stop card tool across all subsidiaries and affiliates to prevent unsafe works. When introducing the stop card procedures, CEOs of the subsidiaries and affiliates addressed all employees to confirm that actions to stop unsafe work would not entail any negative consequences for employees, including no disciplinary sanctions. In 2022, employees registered 357 stop cards.
Furthermore, in order to increase transparency and develop a speak-up culture among the company's employees, a HSE mailbox (HSE@kazatomprom. kz) has been implemented across all facilities. This mailbox accepts questions, requests, complaints, and suggestions regarding occupational safety from all interested employees.
Video conference meetings are held monthly with the heads of H&S departments of subsidiaries and affiliates to discuss H&S issues, analyse root causes of accidents and prevent the recurrence of incidents. When necessary, the Company updates risk registers. All recommendations and instructions for measures implementation are recorded in protocols. Subsidiaries and affiliated companies provide information to the headquarters on the implementation of measures within the framework of approved reporting.
As required by the Labour Code of the Republic of Kazakhstan, the Company regularly conducts H&S briefings with employees, regardless of their education, work experience in this profession or position. The H&S briefing is carried out by the H&S service or by the authorised person, according to the programme developed by the H&S service. The programme includes the requirements of H&S norms, standards, rules and instructions, as well as the requirements for the safe conduct of production works. In addition, videos with H&S briefings are available to the Group's employees.
Measures taken by the Company's subsidiaries and affiliates to improve occupational H&S have prevented industrial accidents (uncontrolled explosions, release of hazardous substances or destruction of buildings).
OCCUPATIONAL DISEASE PREVENTION AND HEALTH PROTECTION
The key goal of Company is to protect employee's life and health. The Company’s employees have access to social benefits, including health improvement and spa treatment programmes. In addition, as part of a collective bargaining agreement between the Group and the trade union, the employees can enjoy additional programmes for health rehabilitation and treatment. Kazatomprom has a medical insurance system in place for its employees.
Employees of subsidiaries and affiliates are provided with three meals a day as established by the laws of the Republic of Kazakhstan.
We promote health care services. Based on an audit of health care services, the Company developed a checklist, which includes an exhaustive list of requirements for monitoring compliance with the H&S laws of the Republic of Kazakhstan and the quality of medical services. Health care facilities and services of subsidiaries and affiliates became digital.
As part of a trend towards digitalisation, we continued automating pre-shift health checks. Compared to 2022, the technical capacity of mining enterprises almost doubled – from 64% to 100%. All mining enterprises of the Group installed electronic systems for pre-shift health checks.
Mandatory training package by Kazakhstan Nuclear University for employees of subsidiaries and affiliates includes the first aid training. Medical professionals perform practical testing of knowledge acquired by employees.
To detect diseases at early stages, the Company arranges annual medical examinations for production personnel, which take into account harmful and (or) hazardous production factors, professions and jobs.
To prevent occupational diseases, the Company ensures operational control and improves working conditions based on the results of workplace certification. Based on the recommendations of the medical commission, employees undergo follow-up examinations, outpatient and inpatient care, screening, health rehabilitation and treatment, and dietary meals. Within the context of social partnership with the Trade Union of Nuclear Industry Workers, employees can access programmes for health rehabilitation and treatment, and fitness clubs.
Medical facilities of subsidiaries and affiliates have a common infrastructure and are equipped with the necessary equipment for medical care. All subsidiaries and affiliates have medical posts in place equipped with defibrillators, ECG and other devices, equipment and materials to administer medical aid to employees. Medical facilities have a sufficient number of staff and ambulance vehicles. A total of 155 medical staff at subsidiaries and affiliates, including 33 doctors and 106 paramedics, work in 63 medical facilities, including doctor's and paramedic stations, first-aid posts, and medical inspection rooms. There are 17 ambulance vehicles for emergency and urgent care and medical evacuation.
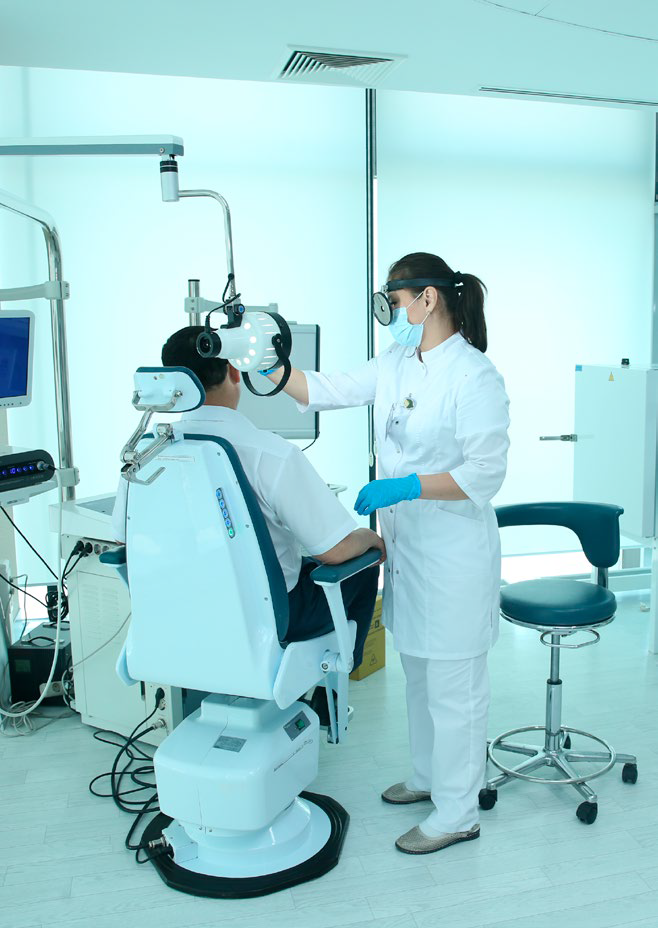
PROMOTING THE H&S CULTURE
All staff of the Group’s enterprises are actively engaged in the H&S management, which allows the Company to achieve a high level of health and safety in a workplace. To interact effectively with employees on health and safety, special operational safety boards have been established at the Group's operations, as required by the Labour Code of the Republic of Kazakhstan. The boards comprise representatives of the employer, employees, and technical H&S inspectors.
The boards ensure regular monitoring of compliance with H&S regulations. Inspections are carried out by technical H&S inspectors. The findings of inspections and follow-up decisions are binding on both the employer and employees of the Group's companies.
As part of the implementation of Kazatomprom’s Development Strategy 2018-2028, the Company conducted works aimed at improving the H&S system. In particular, the Company took the following actions in 2023:
- The Company got TÜV International Certification (Germany) for compliance with ISO 45001 and ISO 14001.
- Works were carried out to improve environmental and social stability in the regions of Kazatomprom operations within the framework of the ESAP Roadmap.
- Kazatomprom's H&S Improvement Plan for 2023 and Samruk-Kazyna H&S Plan for 2023 were implemented.
- H&S month campaign was held.
- Internal trainers held H&S Culture training for the Company's production personnel. 15,699 employees participated.
- Incident Investigation training was held for executives of subsidiaries and affiliates.
- The HSE Club is a forum to share information and knowledge and develop measures to improve the H&S management system at the Group companies.
All these measures in 2023 helped improve health and safety culture of the Group's employees and will help avoid incidents in the future.
To promote the safety culture and leadership among managers at all levels in the Company, Kazatomprom developed and implemented the Leadership in the H&S Culture e-course in 2020. As part of the advanced H&S training system, the Company organises special training for managers and employees of subsidiaries and affiliates to help improve their H&S competences, identify potentially dangerous situations (near-misses), unsafe acts and conditions, as well as conduct behavioural safety audits. Also, the Company organises special mandatory H&S courses.
Kazatomprom conducts HSE trainings sessions for employees on a regular basis. The courses can be divided into mandatory and optional. Training courses on compliance with the requirements of the laws of the Republic of Kazakhstan regulating H&S, radiation, nuclear safety, etc. are mandatory, while training courses on safety culture, leadership, and responsibility in HSE matters are optional. These courses are based on a review of the Company's occupational safety performance and contribute to improving safety culture and introducing best global practices.
The Group engages experts and organisations for the training process. The experts hold all necessary licenses, attestations, certificates and other permits required by the Law of the Republic of Kazakhstan On Permits and Notifications.
Knowledge tests and exams are used to control the effectiveness of the training programme and courses.
MANAGING THE HEALTH AND SAFETY OF CONTRACTORS
Kazatomprom ensures compliance with industrial safety standards by monitoring its employees and contractors. Contractors' occupational safety activities are regulated by the Standard "Unified Occupational Safety Management System", Section 10.3 "Contractor Management".
The Company's occupational safety management system covers 100% of Kazatomprom’s employees, as well as non-employees whose work and/or workplace is controlled by the Company.
In 2022, we revised the information coverage and methodology for the calculation of accident rates for employees who are not full-time employees but whose work and/or workplace is controlled by the Company, and started recording accidents among employees of the Company's contractors.
Kazatomprom sets safety standards that are binding on all contractors and suppliers of goods and services. The Company assesses contractors for their compliance with H&S requirements before signing contracts. The risk analysis and H&S training planning also take into account the accident incidence rate at contractors. The results are then to be approved by the H&S Department. The H&S Department and services conduct safety audits on a regular basis. The H&S services keep records and investigate all accidents that have occurred at contracting organisations. On a quarterly basis, the H&S services provide reports on contractors' activities to assess the H&S level. Contractors that have long-term contracts must register incidents and Near Misses. The Company organises H&S training courses for employees of contractors as well as invites authorised representatives of contractors to participate in the H&S meetings.
The Company's H&S Department carries out audits and inspections of contractors to ensure compliance with the requirements of the Company's H&S management system. The Company's contractor management system is also audited as part of a certification audit for compliance with the requirements of ISO 45001 and 14001.

NUCLEAR SAFETY
To ensure nuclear safety, the Group's enterprises handling nuclear materials monitor compliance with the respective technical regulations, instructions, rules, and nuclear safety requirements for handling nuclear materials.
The Group's enterprises that have nuclear installations include Ulba Metallurgical Plant JSC and Ulba FA LLP
Kazatomprom monitors the nuclear safety performance at nuclear-hazardous sites and conducts an inventory of nuclear materials in a timely manner to ensure the nuclear safety of the Group's companies.
In 2023, the Chief Physicist’s Services (CFS) of Ulba Metallurgical Plant JSC and Ulba FA LLP implemented the following actions:
- nuclear safety knowledge testing for specialists of the finished product warehouse, uranium production (UP), the IAEA LEU warehouse, and auxiliary services of Ulba Metallurgical Plant, as well as the employees of fuel pellets and fuel assemblies shop and the fuel assemblies shop at Ulba FA LLP;
- inspections of nuclear safety level at Ulba Metallurgical Plant JSC and Ulba FA LLP;
- emergency response training of staff and services in case of an alarm signalling about a self-sustained nuclear chain reaction in all nuclear hazardous areas of Ulba Metallurgical Plant JSC and Ulba FA LLP.
The absence of accidents and incidents throughout the reporting year proves the effectiveness of these measures.
The Committee of Atomic and Energy Supervision and Control of the Ministry of Energy of the Republic of Kazakhstan monitors the Company's compliance with its international non-proliferation obligations. No violations were detected in 2023.
Under the IAEA Safeguards Agreement between the Republic of Kazakhstan and the IAEA, additional IAEA accesses and inspections were carried out at the mines of 6 uranium production subsidiaries (Ulba Metallurgical Plant and Ulba FA LLP). The results revealed no undeclared activities and nuclear materials.
In May 2023, representatives of Nuclear Material Accounting and Control unit took part in the IAEA International Symposium on Uranium Raw Material for the Nuclear Fuel Cycle: Innovation for Sustaining Future Resources and Productions at the headquarters of International Atomic Energy Agency (IAEA) in Vienna, Austria. In September 2023, they also joined the 67th Regular Session of the IAEA General Conference at the IAEA headquarters in Vienna, Austria.
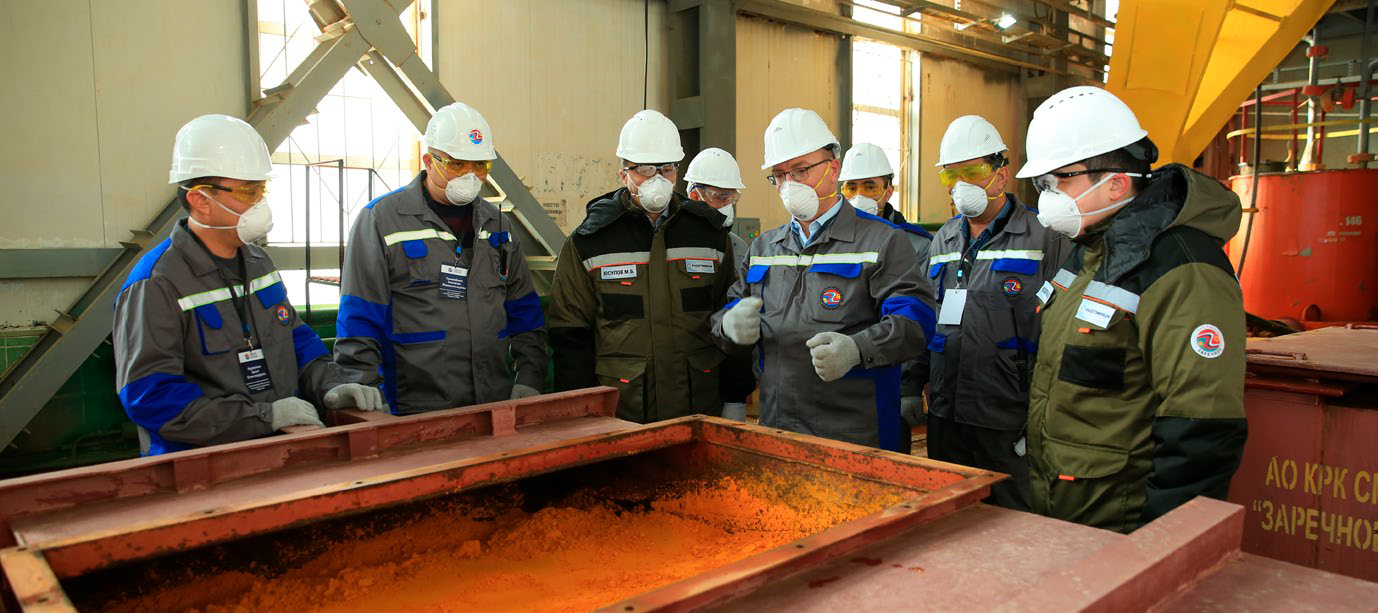
RADIATION SAFETY
КАP3
In 2022, Kazatomprom provided regular monitoring of the radiation situation at workplaces, in premises, production sites, and areas with controlled level of radiation. All radiation indicators are within standard limits and have not changed since 2022.
The average radiation exposure for staff was 1.40 mSv/ year in 2023, including natural radiation sources. The radiation from the natural background sources ranged from 0.69 to 1.22 mSv/year.
The maximum annual effective dose for personnel at the Group's enterprises was 4.86 mSv/year, which is 24.3% of the permitted dose limit, which is 20 mSv/year.
The average radiation exposure for staff of contracting organizations employed at the Group's enterprises and engaged in decontamination of overalls, cleaning of production facilities and preparation of shipping packaging kits with finished products was 0.66 mSv/ year.
To improve radiation safety and protect personnel, Kazatomprom takes the following radiation safety improvement measures:
- conducting repair works on the premises and upgrading equipment;
- upgrading and modernising technological equipment;
- removing low-level radioactive waste to disposal sites;
- repairing and purchasing radiation control equipment;
- providing radiation safety training for employees;
- conducting the certification of responsible persons by the authorised state agency responsible for the use of atomic energy.
EMERGENCY PREPAREDNESS AND RESPONSE
КАP2, SASB EM-MM-320A.1.
The Company conducts regular drills and trainings to maintain emergency preparedness among its personnel. To develop emergency skills and actions of employees, fire-fighting training courses and drills take place annually, with the safe evacuation of staff from the Company's buildings. The involvement of representatives from authorised state agencies is mandatory.
In 2023, we conducted internal fire safety audits at all Company's sites and ensured emergency preparedness among contractors.
To raise awareness among employees and minimise risks of fire, the Company held its first fire safety month.
In November 2023, a certified competent organisation conducted a scheduled inspection and evaluation of the individual fire risk of the Company's headquarters for compliance with the requirements of the Fire Safety Regulations of the Republic of Kazakhstan. The results of the inspection showed that no fire safety violations or fire hazards to people's lives were detected. The building of the Company was in compliance with the requirements of the ISO 14001:2015 and ISO 45001:2018 standards in the field of fire safety.
In 2023, 8,500 employees completed fire safety basics course. 8,000 employees participated in 411 drills, including large-scale drills with the involvement of state agencies and representatives of the Samruk- Kazyna Fund.
Human Resources Management
MANAGEMENT APPROACH
Attracting and retaining qualified personnel is one of the Company's priorities. We strive to create a work and leisure environment that meets high standards. Kazatomprom offers competitive salaries, provides opportunities for professional growth and fosters an open dialogue with employees, especially during periods of instability.
Our corporate culture focuses on mutual trust, respect, openness and integrity, as well as continuous professional development. We continuously improve our training and mentoring programmes that help employees be more successful in their work, adapt faster to the corporate environment and improve their professional skills. Kazatomprom guarantees access to educational resources for all employees, regardless of their area of expertise, place of work, and geographical location.
The Company prioritises employee well-being and satisfaction. We provide opportunities to raise questions and concerns through our confidential internal communications system.
The Company adheres to the principles of business ethics articulated in the Code of Ethics and is strictly committed to non-discrimination and nonharassment. Kazatomprom seeks to create a culture of equal opportunities and socio-cultural diversity. Our comprehensive programmes incorporate training, mentoring and active engagement within the Company.
The Company's HR management activities are regulated by Kazatomprom HR Policy 2023-2028. The document provides for the introduction of inclusion practices and diversity, creation of a psychologically safe environment and sense of belonging for all employees.
We are also governed by the Labour Laws of Kazakhstan, international standards and a set of internal documents:
- the Remuneration Policy;
- the Rules for the Selection and Recruitment of Personnel;
- the Collective Bargaining Agreement;
- the Code of Ethics and Compliance;
- the Principles of the Corporate Social Responsibility Policy.
The Board of Directors approves and monitors the achievement of strategic HR goals. The Company's HR Department and Social Work Department are responsible for the effectiveness of the HR policy, as well as day-to-day activities with personnel. HR services at the enterprise level ensure direct on-site coordination and operational management.
HEADCOUNT AND STAFF TURNOVER
At the end of 2023, Kazatomprom's average staff number (including joint ventures and associates) amounted to 21,554 people. This number does not include employees hired under independent contractor agreements and outstaffing contracts. The total headcount of the Group's personnel increased by 4% year on year compared to 2022. This is due to the increase in production volumes of certain subsidiaries and affiliates and staff recruitment for project needs. The headcount at the end of the period equals to the number of employees on the payroll of the Company's subsidiaries and affiliates as of 31 December 2023.
Kazatomprom’s total headcount, 2023, employees

We value long-term relationships with our employees. The majority are employed under long-term contracts (> 90%), with around 10% of employees employed under fixed-term contracts.
The most common type of contractual relationship among non-employees of the Company is and independent contractor agreement and an outstaffing contract. The total number of personnel who are not employees of the Company, but controlled by NAC Kazatomprom JSC is 1,010 people. Workers hired under a civil law agreement and an outstaffing agreement are hired to perform project or seasonal work. The increase in the number of personnel who are not employees of the Company in comparison with 2022 is due to an increase in project activities, as well as the need to perform one-time work.
The most common type of contractual relationship among non-employees of the Company is and independent contractor agreement and an outstaffing contract.
In 2023, the Group employed 4,386 people, of which 77% work in South Kazakhstan (including Shymkent). Kazatomprom has no policy of preferential hiring of local employees. The candidates are selected on their merits: education, qualifications, and professional qualities of applicants.
In 2023, the Group's total staff turnover was 15.8%. Compared to 2022, this indicator grew by 1%. In 2023, voluntary turnover rate was 7.9%, with the target indicator of up to 14%.
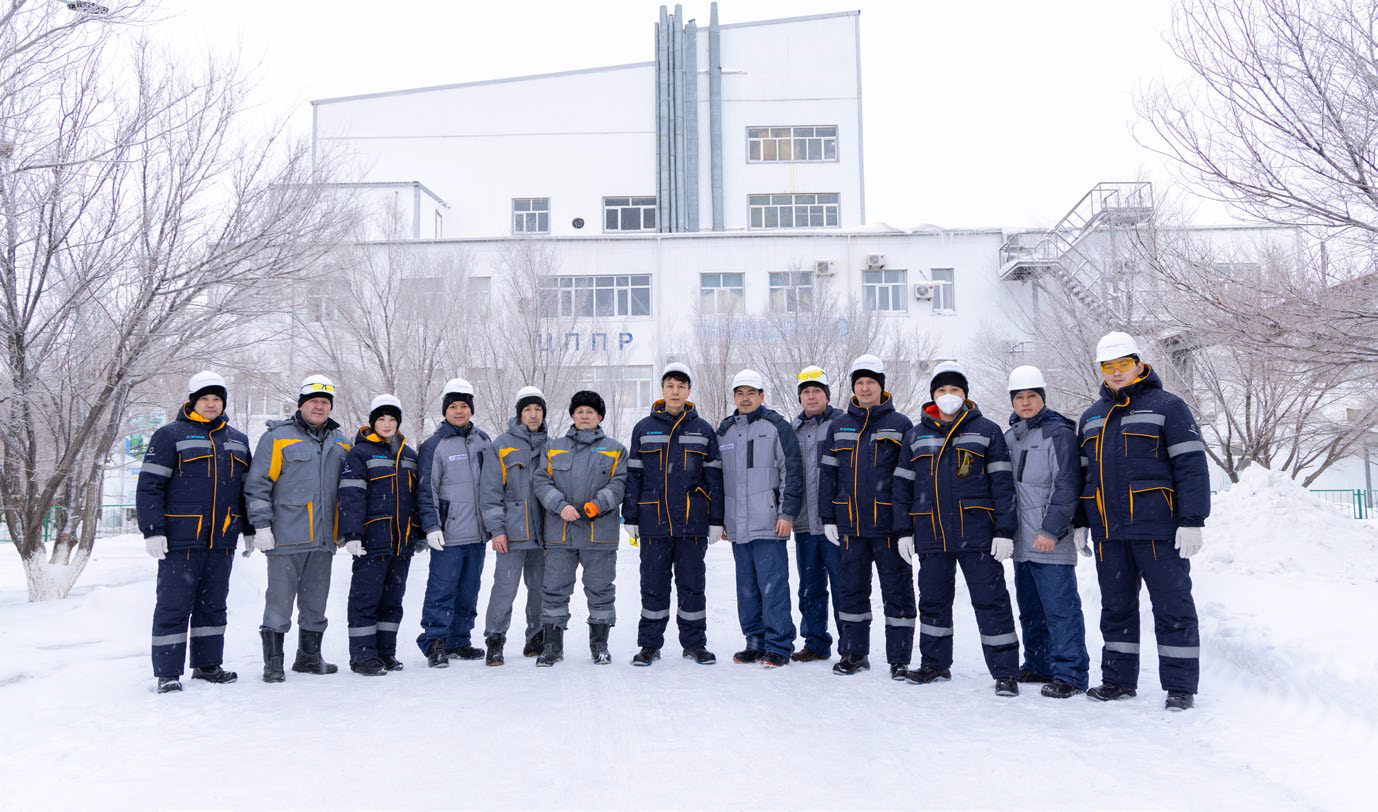
Kazatomprom’s average headcount by form of employment, 2021-2023, persons
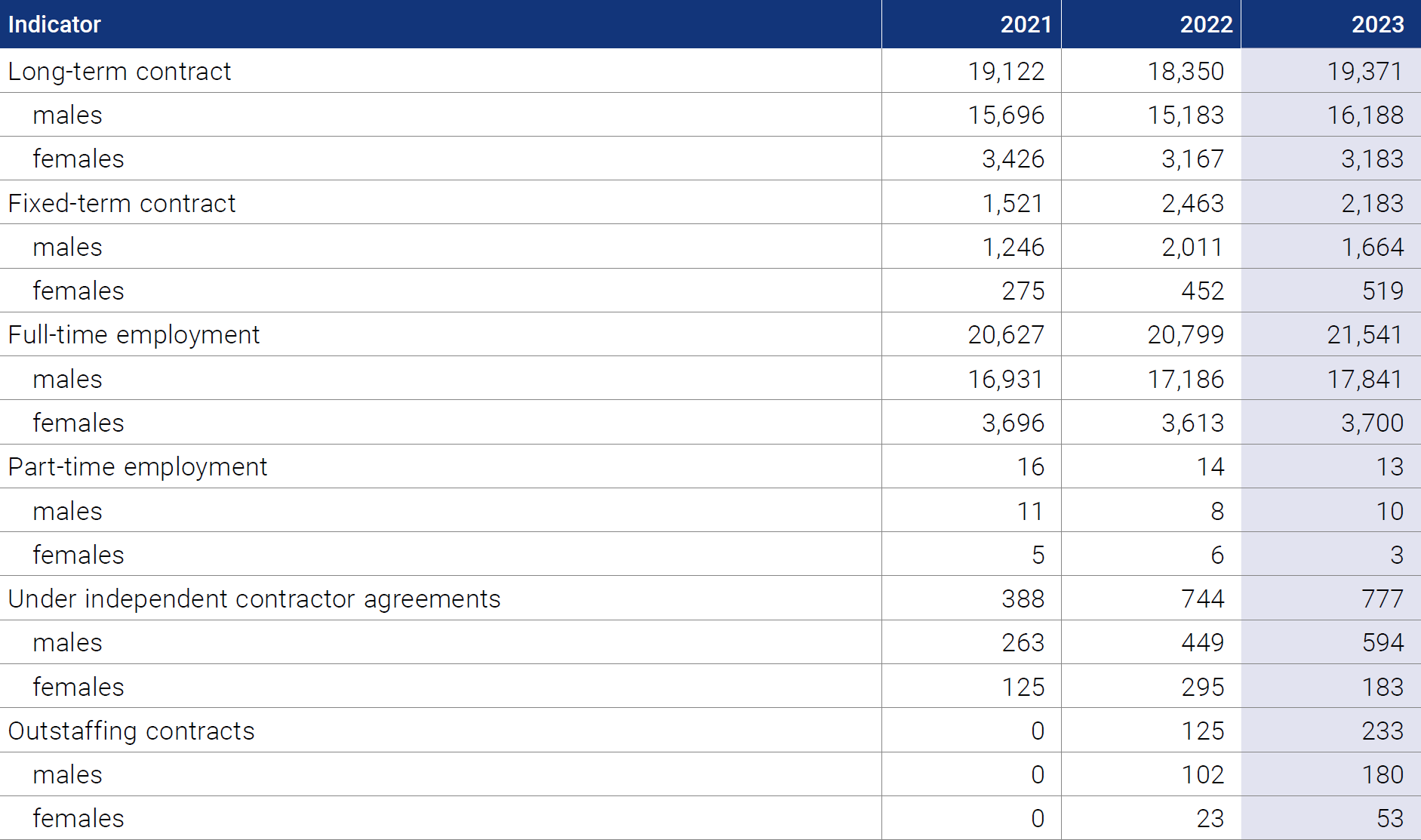
DIVERSITY AND INCLUSION
An important part of our corporate culture is ensuring inclusion and equal rights, as well as non-discrimination. We attract and develop the most talented employees, regardless of gender, nationality, age, religion, social status, physical and mental abilities, work experience and education. This approach aligns with UN SDGs 3, 4, 8, 9, 10, 11 to improve the quality of life and well-being of people of all ages, provide inclusive and equitable education, create lifelong learning opportunities, and achieve gender equality and ensuring decent working conditions for everyone without exception.
Kazatomprom recognises and values the diversity of employees' views and cultural values. The Company does not tolerate any form of discrimination, including discrimination based on race, gender, religion, disability, or political beliefs. When making job announcements and selecting candidates, experience and qualification requirements are clearly defined to eliminate any bias in the recruitment process. The remuneration depends solely on the candidate's skills and qualifications.
Kazatomprom carefully monitors possible discrimination cases through feedback channels, including the hotline, where employees can raise anonymous questions or complaints.
Inclusive environment
Kazatomprom provides jobs for people with disabilities. In 2023, the Group employed 191 persons with disabilities (including 12 people in administrative staff and 179 people in production staff), an increase of 8 persons compared to 2022. The share of employees with disabilities in 2023 was 0.8% of the average employees.
Average number of employees with disabilities, 2021-2023, persons
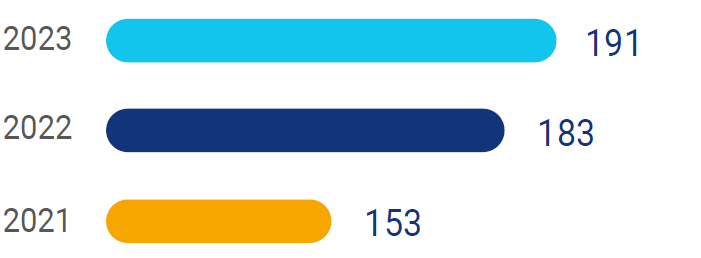
Gender breakdown
Due to the nature of the Company's production operations, the share of males in the total headcount is larger. Kazatomprom follows the principle of gender equality and engages women in administrative and technical positions. In 2023, the share of females was 17.2%.
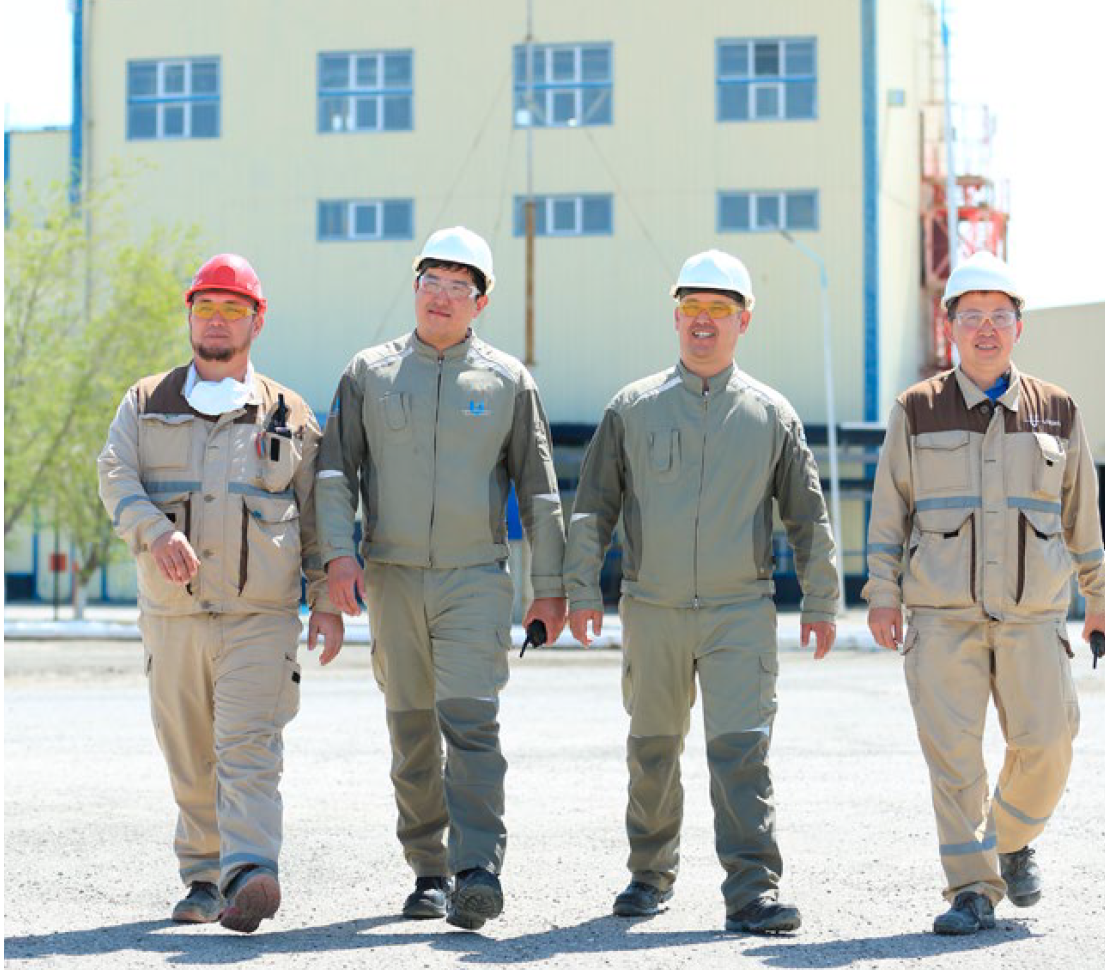
Kazatomprom’s average headcount by gender, 2021-2023, persons
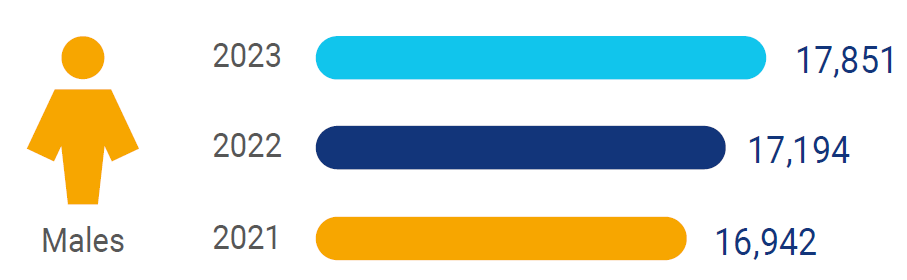
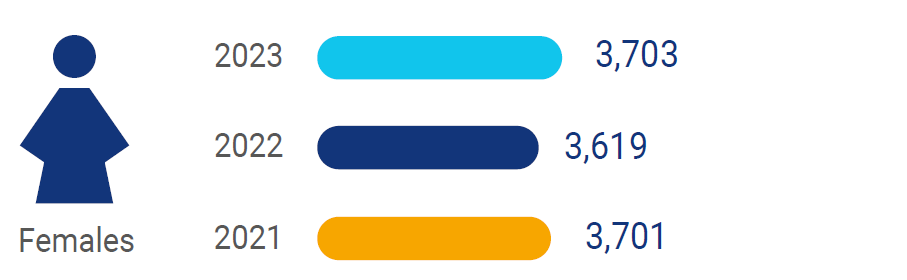
As part of promoting gender equality, developing leadership potential among females and training future female leaders, the Company plans to gradually increase the share of females in the management bodies of the Company and its affiliates and subsidiaries (boards of directors, supervisory boards and executive bodies) to at least 30% by 2030. It was 26% in late 2023.
Workforce age diversity
Kazatomprom prohibits age-based discrimination. The Company employs people of different age groups, including people over 50 years old. In 2023, this age group accounted for 27.2%. The average age of employees was 40 years.
Kazatomprom’s average headcount by age, 2021-2023, persons

MOTIVATION AND REMUNERATION
Kazatomprom seeks to ensure decent and timely pay for its employees and applies transparent approaches to material remuneration, striving to maintain wages at a high competitive level in the labour market and in the industry.
The Company has a remuneration system that complies with national legislation and defines minimum wages, working hours and overtime pay.
In accordance with the HR Management Corporate Standard of Samruk-Kazyna JSC, the reference wage market for employees of the Company's subsidiaries and affiliates is the general industrial market of the Republic of Kazakhstan, and the level of wages tends to its median.
The Model Rules for Remuneration and Approach to Remuneration of Employees of NAC Kazatomprom JSC, approved by the Company's Management Board, set the Company's procedure for remuneration. Each Group's entity further approves its own remuneration rules, taking into account the management specifics (based on the Standard Remuneration Rules). The management bodies of all Kazatomprom subsidiaries and affiliates voted unanimously in favour of adopting the remuneration rules created on the basis of the Company's Model Remuneration Rules. Third-party consultants do not participate in making decisions on remuneration of hte Company's employees.
In 2023, 15,240 people or 71% of the Company's headcount passed the official performance appraisal.
Kazatomprom pays special attention to analysing the ratio of remuneration for females and males.
Due to the industrial nature of the business, which often requires physical labour, most employees are male. Nevertheless, we do not tolerate any form of discrimination with regard to recruitment, remuneration, performance appraisal and career development for females. The ratio of basic remuneration between males and females is 1:1.
According to the Labour Code of the Republic of Kazakhstan, the remuneration system should ensure that the share of basic wages is not less than 75% of employees' wages, excluding one-time incentives. Kazatomprom has a fixed (basic) part of wages of 75% or more, and a variable part of 25% or less.
Internal Company's regulations do not set any benefits when employees are employed or dismissed.
In accordance with the Labour Code of the Republic of Kazakhstan, the employer shall make mandatory occupational pension contributions at the rate of 5% to employees defined by the list of industries, jobs, professions occupied in hazardous working environment.
Kazatomprom’s payroll fund, KZT
Average monthly wage of production personnel

Payroll fund, KZT million
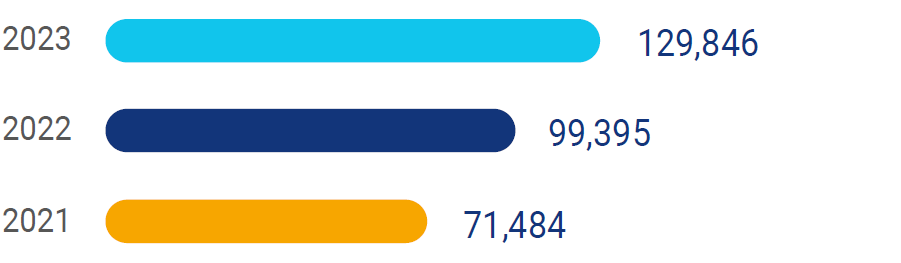
We have analysed differences in the Group's total employee remuneration. The analysis showed that in 2023, the average income of female production personnel was 8% lower than that of males, while the pay gap for males and females in the Group was 6% in favour of females.
Long-term and short-term staff motivation
The rewards paid to employees for meeting planned targets, and strategic and operational goals of the Group, as well as for suggesting innovative ideas, high professionalism, and a responsible attitude to work are the key components of the financial incentives system, which fuels motivation of personnel.
Additional incentives include:
- financial assistance for annual leave to support the health of personnel;
- additional payments for concurrent employment and mentoring allowances set by the Group’s management;
- additional payments to employees living in an environmental disaster zone, depending on the region of residence, in accordance with Kazakh law;
- additional payments to production staff if they work in harmful or dangerous working conditions as prescribed by the laws of the Republic of Kazakhstan.
STAFF DEVELOPMENT AND TRAINING
Staff training and development is one of the key Company's priorities under the Corporate Culture Transformation and Development Programme. Kazatomprom proactively implements the best and most effective educational practices in the areas of operational efficiency, occupational safety, human rights, labour protection and career guidance. The Company runs programmes to develop leadership competencies and trains mentors and internal coaches. Annually, employees of the Company's enterprises undergo compulsory and professional training.
Education level of Kazatomprom’s personnel, 2021-2023, %
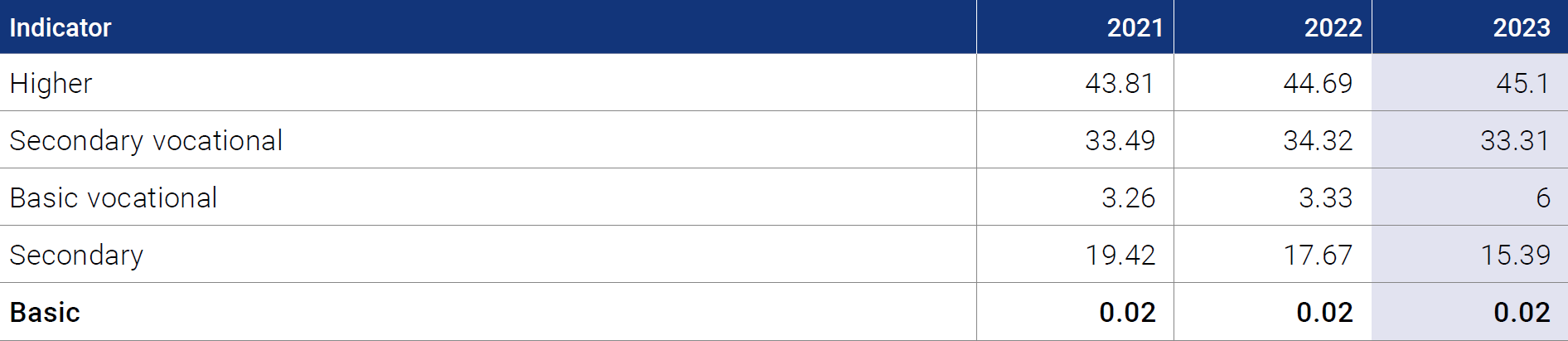
The Company has a Comprehensive Training Programme 2019-2023, which is aimed at systematising the processes of training, retraining and advanced training of employees. The Programme includes such elements as:
- training at universities and colleges;
- advanced training;
- retention and transfer of knowledge.
The training is conducted on the site of Kazakhstan Nuclear University with the involvement of internal experts and external providers.
Kazatomprom invests a significant number of resources in the training and development of its personnel. In 2023, Kazatomprom invested KZT 2.9 million in employee advanced training.

Training is based on the principle of selflearning, according to which 70% of training takes place at work, 20% of skills are acquired by employees through mentoring and coaching programmes, and 10% through training courses and other educational programmes.
The HR Department is responsible for supporting managers in training employees, organising the training process and choosing educational programmes, as well as educational service providers.
In 2023, the Company continued the implementation of the Talimger Project, which aims to develop a mentoring culture, within the framework of 3 projects proposed by employees of subsidiaries and affiliates. The projects are: Automated Calculation of Mining and Development Operations Repayment (JV Akbastau JSC), Gaining Business Negotiation Skills. Effective Presentation. Independent and Responsible Decisions when Working with Customers (Volkovgeologia JSC), and Optimising Performance of Submersible Pumps. Frequency Converter Automation (Baiken-U LLP).
Kazatomprom also develops mentoring through various programmes and areas. The Izbasar programme has a standing pool of engaged mentors. As part of a subsequent rotation, new mentors are also welcome. The Company and its subsidiaries and affiliates have an established mentorship system for young professionals, trainees and interns.
TRAINING EFFECTIVENESS EVALUATION
Kazatomprom has introduced a procedure for evaluating the professional, personal, and business as well as managerial qualities of employees by analysing their common and individual performance. The evaluation and analysis procedure determines the training needs of employees and their future career opportunities. Based on the analysis, we draw up a development plan or corrective measures for the employee, change the remuneration, and promote/demote the employee
Upon completion of training, an assessment of the completed training is carried out by filling out questionnaires by the trainees. After 3 months, the assessment of the completed training is done by the head of the trained employee.
TRAINING PROGRAMMES
The Company pays close attention to improving the practical and professional skills of employees due to the constantly tightening requirements for their qualifications. Kazatomprom develops and implements advanced training programmes in various professional areas, including mandatory training in accordance with the legislation of the Republic of Kazakhstan.
All training programmes of the Company are aimed at improving managerial and personal and business competencies of managers, talents (successors), forming effective management teams, unlocking internal potential, improving cross-functional interaction, as well as applying the acquired skills in the working environment and achieving better results.
In 2023, the Company continued its Leadership Development Programme.
Kazakh and international service providers with experience in leadership development, management competencies, as well as tools to measure compliance with the ESG principles, and team management were engaged.
The training programmes were aimed at improving the managerial and personal and business skills of managers and their successors, forming effective management teams, developing internal potential, improving cross-functional interaction, as well as applying the acquired skills in the working environment and achieving better results.
In 2023, managers at all levels attended a number of training events based on their development areas. Each training sought to develop Kazatomprom's corporate competencies and values.
In 2023, the Company held about 18 workshops, training and strategy sessions, covering 100% of managers at CEO-1 and CEO-2 levels.
In 2023, in partnership with ALMAU University, the Company approved and launched the Development Programme for Directors of Departments. The programme comprised 5 modules on soft skills development. Managers who completed all modules of the programme received diplomas from the University.
In August 2023, Kazatomprom launched the Mine Director Development Programme and the Club of Heads of Production Facilities. The Mine Director Development Programme focuses on the following three levels: enhancing basic management competencies and skills; deep understanding of communication processes; self-management through mindset expansion, energy management, and gaining resilience in tense conflict situations.
256 persons have completed the Programme. The total number of training hours reached 12,515 hours.
In 2023, Company's employees traditionally held 15 master classes. Master classes were recorded, posted on the Group’s corporate portal, and are currently available to all employees. Such a format provides for the use of videos as additional training materials featuring unique knowledge and best practices.
TALENT POOL
In 2012, the Company introduced a management succession programme for Kazatomprom, aimed at identifying candidates from among the Group's employees with high potential and a desire to improve their professional qualities and career growth to ensure continuity in the Company's management system.
During the programme, a mentor is assigned to every successor, who is responsible for employee development, progress monitoring and support in the course of the implementation of their ideas. The pool of successors is defined based on the results of employee performance appraisal. Pool owners – the Chairman of the Management Board and functional area managers – are the main contributors to the development of the succession programme.
In 2023, 7 successors from among the management and functional pools of successors were appointed, which accounts for 47% of the total number of appointments to key positions. To ensure effective mentor sessions with successors, mentors were trained and learnt feedback skills.
On an annual basis, the headquarters review the number of appointments to positions from the successor pool.
COOPERATION WITH EDUCATIONAL INSTITUTIONS
The Company and its subsidiaries and affiliates prioritise their contribution to the development of future skilled personnel, as well as education through training at universities and colleges. Kazatomprom cooperates with Kazakh universities and colleges, as well as foreign educational institutions, in the nuclear industry specialities.
Such universities and colleges include: Kazakh National Research Technical University named after K.I. Satpayev, East Kazakhstan Technical University named after D. Serikbayev, South Kazakhstan University named after M. Auezov, Karaganda State University, Ust- Kamenogorsk Multidisciplinary Technological College, South Kazakhstan Polytechnic College, Geological Exploration College and others. The Company also cooperates with Russian universities: National Research Tomsk Polytechnic University (TPU), National Research Nuclear University MEPhI (MEPhI), and others.
The Group's employees are trained at the expense of the Company. Individuals who are not employed with Kazatomprom and its subsidiaries and affiliates are trained at the expense of subsoil users. As of the end of 2023, 632 people were enrolled in industryspecific specialties, of which 95 were employees of Kazatomprom, its subsidiaries and affiliates, and 537 individuals were not employed by Kazatomprom. In 2023, the Company spent KZT 484,284.9 million on training specialists in universities and colleges, of which KZT 329,060.1 allocated for training individuals not employed by the Company and its subsidiaries and affiliates.
In 2023, 236 students of technical specialities from Satbayev University, from among the socially vulnerable population, received funding in the total amount of KZT 283,166.9 under the licence and contract terms of the Company's subsidiaries, as part of annual total expenses and cooperation with Satbayev University.
In 2023, Kazatomprom launched one of the major social projects, Murager, designed to provide academic grants. The programme focuses on supporting university applicants, college graduates and entry-level students from local communities where the Company operates. Kazatomprom's goal is to contribute to the development of the regions and increase the level of education of the local population, promote technical specialties with further employment opportunities at the company's enterprises.
Programme participants are eligible to receive a 1-year tuition-free academic grant to study priority technical specialties in Kazakh technical colleges and universities. Upon successful completion of the first year, the grant is extended for the next academic year. The academic grant competition is also open to socially vulnerable groups. 34 academic grants for a total of KZT 14.5 million were awarded under the programme.
STAFF WELFARE
Kazatomprom fosters social support measures aimed at continuously improving working conditions and the quality of life for its personnel regardless of the form of employment. Social policy is one of the key pillars of Kazatomprom’s stable operation and sustainable development. The Company ensures a comfortable working environment and provides additional guarantees and benefits that provide high social protection for employees. These initiatives are aimed at improving the quality of life of employees. The Company implements a set of measures as part of its corporate well-being programme, aimed at ensuring social stability, creating a favourable moral and psychological environment within teams, improving social and labour conditions, and enhancing safety.
The core principles of Company's social policy comprise:
- taking care of employees – physical, financial, mental and social welfare;
- improving working conditions – improving the working environment and the production process;
- ensuring comfortable social and living conditions of employees aimed at health care and safety of workers;
- enhancing staff motivation and creating a favourable psychological climate in the team: recognition programmes (corporate awards, professional skills competitions, “Best Employee of the Year” for employees of the headquarters, and “Zhyly Kyzmetkeri” aimed at raising the prestige of bluecollar jobs and engineers), financial support for employees with many children, development programmes and much more.
The country’s leading industrial company continuously improves its approaches to social security and HR management policies.
Kazatomprom's social support costs by area, 2023, KZT bn

In 2023, the Company organised a number of events aimed at self-fulfilment in social functions and supporting the social welfare of employees: Kazatomprom Marathon, Spartakiada, In the Rhythm of a Healthy Heart, Donor Day, eco projects, social volunteering projects, and corporate events and contests.
Social programmes were launched aiming at ensuring financial welfare, particularly, improving employees' financial literacy and knowledge leading to smart financial decisions. The Company carries out activities aimed at increasing employees' knowledge of personal finance management and financial instruments. One of the subsidiaries has introduced a concessional lending programme as part of a pilot project.
EMPLOYEE SUPPORT
Company’s Collective Bargaining Agreement focuses on support to certain categories of employees: single parents, families with many children, parents of children with disabilities, and non-working pensioners upon retirement. The Group companies have a unified approach to full-time and part-time employees.
As part of social security, single parents and mothers of three or more children under 12 are granted additional leave. Families with many children and families with disabled children under 18 receive financial assistance.
In 2023, maternity/paternity leave was granted to 347 employees, where 64 are men and 283 are women.
The Company provides medical care and additional financial assistance on special occasions and holidays for non-working pensioners, upon termination of employment due to retirement or disability.
HEALTH CARE AND WELFARE OF EMPLOYEES
One of the key Kazatomprom priorities is the health and welfare of its employees. The Company has elaborated and implemented various programmes aimed at supporting physical and mental health, as well as improving the financial, social, and professional welfare of employees.
Kazatomprom strives to help each employee develop his or her own conscious attitude to the well-being and acquire the skills necessary to lead a healthy and happy life both at and out of work.
The Company works consistently to improve physical welfare and form healthy habits to enhance the quality of life, improve health and increase productivity.
In 2023, the Company approved72 one corporate program Health Protection 360° for 2023-2027. The Programme aims to improve the health of employees as the basis of corporate social culture to ensure sustainable economic activities of NAC Kazatomprom JSC in the long term.
72 Approved by the Board of NAC Kazatomprom JSC on 08 June 2023.
The Programme is implemented by means of the following tasks:
- improving disease prevention and management;
- building employees' commitment to a healthy lifestyle;
- improving the efficiency of the available resources used.
Programmes implemented in 2023:
- voluntary health insurance for employees and family members. 1.17 billion tenge was allocated to finance voluntary health insurance programs;
- surveys of satisfaction with the quality of services provided within the framework of voluntary health insurance were conducted during the year;
- mandatory annual preventive medical examination with an extended screening programme;
- technical equipment for automation of medical check-ups. All mining enterprises have an electronic system of pre-shift medical check-ups;
- first aid trainings for personnel of hazardous production facilities;
- specific prevention of acute respiratory viral infections during the season epidemic;
- establishment and development of a medical community to achieve the objectives of health protection and occupational medicine. During 14 working meetings, the group addressed 36 important issues on health protection and occupational medicine;
- community health awareness campaign on the Telegram channel with posters about healthy habits, compulsory social health insurance and voluntary health insurance, specific prevention, flu vaccination, prevention of heat-related problems, healthy lifestyle and sports;
- campaign "In the Rhythm of a Healthy Heart", Healthy Days with device tests, webinar on managing the biological age of the heart.
TRADE UNIONS AND HUMAN RIGHTS
Kazatomprom adheres to the policy that does not restrict the employees’ rights to join public organisations that represent their interests. The Group’s staff can engage in any social, political, educational or charitable activity, as long as this engagement does not affect the performance of official duties and does not harm society.
Nuclear Industry Workers Trade Union ensures Kazatomprom's reliable partnership in complying with labour legislation and actively participates in protecting the interests of employees. As of the end of 2023, 13,347 employees of the Group's enterprises are members of the Trade Union, a 1% decrease compared to 2022.
Collective bargaining agreements are concluded to regulate labour relations and ensure social protection of employees. As part of collective bargaining agreements and fulfilment of commitments, the Trade Union is allocated funds on an annual basis for events among the Company's employees, medical care, social assistance, cultural, sports and recreational activities and the purchase of vouchers for sanatoriums and children's camps.
Trade union support costs, KZT million
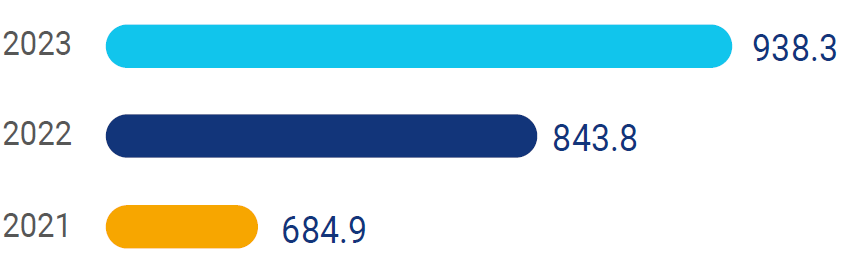
COLLECTIVE BARGAINING AGREEMENT
The Collective Bargaining Agreement is key to protecting labour rights, economic, and social guarantees of employees, as well as regulating labour relations and effective dialogue between the Company and employees. The Collective Bargaining Agreement is developed for a three-year period and is subject to regular updates.
94% of Kazatomprom employees signed collective bargaining agreements, which demonstrates the broad coverage in the organisation.
An important element of the Collective Bargaining Agreement of Kazatomprom is the obligation to notify employees in advance about significant changes in working conditions no later than one month prior to the proposed changes and in some cases fifteen calendar days.
The provisions of the Collective Bargaining Agreement also regulate recruitment, maintenance of corporate culture and relations with employees. In accordance with the Collective Bargaining Agreements, Kazatomprom provides social support for personnel aimed at continuous improvement of working conditions and the quality of life of employees.
APPROACH TO HUMAN RIGHTS OBSERVANCE
Human rights protection, social partnership, mutual respect, mutual trust, and prevention of any discrimination are the main principles in relations between the Company and its employees.
Responsibility for managing issues relating to the Company's Human Rights Policy rests with the Office of Ombudsman and Compliance Service.
Kazatomprom's corporate practices are based on recognised international human rights standards and initiatives:
- the Universal Declaration of Human Rights;
- the International Covenant on Civil and Political Rights;
- the International Covenant on Economic, Social and Cultural Rights;
- the UN Guiding Principles on Business and Human Rights;
- the ILO Declaration on Fundamental Principles and Rights at Work;
- the UN Declaration on the Rights of Indigenous Peoples;
- the UN Voluntary Principles on Security and Human Rights;
- the UN Global Compact.
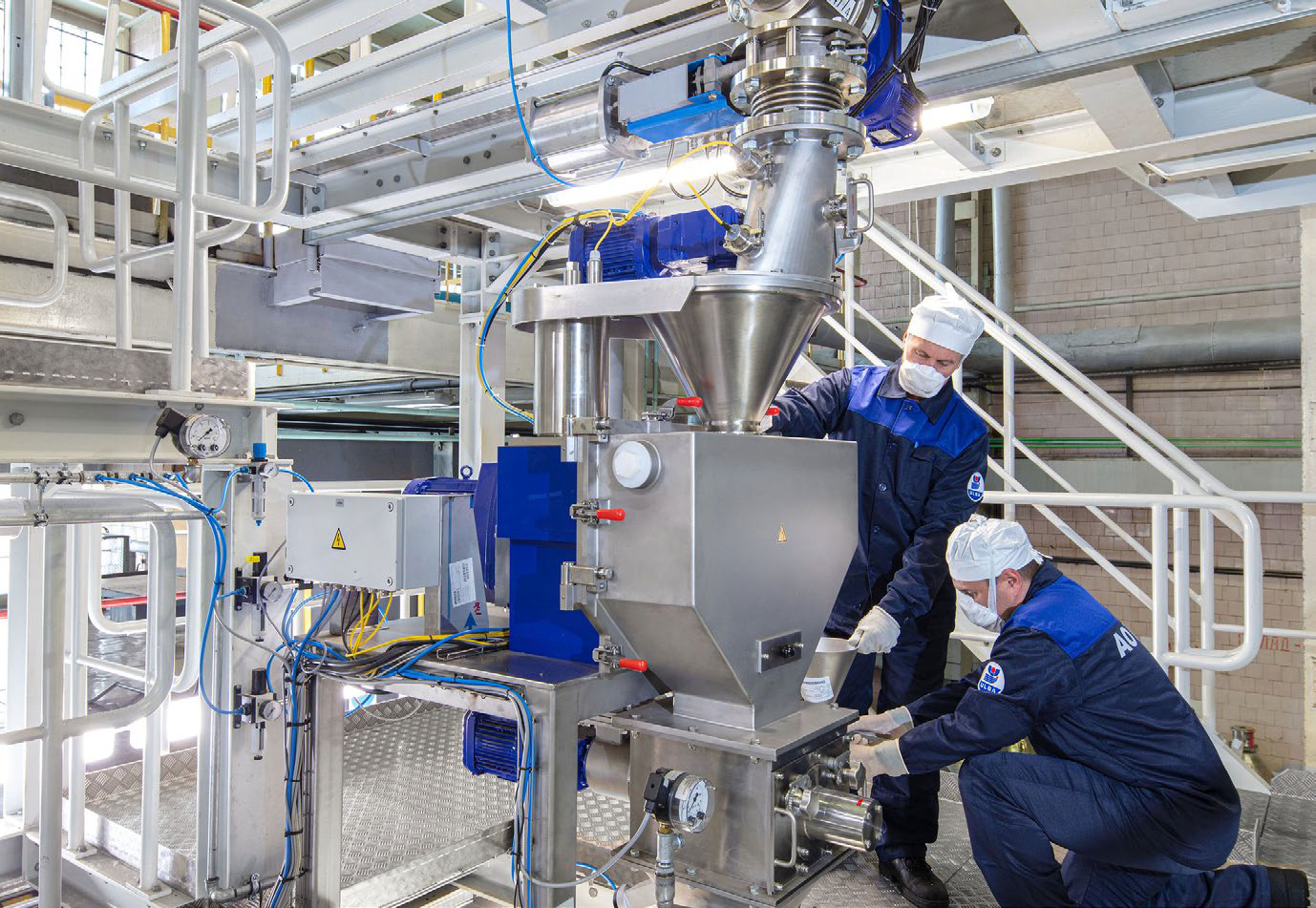
To consolidate and enforce our commitment, Kazatomprom developed and approved the Human Rights Policy in 202273. The Policy applies to all divisions of the Company and is binding on all employees of the Company. The Company's subsidiaries, affiliates and jointly controlled entities are recommended to develop and approve a similar internal document in accordance with the established procedure. The document was developed based on international human rights standards (the Universal Declaration of Human Rights, the UN Global Compact Principles, etc.) and includes the most material human rights issues, as well as issues on diagnosing the moral and ethical environment in the team.
73 Approved by the Board of Directors of NAC Kazatomprom JSC on 16 June 2022.
The Human Rights Policy is published on the corporate website and internal resources of the Company and is accessible to a wide range of stakeholders. In addition, employees of the Holding were introduced to the provisions of this document during sustainability development workshops.
Relying on the principles of respect for human rights, Kazatomprom engages those partners and counterparties that comply with the law and the Group's standards of corporate and business ethics. The Company maintains long-term partnerships only with suppliers who share and comply with the Group's ethical principles, do not tolerate corruption, respect human rights, and care about occupational health and safety. Kazatomprom is strongly opposed to the use of child labour.
In 2023, no cases of discrimination or other human rights violations were recorded in the Company. There are also no cases of forced or compulsory labour or violations of the rights of indigenous and minority peoples.
Kazatomprom requires compliance with the law and its own corporate standards on occupational safety from its suppliers and contractors. All agreements and contracts of NAC Kazatomprom JSC include provisions on the observance of human rights in accordance with the Company's Code of Suppliers and Contractors.
Kazatomprom has an Ombudsman Service ensuring:
- monitoring of human rights compliance within the Company;
- employees’ awareness and comprehension of the Code of Ethics and Compliance;
- individual meetings with employees at the enterprises regarding personal matters.
Compliance with human rights and international human rights standards is also monitored by the Company's Compliance Service and trade union organisation. In the event of a rights violation, employees may contact the Company through all feedback channels.
CORPORATE CULTURE AND INTERNAL COMMUNICATIONS
Production efficiency and achievement of the Company's strategic development goals are due to the Company's focus on the formation of a strong corporate culture. Core values such as safety, responsibility, professionalism, development and teamwork are actively promoted within the team.
All Company employees understand and share the corporate values, define themselves as part of the team and contribute personally to the common cause.
An important element of the corporate culture, aimed at maintaining the Company's corporate values, is social volunteering, which brings employees together and promotes staff involvement in the formation of a positive internal atmosphere and the image of Kazatomprom as a socially responsible Company.
In 2023, employees of the Company and subsidiaries and affiliates continued implementing large-scale volunteering projects. They are aimed at support for vulnerable groups and veterans, education of high school students located in the regions where the Company operates, and environmental campaigns.
Internal communication plays an important role in the development of corporate culture, aimed at organising effective interaction between employees, resolving conflicts, and building employee commitment and loyalty. Corporate internal portal and corporate media such as the daily digest, the company newsletter, and the QazAtomNews corporate magazine are used as information channels.
To develop effective communications, in 2023, the Company launched a messenger with more than 4,000 subscribers from among the Company's employees. The Telegram channel serves as a first-hand information source for employees.
EVENTS FOR EMPLOYEES
Kazatomprom is interested not only in the professional development of employees but also in the realisation of their personal potential. Corporate sports and cultural events help to increase the activity, motivation and involvement of employees in Company's life.
In 2023, Kazatomprom held large-scale corporate events to showcase the Company's achievements and strengthen corporate spirit:
- Women's Leadership Week.
- National sports competitions – Nomad time Kazatomprom.
- Young Professionals Forum and Hackathon.
- Extended Town Hall "Sustainable Development of the Uranium Mining Industry of Kazakhstan" XXII Sports and Athletic Competition among enterprises in the industry.
- Kazatomprom Marathon.
- Kazatomprom’s wits and humour competition.
To support employees' families, the Company organised special events such as "Shine Talent – Kids" and a summer educational camp for children of employees of subsidiaries and affiliates.
To provide social support to employees' families and increase children's interest in the nuclear industry, the IQanat High School of Burabay hosted an educational summer camp for 100 highschool children of employees of subsidiaries and affiliates from 17 to 28 July 2023.
The Company received 490 applications. To ensure transparent selection, a proctoring online test was held. The test comprised 45 questions on the history of Kazakhstan, mathematics, geography, English and Kazatomprom's activities. 100 applicants who scored the best results were enrolled in the programme.
During 10 days, the children were trained not only in languages, programming, financial literacy, mobilography and SMM, but also in leadership skills. The camp also held career guidance sessions.
Upon project completion, programme participants and their parents shared positive feedback.
INTERNAL COMMUNICATIONS AND INTERACTION
The Company has an effective system of internal communications, which ensures several feedback channels.
The main channel of communication is the Company's Internet resource, kazatomprom.kz. The website provides external stakeholders with the opportunity to leave a written inquiry or complaint and, if necessary, to contact the hotline by phone.
The Company supports the development of a feedback culture by:
- conducting feedback surveys;
- conducting exit interviews;
- developing a corporate portal.
The Group’s enterprises monitor and analyse inquiries, providing quarterly reports to Kazatomprom's headquarters. Based on the analysis results for each inquiry, we follow up on the elimination of violations and make appropriate recommendations.
Kazatomprom's internal communications system is the main tool to ensure that employees are timely informed about current events in the Group and helps maintain a positive atmosphere in the team.
The Company uses an online and offline format to hold major organisational events for employees (meetings, management meetings with the team, and teambuilding events).
There is a functioning Kazatomprom RHYTHM programme, which informs employees about the Company's projects.
Employee awareness of the current situation and important events for the industry is maintained via e-mail – regular newsletters and addresses on behalf of management, as well as the corporate QazAtomNews e-magazine.
EMPLOYEE SATISFACTION AND ENGAGEMENT
Kazatomprom's programmes and initiatives dedicated to corporate culture development, improvement of social and labour conditions, safety improvement, material remuneration, motivation and engagement of employees are implemented in accordance with the developed plans and supported by all employees of the Company.
The annual positive performance appraisals are confirmed by regular surveys on the level of social stability. In 2023, the Centre for Social Interaction and Communications (PE) conducted research to determine the level of social stability “Samruk Research Service” (SRS) at 21 enterprises of Kazatomprom Group. The SRS is determined based on employee appraisals and their perception of the index components. The SRS includes three components:
- Engagement Rate: the level of satisfaction with working conditions and occupational safety, relationships and communications in the Company, and the level of employee loyalty.
- Social Wellbeing Rate: captures employee sentiment, determined by external factors and the social environment.
- Social Tranquility Rate: reflects the level of social tension in the team, assessment of the potential for protest and the motives of hypothetical readiness for protests.
According to 2023 survey results, the Group's social stability level reached 74%, favourable level. Compared to the 2022 results, the level of social stability has decreased by 2%. Compared to the results of the first half of 2023, has improved by 4%. As part of this research, the engagement rate is also determined, which amounted to 84% (favourable level).
In order to take a systematic approach to development issues and improve the level of social stability, Kazatomprom implements a set of measures which contribute to improving the level of social stability, prevention of labour conflicts and protest sentiments.
Based on the effectively implemented measures, confirmed by Samruk Research Service survey results, during 2024 the Company will continue to implement systematic measures to develop corporate culture, and improve social and labour conditions, safety, material remuneration, motivation and personnel engagement. Kazatomprom aims to ensure a favourable level of social stability and employee engagement, but not below 70%.
PLANS FOR 2024 AND A SHORT TERM
In 2024, we will continue employee support programmes, maintain and develop HR potential and maintain the level of employee engagement, including through measures to develop the employer brand.
The Company plans to continue efforts to improve the efficiency of the remuneration and financial incentives system, automate HR management processes, implement management succession and leadership development programmes, streamline remuneration, and take measures seeking to improve working conditions.
In accordance with the Company's priorities, we are set to deepen cooperation with trade unions representing the social partnership, amend collective bargaining agreements, maintain social stability, develop a culture of negotiation, and improve internal communications.
To increase employee satisfaction, the Company aims to improve social and living conditions in 2024 in accordance with the Corporate Standard of Industrial Relations of Samruk-Kazyna JSC and legal entities where 50+ percent of voting shares (equity interests) are directly or indirectly owned by Samruk-Kazyna JSC.
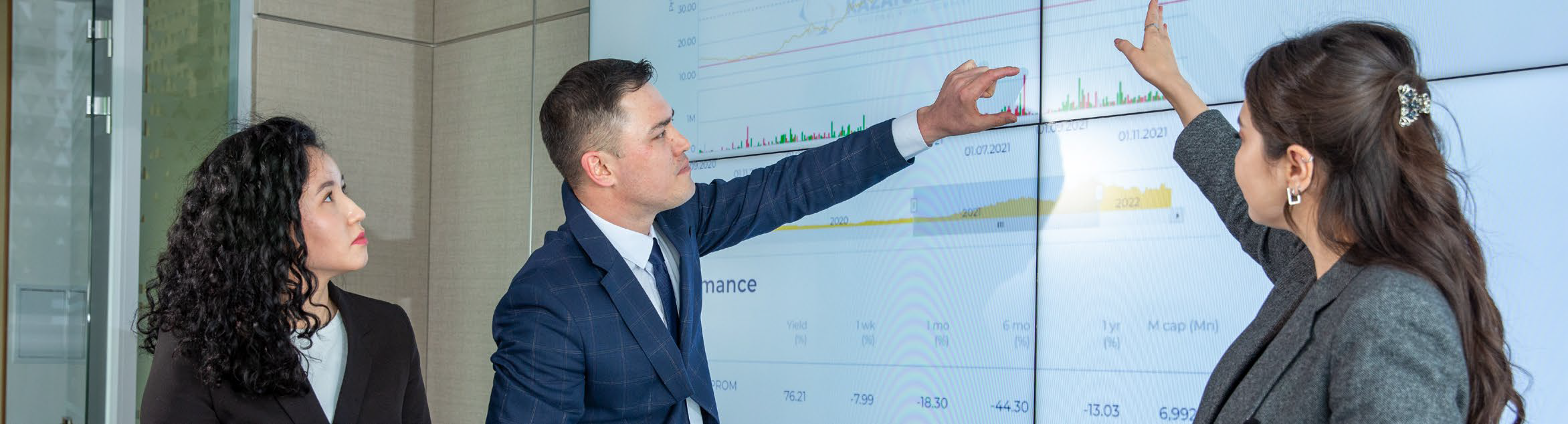
Support for Local Communities
MANAGEMENT APPROACH
The Company's main social commitment is to support and develop the regions where it operates. Kazatomprom creates jobs, pays taxes and operates social and economic partnerships in local communities. The Company's stakeholder engagement helps maintain a strong public image.
Kazatomprom's social programmes are aimed at tackling current social problems, improving the living standards of the local communities and bolstering economic growth. The Group is committed to the principle of social investment transparency and liaises with stakeholders at all stages of the Company's projects.
Chief HR and Occupational Safety Officer is responsible for the external social policy and interaction with local communities.
In 2022, the Company consistently implemented measures aimed at ensuring long-term productive relations with the regions where it operates and strengthening its image as a socially responsible business.
Kazatomprom makes a significant contribution to the well-being and socio-economic development of the regions of operations by:
- generating significant tax revenues for regional budgets;
- making payments to regional budgets under subsoil use contracts;
- providing jobs to the local population.

Key indicators of Kazatomprom's economic contribution to the development of regions of operations
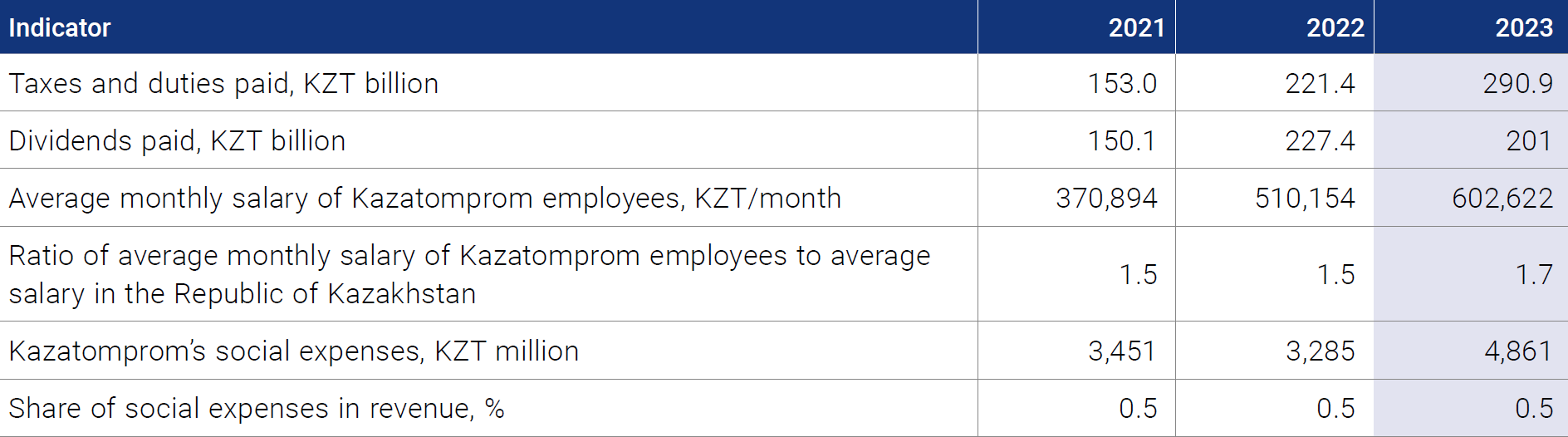
SPONSORSHIP AND PHILANTHROPY
To support local communities, subsidiaries and affiliates can implement philanthropic initiatives independently. Subsidiaries and affiliates widely participate in charity events and cultural activities in the regions where they operate. In particular, they help children from orphanages and large families and provide support to improve local public services and public amenities. They also participate in environmental campaigns, clean-ups, public events, and festivities.
In addition, subsidiaries and affiliates implement community development programmes as part of the Company's philanthropic and sponsorship activities. These programmes are based on the requests of the local communities and vulnerable groups, through the engagement of the Akimats, the Council of Elders, if any, and volunteers. The Company operates a hotline that receives queries, including requests from external stakeholders.
SOCIAL INVESTMENTS
The Company's enterprises annually implement socially significant projects aimed at the socio-economic and infrastructural development of the regions where the Company operates, including improving the quality of life of employees of Kazatomprom, as well as their family members.
In 2023, the Company launched a number of socially significant projects, including financial support for the construction of a culture and recreation centre, construction of children's playgrounds and sports grounds, purchase of educational equipment, improvement of settlements, financial assistance to socially vulnerable groups by purchasing coal, food, school supplies, New Year gifts, and other socially significant initiatives.
Investment in external social programmes, 2022, KZT million
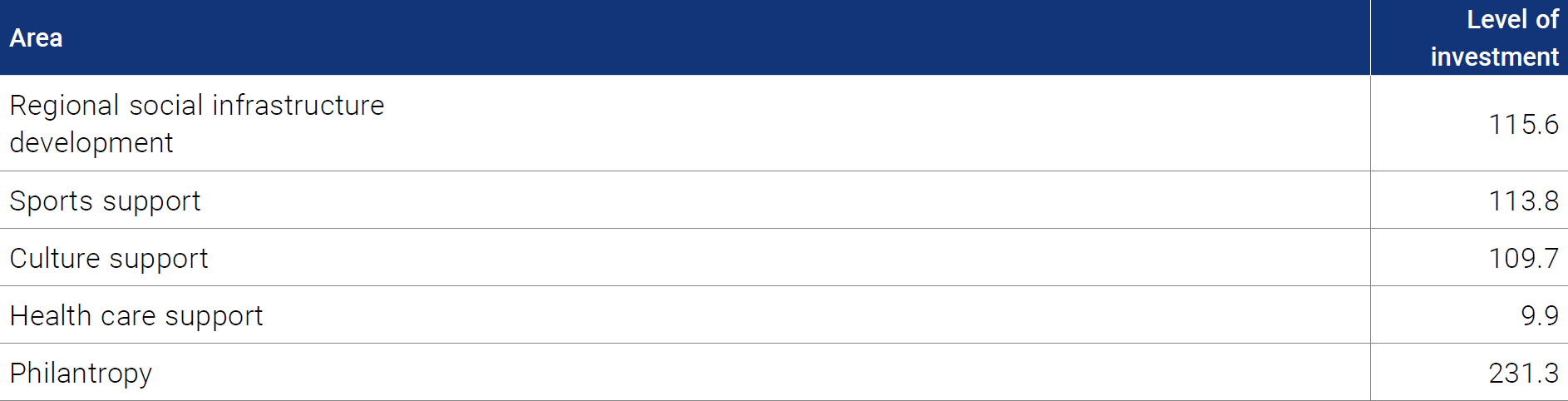
Social infrastructure development
Identification of key problems in the regions of operation and assistance in their solution and the development of social infrastructure are also among the priorities of Kazatomprom's external social strategy.
Throughout 2023, JV Katco LLP, ME ORTALYK LLP, and Kazatomprom-SaUran LLP implemented projects to improve street lighting, pedestrian paths roads, landscaping and repair of alleys in the settlements in the Sozak district of Turkestan Region. A total of KZT 115.6 million was channelled into these projects.
Education support
In 2023, the Company organised SANA Leadership Development Information Camp for high school students in the regions of Kazatomprom's operations. The camp seeks to develop personal competencies, leadership skills, and emotional intelligence through training and awareness-raising activities as part of the students' career guidance. It promotes technical professions in production areas and builds confidence in Kazatomprom's HR brand among local residents.
In 2023, the camp took place in the settlements of Sholakorgan, Kyzymshek, Tasty settlements in Turkestan Region, and in Shieli settlement of Kyzylorda Region. The project covered 440 pupils from:
- Nazir Torekulov IT School-Lyceum.
- Lande Bokenov School.
- Abay Secondary School.
- Sh. Ualikhanov School-Lyceum No.127.
- School Gymnasium №45 "AK Orda".
Health care projects
The initiatives seek to support and improve healthcare institutions, as well as medical check-ups of children suffering from nervous disorders.
JV Katko LLP sponsored a project to renovate a health care centre in the Shu settlement of Turkestan region.
Sports support
The Company's enterprises seek to support the development of sport as an important area of social projects. JV KATCO LLP and Baiken-U LLP allocated KZT 113.8 million for the construction of sports and playgrounds, a basketball court and a street workout area, as well as organisation of a chess school in the regions where the Company operates.
Culture support
The culture support projects cover settlements in Kyzylorda and Turkestan Regions. Baiken-U LLP supported the construction of Khorsan Ata local history museum in the Zhanakorgan District of Kyzylorda Region. As part of contractual obligations for subsoil use, JV Budenovskoye LLP targeted financial assistance for the construction of a 75-seat culture and recreation centre in the Sozak District of Turkestan Region. We spent a total of KZT 109.7 million on this area.
Philanthropy
The Company provides targeted assistance to those in need, supports socially important projects and promotes the involvement of employees and active residents to solve social problems in the regions where it operates.
We rolled out a number of socially significant projects in 2023, including financial assistance to socially vulnerable groups: coal purchases, food aid, school supplies, New Year presents, as well as a number of other socially significant initiatives.
Kazatomprom also pays great attention to supporting war veterans and retired former employees. To mark Victory Day, our enterprises held events to honour veterans of the Great Patriotic War and home front workers: presenting gifts and providing necessary assistance.
We spent a total of KZT 231.3 million on this area.
PLANS FOR 2024 AND A SHORT TERM
The following social projects are scheduled for 2024:
- The Igilik social project focused on socio-economic and infrastructural development, solving social problems in the regions where the Company operates, and improving working conditions at the Company's production facilities based on the initiatives and proposals submitted by employees of the Company, subsidiaries and affiliates, local governments, local communities and CSOs.
- Construction and repair of social infrastructure facilities, construction of children's and sports grounds.
- Assistance to socially vulnerable groups (war veterans, pensioners, large families, etc.)
- Community events in villages where the Company operates.
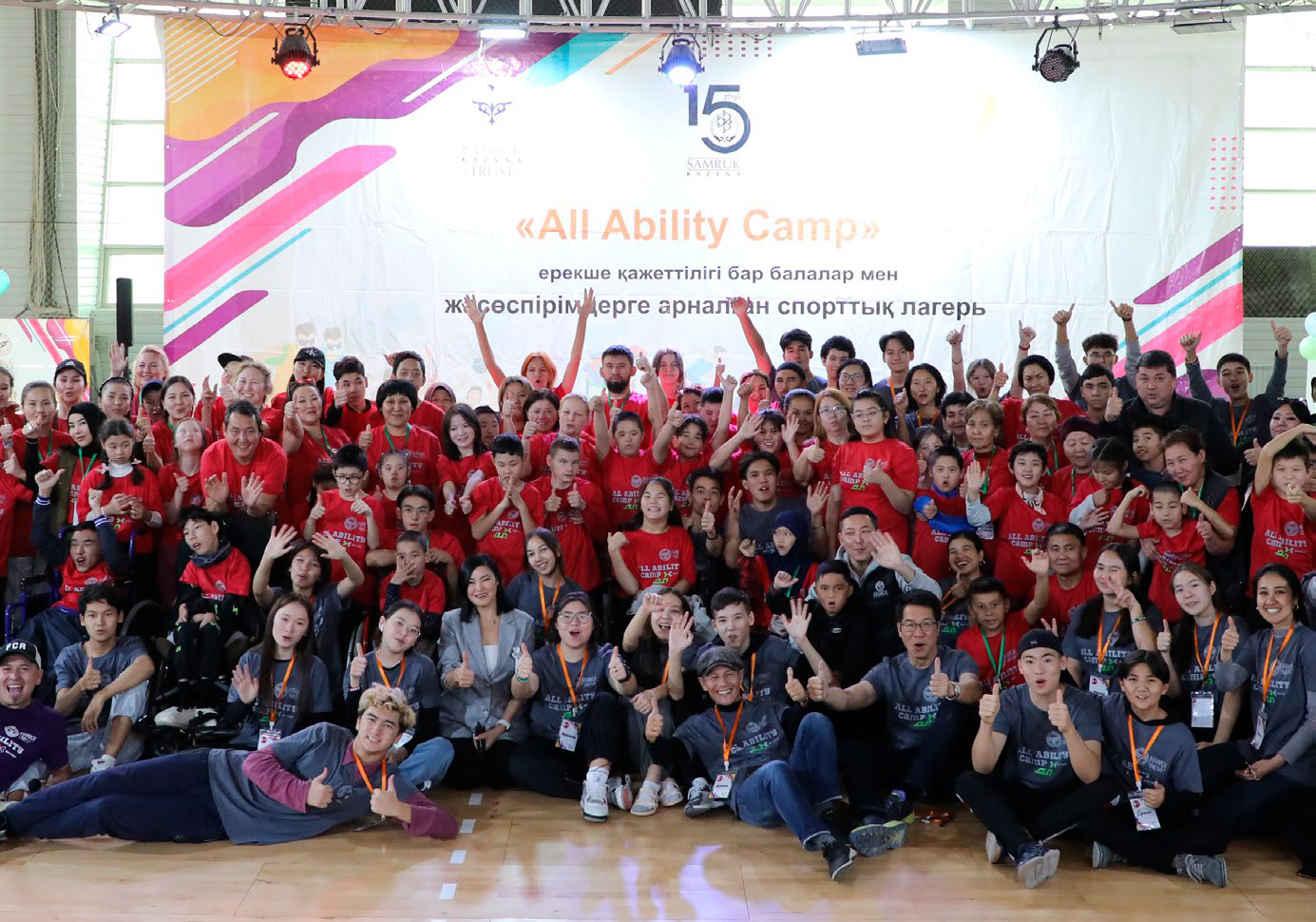
Supply Chain
MANAGEMENT APPROACH
NAC Kazatomprom JSC is a national Kazakh operator and a global leader of natural uranium mining industry. Kazatomprom's business and the vast geography of its operations requires efficient, timely, and complete provision of the necessary resources, combined with the best procurement terms and conditions.
Responsible procurements contribute to the development of mutually beneficial partnerships, increase the efficiency of interaction with suppliers and contractors, as well as improve control and transparency of procurement activities within the supply chain.
The Group’s main procurement priorities:
- enhancing the transparency of processes via automation and digitalisation;
- optimising the procurement management structure at the Company, subsidiaries and affiliates;
- developing the category management and strategies in procurement.
The Procurement Department headed by the Managing Director for Procurement and General Affairs is responsible for procurements. The department is making efforts to maximise the business value ensuring quality, timeliness, safety, efficiency, and risk mitigation. To this end, Kazatomprom keeps expanding the professional competencies of the Procurement Department employees and applying new technological solutions.
In procurements, Kazatomprom follows the Procedures for Procurement by Sovereign Wealth Fund Samruk- Kazyna JSC and legal entities where 50+ percent of voting shares (equity interests) are directly or indirectly owned by Samruk-Kazyna JSC (ownership or trust management74).
74 Approved by Resolution No.193 of the Board of Directors of Samruk-Kazyna JSC of 3 March 2022.
Procurement processes to meet the needs of the Company are regulated within the framework of the established rules, which are strictly observed. Procurement processes are automated in the zakup.sk.kz system. Competitive procurement is preferred, with strict compliance with the principles of publicity and transparency. In addition, with government support, we make preferences for domestic producers and work to support import substitution and the development of new production facilities.
Under the Procurement Procedure, long-term mutually beneficial cooperation has been established with the key suppliers of strategically important goods for the Company, and all supply chains, logistics and storage systems have been streamlined to ensure continuous production. All requirements for responsible business conduct are reflected in the contracts and are strictly followed by both suppliers and the Company.
SUMMARY OF KAZATOMPROM’S PROCUREMENTS
The total procurements under the Procurement Plans for the Company’s Group reached KZT 339.6 billion.
The Company concluded contracts amounting to a total of KZT 314.3 billion. At the same time, the procurement targets were met 92.5%.
Single source procurements made KZT 106.4 billion or 33.8% of the total procurements.
Procurements under the Invitation to Tender/Request for Quotation (ITT/RFQ) arrangements made KZT 207.9 billion or 66% of the total procurements.
To increase the share of competitive purchases, the Company interacts with potential suppliers to clarify the terms and conditions of registration and submission of tender documents, and eliminates excessive requirements for suppliers and administrative costs that do not affect the production process.
Additionally, to improve the procurement process in line with international best practices, in 2023 the Company developed an ESG supplier questionnaire on quality management system, environment, supply chain security, occupational health and safety, etc. Kazatomprom's Standard Procurement Contract for Goods, Works and Services obliges suppliers to complete the ESG questionnaire. Based on the results of questionnaires, the Company plans internal analyses of the suppliers' ESG practices development.
PLANNED AND ACTUAL BENEFITS OF CATEGORY PROCUREMENTS (CATEGORY PROCUREMENT MANAGEMENT)
In 2023, the Company implemented three procurement category strategies in accordance with the Procurement Plan 2023.
By implementing the procurement category strategies, the Company achieved actual benefits of KZT 2.57 billion.
Category strategies of the Company in 2023:
- Pipes.
- IT equipment.
- Protective clothing.
SUPPORT OF LOCAL SUPPLIERS
To comply with the public policy, NAC Kazatomprom JSC supports local suppliers.
In 2023, the Company continued controlling the procurements of goods produced by domestic producers in the light, furniture, food industries, as well as in the production of construction, engineering, chemical and pulp and paper products from manufacturers listed on the Samruk-Kazyna’s Register.
EST procurements accounted for 72% of the total procurements under the EST List in accordance with the established indicators in procurement (report as of 21 February 2024).
50 off-take contracts concluded under the Programme for Facilitation of Creation of New Production in the reporting period amounted to KZT 1.2 billion.
The Central Project Office engaging the Company’s subsidiaries and affiliates continues its work at the platform of Samruk-Kazyna Contract LLP to support domestic producers. The platform is used to conclude off-take contracts with producers. In addition, works are underway to search for new domestic producers adapted to the needs of the industry.
In 2023, we changed the local content calculation methodology to distinguish between indicators for goods and works/services.
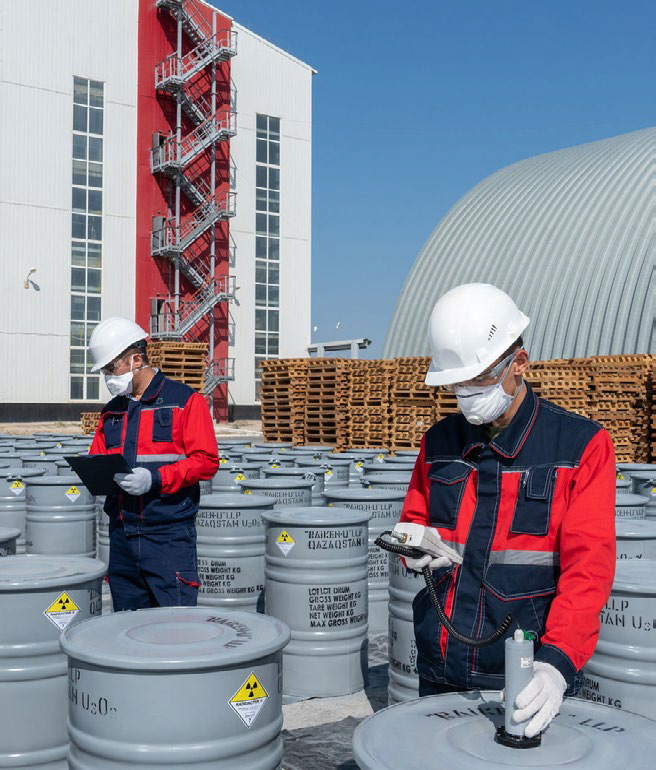
In 2023, we reached the following indicators for:75
The local content in goods
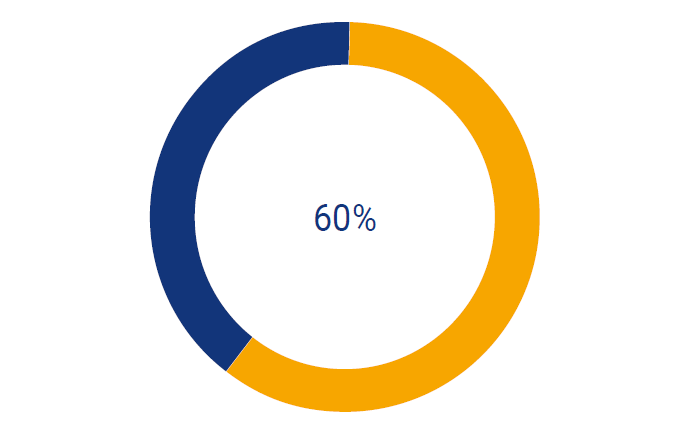
The local content in works and services
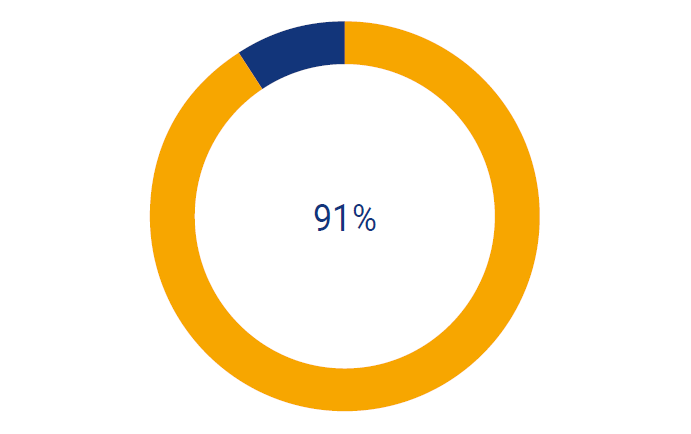
75 As of 23 January 2024.
In 2023, we also observed a decline in the local content in goods due to a shortage of sulphuric acid supply from local producers.
Suppliers by region
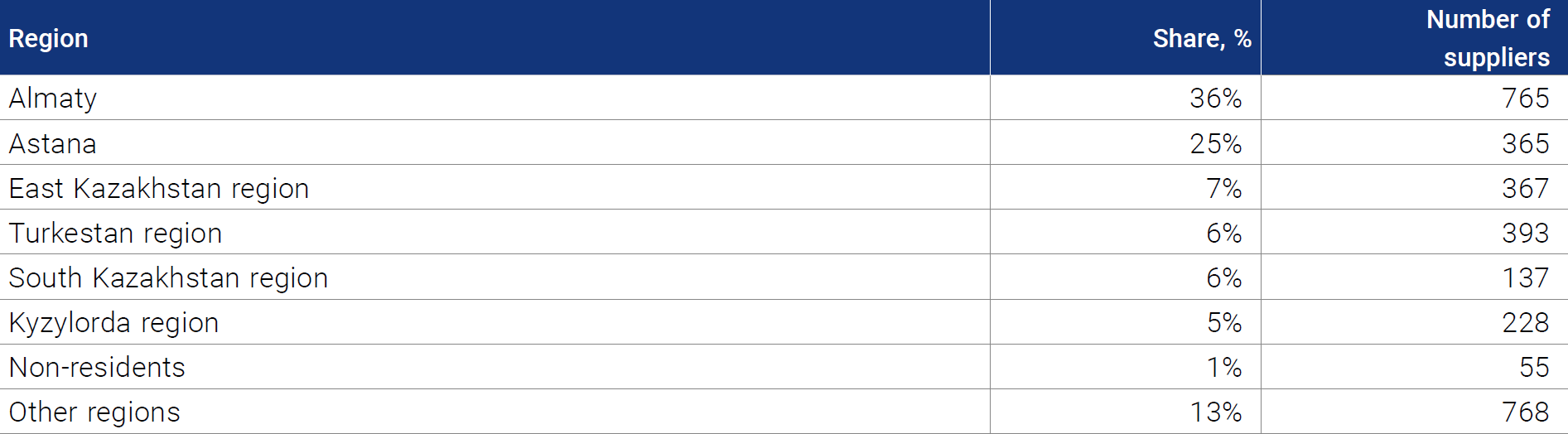
In 2023, the share of local suppliers was 98%. The share of goods, works and services purchased from local suppliers is 99%.

PLANS FOR 2024 AND A SHORT TERM:
- Continue optimising procurement processes and developing procurement automation;
- Continue implementing initiatives for proper separation of duties and access control within the framework of SAP implementation as the Group's ERP system.
- Information, analyses and data are for subsidiaries and affiliates where 50+ percent of voting shares (equity interests) are directly or indirectly owned by Samruk-Kazyna JSC (ownership or trust management).
Science and Innovations
MANAGING R&D AND INNOVATIONS
R&D and innovations play a key role in achieving Kazatomprom's strategic goals of maintaining production output, increasing operational efficiency and minimising negative environmental footprint.
The following companies make a key contribution to the implementation of strategic tasks on R&D and innovation management aimed at increasing the value and scientific component of Kazakhstan's uranium products:
- Volkovgeologia JSC: geology, geotechnology and mining and preparation operations, repair and restoration works of wells and associated extraction of rare metals and rare earth metals at uranium deposits;
- High Technology Institute LLP: research and design works related to the mining and processing of uranium;
- Ulba Metallurgical Plant JSC: advanced technologies of the nuclear fuel cycle (NFC), production and processing of rare metals (RM) and rare-earth metals (REM);
- NAC Kazatomprom JSC: intellectual property commercialisation, scientific personnel training and technology transfer.
The Department of Scientific and Technological Projects of NAC Kazatomprom JSC is responsible for the general coordination of R&D activities, as well as for the management and commercialisation of intellectual property.
Scientific and technological development:
- Updated Standard Organisation of Research and Development Activities;
- Approved Standard Organisation and Management of Intellectual Activity;
- Updated Standard Guidelines for Lean Production and Rationalisation Activities of NAC Kazatomprom JSC;
- Approved the Programme of scientific and technological development in the field of RM and REM, creation of new types of products and improvement of technologies for associated extraction of useful valuable components at Kazatomprom’s enterprises to organise high-tech production for 2022-2029;
- Approved the Action Plan for the transcontinental project to obtain medical radioisotopes (225Ac, 131I, 226Ra, etc);
- In 2023, 64 R&D contracts were concluded for a total amount of KZT 6.839 billion, excluding VAT;
- Filed 30 intellectual property applications, including 2 PCT international patent applications.
- Obtained 22 titles of protection.
Results in 2023
- Within the framework of the priority areas of scientific and technological work, the Group held 17 meetings of Scientific and Technical Councils.
- The Kazatomprom’s Expert Commission on Intellectual Property held 6 meetings.
- The Company held 2 meetings of the Platform (on the basis of JV Inkai LLP and Baiken-U LLP) to review the status of R&D performed and the results of R&D performed by Kazatomprom's subsidiaries and affiliates.
The Company and its subsidiaries and affiliates have 422 employees engaged in R&D activities. The Company has a research and design institute (High Technology Institute LLP), as well as research and production units of the enterprises (Ulba Metallurgical Plant JSC, Volkovgeologiya JSC).
KZT 1.372 billion, VAT excluding, was the total amount of R&D contracts concluded in 2023 by Kazatomprom and its subsidiaries and affiliates, of which 24 contracts were signed by subsidiaries and affiliates (KZT 1.332 billion) and 1 contract by Kazatomprom (KZT 0.040 billion). Also in 2023, the Company worked on 39 contracts transferred from previous years (total of KZT 5.467 billion).
The Company utilized KZT 2.623 billion in 2023, including KZT 0.151 billion under contracts of Kazatomprom and KZT 2.472 billion under contracts of subsidiaries and affiliates.
To commercialise the R&D results, Kazatomprom signed three contracts in 2023 to grant the right to use its inventions:
- Recovery of a chemical concentrate of natural uranium between Kazatomprom and JV Southern Mining and Chemical Company LLP
- Mobile unit for chemical treatment of process wells between Kazatomprom and Baiken-U LLP
- Recovery of a chemical concentrate of natural uranium between Kazatomprom and Karatau LLP
In addition, work on commercialisation of NAC Kazatomprom JSC's intellectual property continues on an ongoing basis.
Negotiations are also underway to sign licence agreements between NAC Kazatomprom JSC and its subsidiaries and affiliates (APPAK LLP and Baiken-U LLP) on granting the right to use the invention “Method for obtaining natural uranium concentrate”.
Scientific developments
Almost all R&D projects of the Group seek to improve and upgrade production. Several major R&D projects were implemented in 2023:
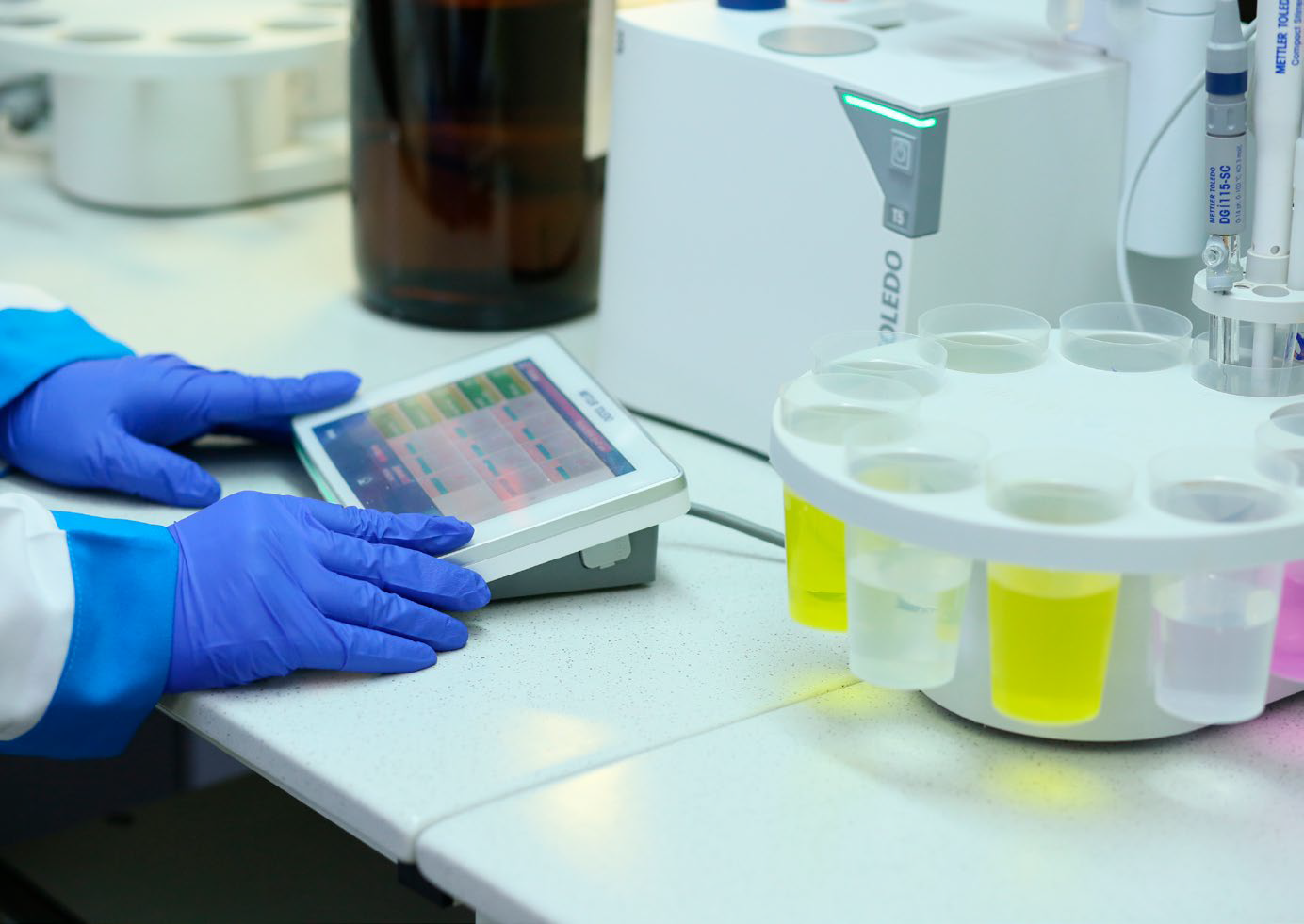
Projects | Description |
---|---|
Development of a software product for managing downhole pumping equipment |
|
Development of a technology for retrieving casing pipes with minimal defects from spent process wells and development of proposals for their further use |
|
Development and production of a prototype, a new generation unified modular drilling unit for uranium deposits, with the possibility of hybrid flushing and automated online system for transferring data of technological parameters |
|
The Science and Technology Projects Department initiated a number of R&D projects on rare and rare-earth metals: | |
Exploratory studies on the application of nanofiltration method in the associated extraction of scandium from uranium sorption mother liquors |
|
Assessment of the possibility of obtaining vanadium from sorption mother liquors during uranium mining at the Zarechnoye deposit |
|
Assessment of resource potential, development and testing of technology for extraction of gold and associated valuable metals from spent and operating blocks of uranium deposits |
|
Development of a technology for utilisation of spent ion exchange resins at subsidiaries and affiliates with associated extraction of valuable components, in particular, RMs and REMs |
|
In 2023, we continued working on several studies aimed at improving the environmental safety of operations: | |
Conducting comprehensive environmental and social research for sustainable development (GRI standards) |
|
Conducting research to optimise the processes of handling production and consumption waste at the enterprise in accordance with the Environmental Code of the Republic of Kazakhstan and GRI standards |
|
In 2023, work began on joint R&D projects between NAC Kazatomprom JSC and Orano Mining in the following areas:
- Geology and exploration;
- PES deposits;
- Uranium reprocessing;
- Environment.
Also in 2023, the RM and RSM Science and Technology Development Programme worked on the technological design of a mobile unit to obtain ammonium perrenate, aimed at the production of a mobile unit to obtain an ammonium perrenate of technical purity (Re at least 60 per cent), the development of a hardware and technology scheme and the conduct of tests on a mobile installation, using uranium ion exchange resin as a source of ironing, and the development of technological regulations for the extraction of rubber on a mobile plant and the design and design of a mobile plant; a mobile installation to obtain an ammonium perrenate of technical purity was constructed and launched; work on the development of an experimental batch of ammonium perrenate was planned in 2024.
Innovations
The Group activates the innovative activity of its employees through mechanisms for submitting, processing, evaluating, and reviewing innovation proposals. An additional incentive for innovations is an annual contest of innovations held among subsidiaries and affiliates.
Results in 2023:
- The Group's employees submitted 2,843 innovation proposals, of which 2,406 were accepted and 1,668 were implemented. KZT 2.54 billion is the expected economic effect of the implemented proposals.
Plans for 2024 and a short term:
Pursuing a new approach to R&D management, the Group will take the following actions in 2024:
- Updating the internal regulatory documents to raise 1% of funds from subsoil users for science.
- Revising the composition of scientific and technical councils.
- Continuing R&D coordination (initiation of new R&D, realisation and implementation of R&D results) through a platform for the presentation of completed research projects.
- Enhancing S&T cooperation with the scientific environment (science centres, universities, etc.).
The Company will also continue improving the competencies of subsidiaries and affiliates' employees involved in R&D. This will contribute to the improvement of the quality of R&D as part of the implementation of R&D licence terms and conditions.
DIGITALISATION AND IT
In the context of implementation of the strategic task "Digitalisation and transformation" to achieve the strategic goal "Apply best practices in business activities" of the Development Strategy of NAC Kazatomprom JSC for 2018-2028, the Company continued standardisation and optimisation of business processes, including the creation of a single vertical integrated IT infrastructure.
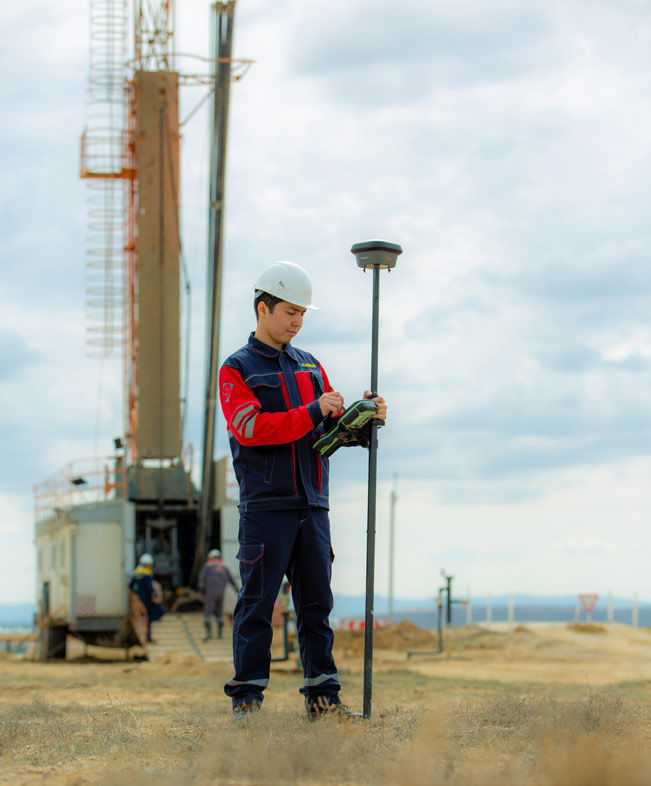
Key IT and digitalisation projects
Project | Purpose/Effect |
---|---|
Improving the efficiency of operations and decision-making | |
Unified Corporate Data Warehouse and Integration Bus |
|
IT architecture development | |
Providing Kazatomprom's mine workers with quality 4G mobile communication services |
|
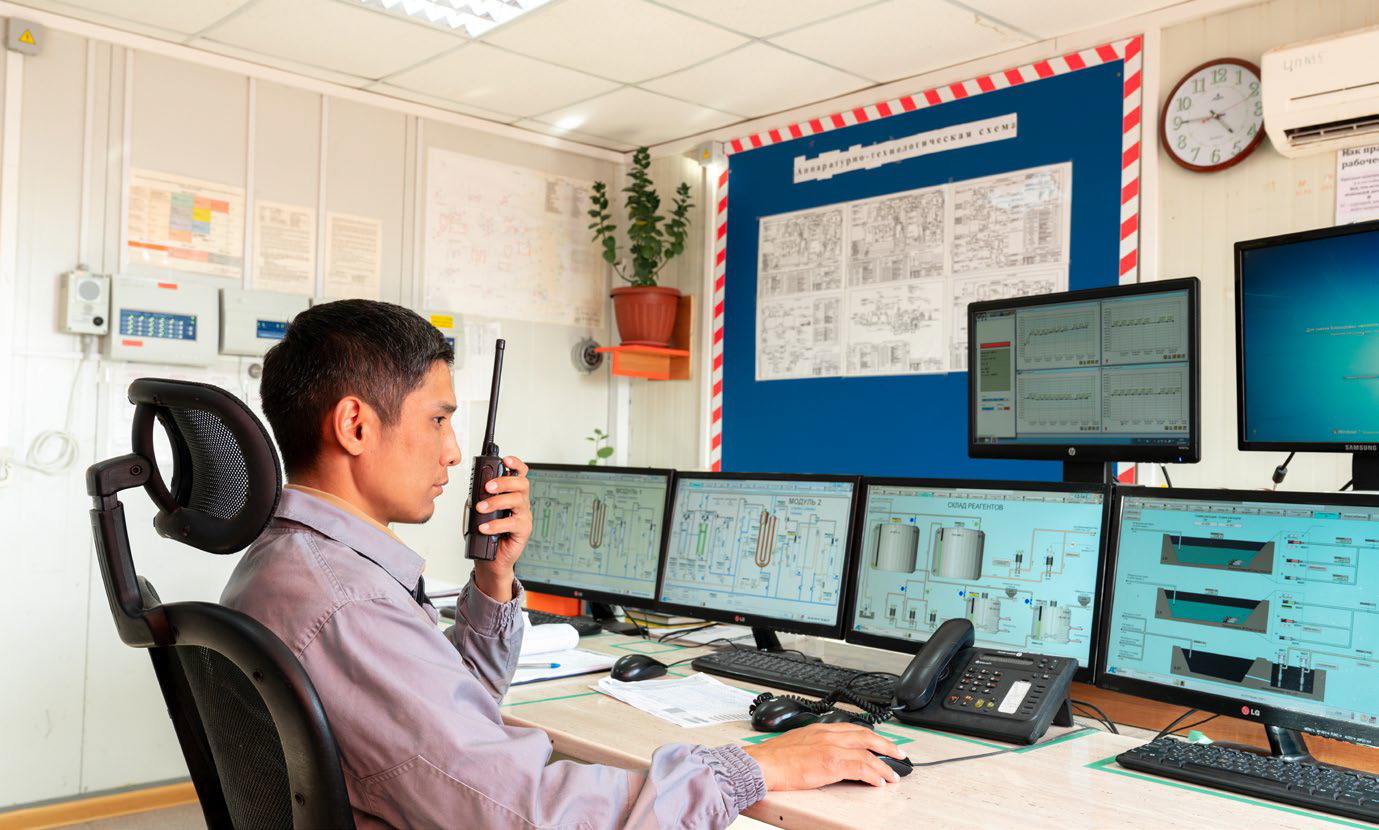
Information security
Transformation of business processes offers companies new perspectives for real-time decisionmaking, which drives productivity, flexibility and industry dynamism. However, it also reinforces the need for information security, cyber resilience and continuity of information systems.
To guarantee an adequate level of protection against cyber threats, Kazatomprom continuously monitors compliance with information security standards and strives to improve its information security management system in accordance with the laws of the Republic of Kazakhstan and international standards ISO/IEC 27001.
In accordance with the Action Plan for the creation of a Comprehensive Information Security Management System, as part of the strategic task "Digitalisation and Transformation" and to achieve the strategic objective "Use of Best Practices in Business" under the Development Strategy of NAC Kazatomprom JSC for 2018-2028, we continue working on the project "Cyber Security Development". The Company monitors and responds to information security incidents around the clock and actively cooperates with the Information Security Operations Centre and the National Information Security Coordination Centre. To raise awareness and prevent cyber threats, the Group regularly organises online training for employees, cyber-attack drills and special briefings.
In 2023, we registered and prevented a significant number of information security incidents in NAC Kazatomprom JSC and its subsidiaries and affiliates, as well as jointly controlled enterprises, and work is underway to prevent property and reputational damage to the Company.
To increase the awareness of personnel in the field of information security, as well as to inform about changes in internal documents regulating information security requirements, the Company introduced an information system that allows for interactive online training for employees of the Company and its subsidiaries and affiliates. In 2023, we conducted training for all employees of NAC Kazatomprom JSC and all subsidiaries and affiliates.
We were implementing initiatives to improve cyber hygiene and digital security under information security co-operation arrangements. There is also active participation in forums and events aimed at discussing digitalisation processes in the nuclear industry and strategies for the development of information technology and information security systems.
Plans for information security development in 2024
Kazatomprom will continue to monitor compliance with information security requirements in all existing and developing IT systems as well as arrange initiatives to strengthen cybersecurity, awareness of information security issues and protection of confidential information.
In addition, the Company intends to:
- Continue to improve and replicate the processes of the comprehensive information security management system in accordance with the Information Security Strategy of NAC Kazatomprom JSC for 2019-2028.
- Continue the implementation of the Cybersecurity Implementation and Development project.
- Continue the implementation of the Information Security Management System Improvement Plan for 2024.
- Continue the automation of Information Security Management System (ISMS).
- Develop a unified approach to ensuring the information security of automated control systems of subsidiaries and affiliates based on the results of pilot projects of information security systems in automated control systems.
- Continue IS-related cooperation with GTS JSC and Information Security Committee of the Ministry of Digital Development, Innovations, and Aerospace Industry of Kazakhstan.